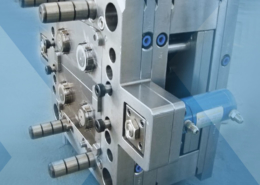
Exploring Bottle Cap Injection Molding: Revolutionizing Packaging Solutions
Author:gly Date: 2024-06-08
Bottle cap injection molding stands as a cornerstone of modern packaging manufacturing, offering innovative solutions for sealing bottles and containers across various industries. In this article, we delve into the intricacies of bottle cap injection molding, shedding light on its techniques, applications, benefits, and future prospects, thus sparking the reader's interest and providing essential background information.
Introduction to Bottle Cap Injection Molding
Bottle cap injection molding represents a critical process in the production of caps and closures for beverage, pharmaceutical, and household product containers. This manufacturing technique involves injecting molten plastic resin into a specialized mold cavity, where it solidifies to form precisely engineered bottle caps. With advancements in machinery, materials, and design capabilities, bottle cap injection molding offers unparalleled efficiency, reliability, and customization options in packaging production.
State-of-the-Art Molding Techniques
High-Speed Injection Molding
High-speed injection molding technology enables rapid production of bottle caps with minimal cycle times. By optimizing injection speed, cooling processes, and mold design, manufacturers can achieve high throughput and cost efficiency in mass-producing bottle caps for large-scale beverage and consumer goods markets. High-speed injection molding also ensures consistent quality and dimensional accuracy, meeting the stringent requirements of modern packaging applications.
Multi-Cavity Molding
Multi-cavity molding allows simultaneous production of multiple bottle caps within a single mold, maximizing productivity and resource utilization. By incorporating multiple cavities into the mold design, manufacturers can significantly increase output while minimizing production costs and lead times. Multi-cavity molding is particularly advantageous for high-volume production runs, where economies of scale and efficiency gains are essential for competitive packaging solutions.
Threaded Cap Molding
Threaded cap molding involves the production of bottle caps with screw-on or twist-off features, ensuring secure sealing and tamper resistance. This specialized molding technique requires precision tooling and tight tolerances to achieve accurate thread profiles and seamless cap operation. Threaded cap molding is widely used in pharmaceutical, food and beverage, and personal care industries, where product integrity and consumer safety are paramount.
Applications Across Industries
Beverage Packaging
In the beverage industry, bottle cap injection molding plays a crucial role in sealing various liquid products, including water, soda, juice, and alcoholic beverages. Bottle caps must withstand rigorous handling, transportation, and storage conditions while preserving product freshness and preventing leakage. With advancements in material science and design engineering, bottle cap manufacturers can tailor solutions to meet the unique requirements of different beverage applications, ensuring consumer satisfaction and brand loyalty.
Pharmaceutical Packaging
Pharmaceutical packaging demands stringent quality standards and regulatory compliance to ensure the safety and efficacy of medicinal products. Bottle cap injection molding provides pharmaceutical companies with reliable sealing solutions for liquid medications, tablets, and capsules. Tamper-evident features, child-resistant designs, and compatibility with various container materials are essential considerations in pharmaceutical cap manufacturing, driving innovation and continuous improvement in packaging technology.
Personal Care and Household Products
Personal care and household product manufacturers rely on bottle cap injection molding to deliver convenient and functional packaging solutions to consumers. From shampoo and conditioner bottles to cleaning agents and detergents, bottle caps serve as the first line of defense against product contamination and spillage. Manufacturers leverage custom molding capabilities to create aesthetically pleasing designs, ergonomic features, and brand-specific branding elements, enhancing product differentiation and consumer appeal.
Advantages and Future Directions
Bottle cap injection molding offers numerous advantages, including design flexibility, cost efficiency, and scalability. Future directions may include the integration of smart packaging technologies, such as RFID tags and NFC labels, to enable product tracking, authentication, and interactive consumer engagement. Additionally, advancements in sustainable materials, biodegradable resins, and circular economy initiatives hold promise for reducing environmental impact and promoting eco-friendly packaging solutions.
Conclusion
In conclusion, bottle cap injection molding stands at the forefront of packaging innovation, driving efficiency, functionality, and sustainability in consumer goods manufacturing. By leveraging state-of-the-art molding techniques, materials, and design capabilities, manufacturers can meet the evolving needs of diverse industries and consumers worldwide. As we look towards the future, continued investment in research, technology, and sustainability initiatives will pave the way for the next generation of bottle cap injection molding solutions, shaping the landscape of packaging for years to come.
GETTING A QUOTE WITH LK-MOULD IS FREE AND SIMPLE.
FIND MORE OF OUR SERVICES:
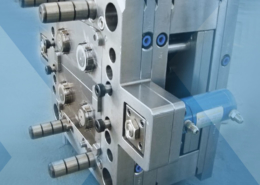
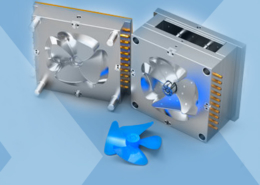
Plastic Molding

Rapid Prototyping
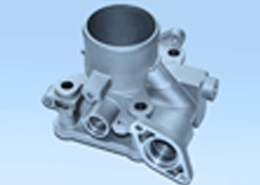
Pressure Die Casting
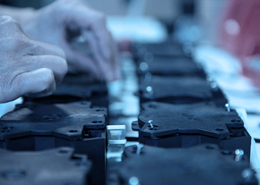
Parts Assembly
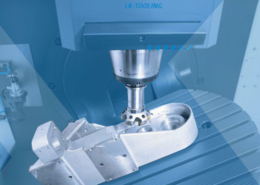