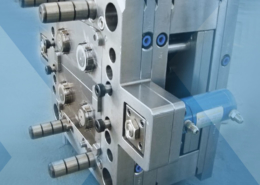
Exploring the World of Injection Molding Medical Plastics
Author:gly Date: 2024-06-08
In the dynamic landscape of healthcare, the role of injection molding medical plastics is paramount, revolutionizing the production of critical components for medical devices and equipment. In this comprehensive exploration, we delve into the fascinating realm of injection molding medical plastics, uncovering its significance, applications, advancements, and future prospects.
Introduction
Injection molding medical plastics stands at the intersection of healthcare innovation and manufacturing excellence, facilitating the production of intricate and precise components essential for medical devices, diagnostics, and equipment. With its ability to meet stringent regulatory requirements, maintain sterility, and ensure biocompatibility, injection molding plays a vital role in advancing medical te
for safer, more effective medical devices and equipment. Biocompatible polymers, bioresorbable materials, and antimicrobial additives are among the innovations driving the evolution of injection molding medical plastics, offering solutions that meet the stringent requirements of modern healthcare.
Design Optimization
Design optimization plays a crucial role in maximizing the performance and manufacturability of injection-molded medical components. Collaboration between designers, engineers, and manufacturing experts is essential to streamline the design process, minimize material waste, and optimize part geometry for injection molding. Utilizing advanced design tools such as computer-aided design (CAD), finite element analysis (FEA), and mold flow simulation enables the evaluation of design concepts, identification of potential issues, and optimization of part geometry, gating, and cooling systems. By integrating design for manufacturability (DFM) principles early in the product development process, manufacturers can reduce lead times, improve product quality, and lower production costs.
Regulatory Compliance
Navigating the complex regulatory landscape is a critical challenge in injection molding medical plastics, requiring thorough understanding and adherence to applicable regulations and standards. Manufacturers must ensure compliance with regulatory requirements related to material selection, manufacturing processes, quality management systems, and product testing and validation. Collaboration with regulatory experts, auditors, and certification bodies is essential to navigate the regulatory requirements effectively and obtain the necessary approvals and certifications for medical device components. By establishing robust quality management systems and documentation practices, manufacturers can demonstrate compliance with regulatory requirements and ensure the safety and efficacy of injection-molded medical products.
Conclusion
In conclusion, injection molding medical plastics play a pivotal role in the advancement of healthcare technology, enabling the production of high-quality, precision-engineered components for medical devices and equipment. With its ability to meet the stringent requirements of the healthcare industry, injection molding offers numerous advantages, including precision, scalability, and cost-effectiveness. By leveraging advancements in materials, technology, and regulatory compliance, manufacturers can address key challenges and unlock new opportunities for innovation in injection molding medical plastics.
As the healthcare landscape continues to evolve, injection molding will remain a cornerstone of medical device manufacturing, driving improvements in patient care, diagnostic accuracy, and therapeutic outcomes. By embracing collaboration, innovation, and continuous improvement, stakeholders across the medical device supply chain can harness the full potential of injection molding to address emerging challenges and deliver transformative solutions for the healthcare industry. Together, we can advance the frontiers of medical technology and improve the lives of patients worldwide through injection molding medical plastics.
GETTING A QUOTE WITH LK-MOULD IS FREE AND SIMPLE.
FIND MORE OF OUR SERVICES:
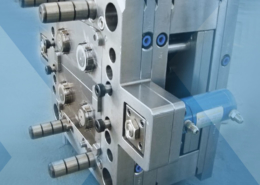
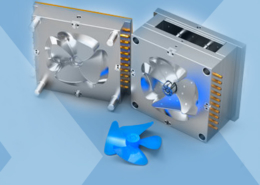
Plastic Molding

Rapid Prototyping
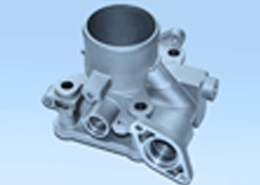
Pressure Die Casting
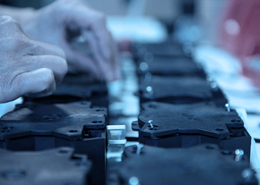
Parts Assembly
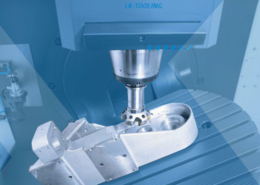