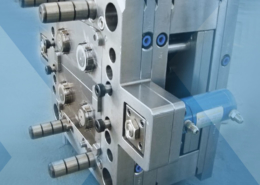
Exploring the Versatility of Injection Molding Services
Author:gly Date: 2024-06-08
Introduction:
Injection molding services stand as the cornerstone of modern manufacturing, revolutionizing industries with their efficiency and versatility. From consumer goods to automotive components, their impact spans wide. This article delves into the intricacies of injection molding services, providing a comprehensive overview of its processes, applications, and future prospects.
Process Overview
Injection molding entails injecting molten material into a mold cavity, where it solidifies to form the desired product. This process boasts remarkable precision, allowing for intricate designs and consistent quality. Initial steps involve melting the chosen material, typically thermoplastics, before it's injected under high pressure into the mold.
The mold, often made of steel or aluminum, defines the product's shape and features. Cooling channels within the mold facilitate rapid solidification, ensuring quick cycle times. Once solidified, the product is ejected, and the cycle repeats. This streamlined process enables mass production of complex parts with minimal waste.
Injection molding's efficiency and repeatability make it a preferred choice for high-volume production. Its adaptability to various materials, including polymers, metals, and ceramics, further enhances its appeal across diverse industries.
Applications Across Industries
Injection molding finds application in myriad industries, ranging from automotive and electronics to healthcare and consumer goods. In automotive manufacturing, it produces components such as bumpers, dashboards, and interior trim with superior strength and precision.
Electronics benefit from injection-molded casings, connectors, and housings, ensuring optimal functionality and durability. The medical sector relies on injection molding for producing sterile and biocompatible devices, including syringes, implants, and medical equipment components.
Consumer goods, including household appliances, toys, and packaging, leverage injection molding for cost-effective mass production without compromising quality. The versatility of this process enables the creation of intricate designs and textures, enhancing product aesthetics and functionality.
Advancements in Material Science
Material selection plays a pivotal role in injection molding, driving innovation and expanding application possibilities. Traditional thermoplastics offer a balance of strength, flexibility, and cost-effectiveness. However, recent advancements have introduced biodegradable polymers, reinforced composites, and conductive materials, catering to evolving consumer demands and environmental concerns.
These materials exhibit enhanced properties, such as improved strength-to-weight ratios, flame retardancy, and electrical conductivity, opening doors to novel applications in aerospace, renewable energy, and electronics.
Technological Innovations
The landscape of injection molding is continually evolving with technological advancements. Industry 4.0 initiatives integrate automation, robotics, and data analytics into molding processes, optimizing efficiency and quality control.
Additive manufacturing techniques, such as 3D printing, complement traditional injection molding, enabling rapid prototyping and on-demand production of customized components. Furthermore, simulation software simulates mold filling, cooling, and part shrinkage, facilitating design optimization and reducing time-to-market.
Conclusion:
In conclusion, injection molding services represent a cornerstone of modern manufacturing, driving innovation across diverse industries. From its precise processes and broad material capabilities to its myriad applications and technological advancements, injection molding continues to shape the future of production. As industries evolve and consumer demands shift, further research into sustainable materials and advanced manufacturing techniques will undoubtedly propel injection molding into new frontiers of efficiency and innovation.
GETTING A QUOTE WITH LK-MOULD IS FREE AND SIMPLE.
FIND MORE OF OUR SERVICES:
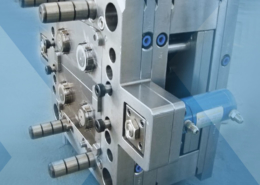
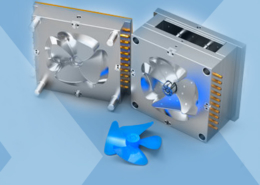
Plastic Molding

Rapid Prototyping
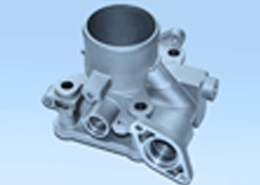
Pressure Die Casting
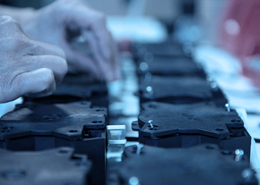
Parts Assembly
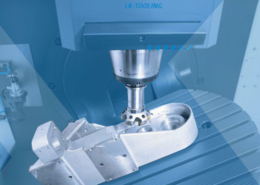