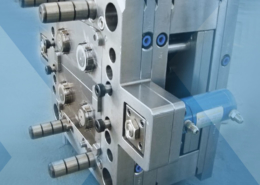
Understanding Injection Molding Price Dynamics
Author:gly Date: 2024-06-08
Introduction:
Injection molding is a cornerstone process in modern manufacturing, serving industries ranging from automotive to consumer goods. One of the critical aspects influencing decision-making in this realm is the pricing structure associated with injection molding. Understanding the factors that contribute to injection molding prices is crucial for businesses aiming to optimize costs while maintaining quality standards.
Market Demand
Market demand plays a pivotal role in shaping injection molding prices. Fluctuations in demand, influenced by consumer trends, economic conditions, and industry-specific factors, directly impact pricing dynamics. During periods of high demand, such as the release of new consumer electronics or automotive models, injection molding prices may surge due to increased competition for manufacturing resources and capacity constraints. Conversely, during economic downturns or lulls in product innovation cycles, pricing pressures may ease as suppliers compete for a smaller pool of projects.
Furthermore, the geographical distribution of demand can also affect prices. Regions with higher concentrations of manufacturing facilities may experience greater competition, leading to more competitive pricing compared to areas with limited supplier options.
Material Selection
The choice of materials is a critical determinant of injection molding prices. Different materials possess varying properties, such as strength, flexibility, and heat resistance, which influence their suitability for specific applications. High-performance engineering plastics command higher prices due to their superior characteristics and specialized production requirements. Conversely, commodity plastics like polyethylene and polypropylene are more cost-effective but may lack the desired performance attributes for certain applications.
Moreover, fluctuations in raw material prices, driven by factors like supply chain disruptions, geopolitical events, and environmental regulations, can directly impact injection molding costs. Manufacturers must stay vigilant and adapt their pricing strategies to reflect changes in material costs to maintain profitability.
Production Volume
Production volume is a key determinant of injection molding pricing. Economies of scale dictate that larger production runs typically result in lower per-unit costs due to spreading fixed expenses across a greater number of parts. Manufacturers offering injection molding services often provide tiered pricing structures based on volume commitments, incentivizing clients to place larger orders.
However, smaller production runs may incur higher setup costs, tooling expenses, and overhead, leading to comparatively higher unit prices. Factors such as part complexity, tolerances, and finishing requirements can also influence production costs, further complicating pricing calculations.
Technological Advancements
Technological advancements in injection molding processes and equipment have a significant impact on pricing dynamics. Innovations such as computer-aided design (CAD), simulation software, and automation systems have streamlined workflows, improved efficiency, and enhanced product quality. While initial investments in advanced technology may be substantial, the long-term benefits in terms of reduced cycle times, scrap rates, and labor costs can outweigh the initial outlay.
Additionally, advancements in materials science, such as the development of bio-based polymers and recyclable plastics, offer environmentally conscious solutions but may come with a premium price tag. Manufacturers must weigh the benefits of adopting new technologies against their associated costs to remain competitive in the market.
Supplier Relationships
The nature of supplier relationships can significantly impact injection molding prices. Long-term partnerships built on trust, reliability, and mutual benefit often result in preferential pricing arrangements and collaborative problem-solving. Suppliers may offer discounts, expedited lead times, or value-added services to loyal clients, thereby fostering a symbiotic relationship that benefits both parties.
Conversely, transactional relationships characterized by price-focused negotiations and minimal engagement may result in higher costs and reduced flexibility. Suppliers may prioritize clients with whom they have established strong relationships, potentially disadvantaging newcomers or infrequent buyers.
Conclusion:
In conclusion, injection molding pricing is a multifaceted aspect of manufacturing that encompasses various factors, including market demand, material selection, production volume, technological advancements, and supplier relationships. Businesses must navigate these complexities strategically to optimize costs while meeting quality standards and customer expectations. By understanding the underlying dynamics driving injection molding prices, manufacturers can make informed decisions to enhance competitiveness and profitability in an ever-evolving market landscape.
Word Count: 748
GETTING A QUOTE WITH LK-MOULD IS FREE AND SIMPLE.
FIND MORE OF OUR SERVICES:
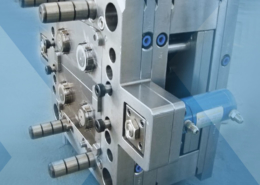
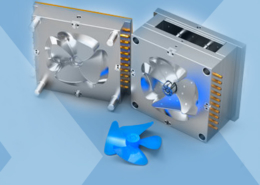
Plastic Molding

Rapid Prototyping
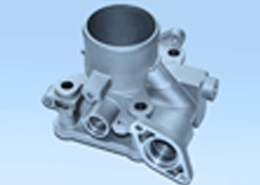
Pressure Die Casting
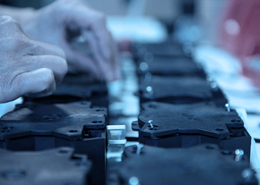
Parts Assembly
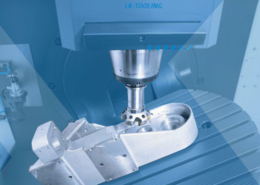