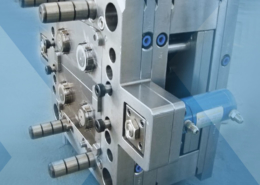
Exploring the World of Bobbin Molding
Author:gly Date: 2024-06-08
Bobbin molding, a specialized form of injection molding, holds a pivotal role in the manufacturing of components crucial for various industries. From electrical appliances to automotive systems, the precision and efficiency of bobbin molding contribute significantly to the production of high-quality parts. This article provides an in-depth exploration of bobbin molding, shedding light on its processes, applications, innovations, challenges, and future prospects.
Unveiling Bobbin Molding: A Brief Introduction
Bobbin molding, also known as coil winding, refers to the process of encapsulating electrical components, such as coils and transformers, within thermoplastic or thermosetting materials. The technique involves intricately winding conductive wires onto a cylindrical or spool-like core, followed by injection molding to encapsulate the assembly in a protective casing. This encapsulation not only safeguards the delicate components from environmental factors but also enhances their durability and functionality.
Historical Context
The roots of bobbin molding can be traced back to the early 20th century, coinciding with the rise of electrical engineering and the demand for compact and reliable components. Over the decades, advancements in materials science, molding technologies, and automation have propelled bobbin molding into a cornerstone of modern electronics manufacturing.
Process Overview
The bobbin molding process comprises several stages, including coil winding, core assembly, mold setup, injection, curing (in the case of thermosetting materials), and finishing. Each step demands meticulous attention to detail and precise control of parameters such as temperature, pressure, and material flow to ensure the integrity and performance of the final product.
Diverse Applications Across Industries
Electronics
In the electronics industry, bobbin molding finds extensive use in manufacturing transformers, inductors, solenoids, and other electromagnetic components. The encapsulation provided by bobbin molding not only protects these components from moisture, dust, and mechanical stress but also facilitates efficient heat dissipation and electrical insulation, ensuring optimal performance and longevity.
Automotive
The automotive sector relies on bobbin molding for the production of ignition coils, sensor modules, and powertrain components. The compactness, reliability, and thermal stability offered by bobbin-molded components are critical for the demanding operating conditions of modern vehicles, contributing to enhanced fuel efficiency, emissions control, and overall performance.
Renewable Energy
In the renewable energy sector, bobbin molding plays a vital role in the manufacturing of wind turbine generators, solar inverters, and energy storage systems. The encapsulation of sensitive electronic components ensures the robustness and longevity of these systems, enabling the efficient harnessing and distribution of clean energy.
Innovations Driving Progress
Material Advancements
Ongoing research in polymer chemistry has led to the development of specialized materials tailored for bobbin molding applications. High-temperature thermoplastics, flame-retardant resins, and electrically conductive polymers offer improved performance, reliability, and safety, expanding the capabilities of bobbin-molded components in diverse industries.
Miniaturization and Integration
Advancements in microelectronics and miniaturization techniques have enabled the production of smaller and more integrated bobbin-molded components. This trend towards compactness and multifunctionality not only optimizes space utilization but also reduces manufacturing costs and enhances system efficiency, particularly in portable devices and IoT applications.
Automation and Robotics
The integration of automation and robotics in bobbin molding processes streamlines production workflows, enhances process repeatability, and reduces labor costs. Robotic systems for coil winding, mold handling, and quality inspection enable high-throughput manufacturing with minimal human intervention, improving overall productivity and quality control.
Challenges and Future Directions
Design Complexity
The increasing complexity of electronic systems poses challenges in designing and molding intricate bobbin-wound components. Innovations in CAD software, mold design methodologies, and simulation tools are needed to optimize component geometries, ensure uniform material distribution, and minimize manufacturing defects.
Sustainability Considerations
As the demand for environmentally friendly manufacturing practices grows, the bobbin molding industry faces pressure to reduce its environmental footprint. Strategies such as recycling of molding materials, use of biodegradable resins, and adoption of energy-efficient processes are essential for achieving sustainability goals while maintaining competitiveness in the market.
Regulatory Compliance
Stringent regulations governing the use of hazardous substances and the disposal of electronic waste pose compliance challenges for bobbin molding manufacturers. Continuous monitoring of regulatory developments, adherence to industry standards, and proactive engagement with stakeholders are essential for navigating the evolving regulatory landscape and ensuring product compliance.
Conclusion and Future Outlook
In conclusion, bobbin molding stands as a versatile and indispensable manufacturing technique, driving innovation and progress across industries. By leveraging advancements in materials science, automation, and design optimization, manufacturers can overcome challenges and unlock new opportunities for enhancing the performance, reliability, and sustainability of bobbin-molded components. Looking ahead, continued collaboration between industry stakeholders, academia, and policymakers will be crucial for shaping the future of bobbin molding and realizing its full potential in the evolving landscape of electronics manufacturing.
GETTING A QUOTE WITH LK-MOULD IS FREE AND SIMPLE.
FIND MORE OF OUR SERVICES:
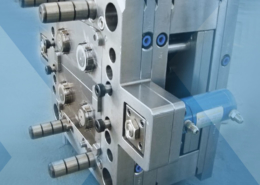
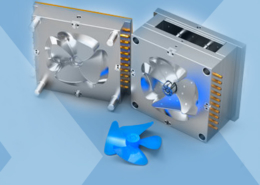
Plastic Molding

Rapid Prototyping
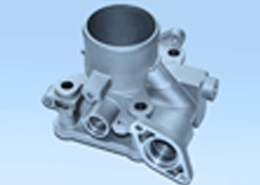
Pressure Die Casting
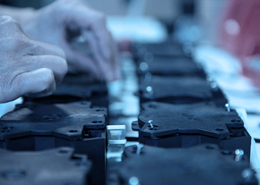
Parts Assembly
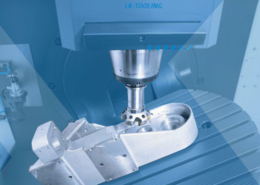