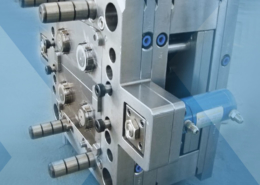
Deciphering Injection Molding Mold Costs
Author:gly Date: 2024-06-08
Introduction:
Injection molding is a cornerstone of modern manufacturing, enabling the mass production of intricate plastic components. Central to this process is the injection molding mold, a critical tool that shapes the final product. Understanding the intricacies of injection molding mold costs is essential for businesses seeking to optimize their manufacturing processes while managing expenses effectively.
Mold Material Selection
The choice of mold material significantly influences injection molding mold costs. Various materials, such as steel, aluminum, and pre-hardened steel, offer distinct advantages in terms of durability, heat conductivity, and machining properties. While steel molds are durable and well-suited for high-volume production, they entail higher initial costs due to material expenses and longer machining times. In contrast, aluminum molds are more cost-effective upfront but may require frequent replacement or refurbishment, leading to higher lifecycle costs. Selecting the optimal mold material involves balancing upfront investment with long-term maintenance considerations to achieve cost-efficient production.
Mold Complexity and Design
The complexity of mold design directly impacts injection molding mold costs. Intricate geometries, undercuts, and complex parting lines necessitate specialized machining techniques and longer lead times, driving up manufacturing expenses. Simple, straightforward molds are typically more cost-effective to produce due to reduced machining complexity and shorter production cycles. Additionally, innovative design features, such as conformal cooling channels and interchangeable inserts, can optimize cycle times and improve part quality but may entail higher initial investment costs. Manufacturers must carefully evaluate the trade-offs between mold complexity, production efficiency, and overall cost to achieve the desired balance.
Tooling and Equipment
Investments in tooling and equipment constitute a significant portion of injection molding mold costs. High-precision CNC machining centers, EDM (Electrical Discharge Machining) equipment, and surface finishing tools are essential for fabricating molds with tight tolerances and smooth surface finishes. Additionally, auxiliary equipment such as mold bases, inserts, and hot runners contribute to the overall cost of mold fabrication. Upgrading to advanced technologies, such as rapid tooling prototyping and multi-cavity molds, can enhance productivity and reduce lead times but may entail higher upfront expenses. Manufacturers must carefully assess their equipment needs and investment priorities to maximize operational efficiency and minimize production costs.
Supplier Relationships and Outsourcing
The choice of mold supplier and outsourcing strategy can impact injection molding mold costs significantly. Establishing partnerships with reputable mold makers and leveraging their expertise can result in cost savings through streamlined processes, value engineering, and collaborative problem-solving. Outsourcing mold fabrication to low-cost regions may offer initial cost advantages but can lead to quality issues, communication challenges, and longer lead times, ultimately affecting overall project costs. Manufacturers must weigh the benefits of outsourcing against potential risks and consider factors such as intellectual property protection, regulatory compliance, and supply chain resilience when making sourcing decisions.
Conclusion:
In conclusion, injection molding mold costs are influenced by various factors, including mold material selection, complexity of design, investments in tooling and equipment, and supplier relationships. By understanding these dynamics and making informed decisions, manufacturers can optimize their mold fabrication processes, enhance product quality, and manage costs effectively. Continuous innovation in mold design and manufacturing technologies presents opportunities for cost reduction and process optimization, ensuring competitiveness in an evolving market landscape.
Word Count: 572
GETTING A QUOTE WITH LK-MOULD IS FREE AND SIMPLE.
FIND MORE OF OUR SERVICES:
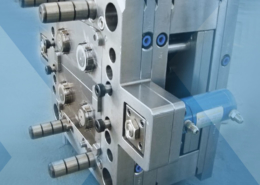
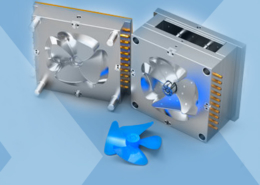
Plastic Molding

Rapid Prototyping
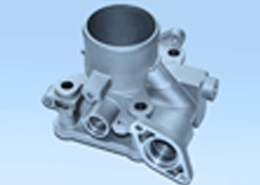
Pressure Die Casting
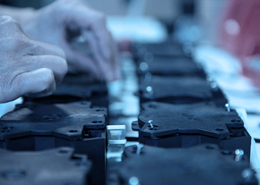
Parts Assembly
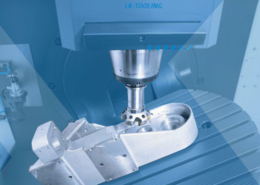