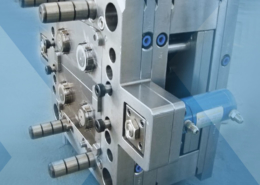
Unraveling the Mystery of the Best Plastic for Injection Molding
Author:gly Date: 2024-06-08
In the dynamic world of manufacturing, the choice of plastic material for injection molding plays a pivotal role in determining the quality, performance, and cost-effectiveness of the final product. With a plethora of options available, selecting the best plastic for injection molding can be a daunting task. This article aims to demystify this process by exploring the characteristics, applications, and considerations associated with the best plastic materials for injection molding.
Introduction: Understanding the Significance of Plastic Selection
The selection of the best plastic material for injection molding is a critical decision that influences every aspect of the manufacturing process, from design to production to end-use performance. With advancements in material science and engineering, manufacturers have access to a wide range of plastic resins, each offering unique properties and advantages. By understanding the characteristics and applications of different plastic materials, businesses can make informed decisions that optimize product quality, cost-efficiency, and market competitiveness.
Mechanical Properties: Balancing Strength and Flexibility
One of the primary considerations when selecting the best plastic for injection molding is the desired mechanical properties of the final product. Different plastics offer varying degrees of strength, stiffness, toughness, and flexibility, depending on their molecular structure and composition. For applications requiring high impact resistance, materials such as ABS (Acrylonitrile Butadiene Styrene) or polycarbonate are preferred. Conversely, for components requiring flexibility and resilience, materials like polypropylene or TPE (Thermoplastic Elastomer) may be more suitable. By carefully assessing the mechanical requirements of the intended application, manufacturers can choose the best plastic material that strikes the optimal balance between strength and flexibility.
Thermal Stability: Ensuring Performance in High-Temperature Environments
In applications where exposure to high temperatures is a concern, selecting a plastic material with excellent thermal stability is essential. Certain plastics, such as PEEK (Polyether Ether Ketone) or PPS (Polyphenylene Sulfide), offer exceptional heat resistance and can withstand prolonged exposure to elevated temperatures without compromising performance. These materials are commonly used in automotive, aerospace, and electrical applications where thermal stability is critical. By choosing a plastic material with the appropriate thermal properties, manufacturers can ensure the long-term reliability and durability of their products in demanding environments.
Chemical Resistance: Protecting Against Corrosive Environments
For applications where exposure to harsh chemicals or corrosive substances is a concern, selecting a plastic material with superior chemical resistance is paramount. Plastics such as PVC (Polyvinyl Chloride), HDPE (High-Density Polyethylene), or PTFE (Polytetrafluoroethylene) offer excellent resistance to a wide range of chemicals, solvents, and corrosive agents. These materials are commonly used in industries such as pharmaceuticals, chemicals, and agriculture, where resistance to chemical degradation is essential for product integrity and performance. By choosing a plastic material with the appropriate chemical resistance, manufacturers can ensure the longevity and reliability of their products in challenging environments.
Cost Considerations: Balancing Performance and Affordability
While performance and durability are crucial considerations when selecting the best plastic for injection molding, cost-effectiveness also plays a significant role. Certain high-performance plastics, such as PEEK or Ultem, may offer superior mechanical properties and thermal stability but come at a higher cost. On the other hand, commodity plastics like polyethylene or polypropylene offer affordability but may lack the desired performance characteristics for certain applications. By carefully evaluating the performance requirements and cost constraints of the project, manufacturers can choose the best plastic material that strikes the optimal balance between performance and affordability, maximizing value without compromising quality.
Sustainability: Embracing Eco-Friendly Solutions
In today's environmentally conscious world, sustainability has become a key consideration in material selection for injection molding. With increasing pressure to reduce plastic waste and minimize environmental impact, manufacturers are seeking eco-friendly alternatives that offer biodegradability, recyclability, and reduced carbon footprint. Bio-based plastics, recycled materials, and biodegradable polymers offer promising solutions for sustainable injection molding applications. By prioritizing sustainability in material selection, manufacturers can minimize their environmental footprint and contribute to a greener, more sustainable future.
Conclusion: Navigating the Complexities of Plastic Selection
In conclusion, selecting the best plastic material for injection molding is a multifaceted process that requires careful consideration of various factors, including mechanical properties, thermal stability, chemical resistance, cost-effectiveness, and sustainability. By understanding the unique properties and applications of different plastic resins, manufacturers can make informed decisions that optimize product performance, cost-efficiency, and environmental sustainability. As advancements in material science continue to drive innovation, the landscape of plastic selection for injection molding will continue to evolve, offering new possibilities for enhanced performance, durability, and eco-friendliness. By staying informed and adaptable, manufacturers can navigate the complexities of plastic selection and stay ahead in a competitive marketplace.
GETTING A QUOTE WITH LK-MOULD IS FREE AND SIMPLE.
FIND MORE OF OUR SERVICES:
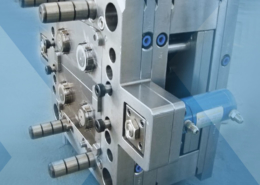
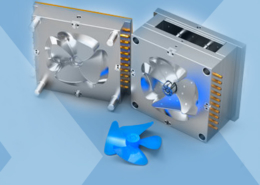
Plastic Molding

Rapid Prototyping
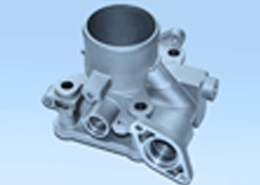
Pressure Die Casting
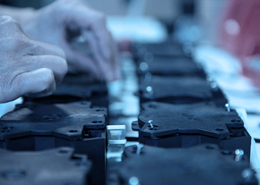
Parts Assembly
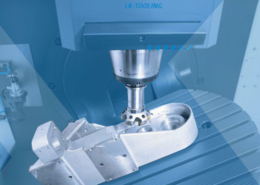