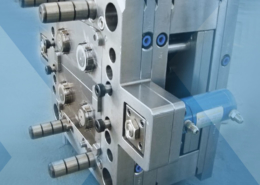
Exploring the World of Clean Room Injection Molding
Author:gly Date: 2024-06-08
Clean room injection molding represents a pinnacle of precision manufacturing, where meticulous attention to cleanliness and quality is paramount. This specialized process ensures the production of high-quality plastic components for industries where contamination control is critical, such as medical devices, pharmaceuticals, electronics, and aerospace. In this article, we delve into the realm of clean room injection molding, unraveling its intricacies, applications, advantages, and future prospects.
Introduction to Clean Room Injection Molding
Clean room injection molding is a manufacturing process that takes place within a controlled environment designed to minimize airborne particles, contaminants, and microbial contamination. This environment, known as a clean room, adheres to stringent cleanliness standards specified by regulatory bodies such as ISO and FDA. Clean room injection molding ensures the production of pristine plastic components with minimal risk of defects or contamination, making it ideal for applications where product integrity and safety are paramount.
Background and Evolution
The concept of clean room manufacturing originated in the semiconductor industry, where the production of microelectronic components necessitated ultra-clean environments to prevent defects and ensure product reliability. Over time, clean room technology has been adapted and applied to various industries, including injection molding, to meet the stringent cleanliness requirements of sensitive applications such as medical devices and pharmaceutical packaging.
Principles of Clean Room Injection Molding
Clean room injection molding follows the same basic principles as conventional injection molding, with the added emphasis on maintaining a clean and controlled environment throughout the manufacturing process. This includes strict adherence to cleanliness protocols, personnel hygiene practices, and environmental monitoring to ensure compliance with cleanliness standards and regulations.
Key Aspects of Clean Room Injection Molding
Facility Design and Layout
Clean room injection molding facilities are meticulously designed and constructed to minimize the ingress of contaminants and maintain a controlled environment. Key design considerations include the layout of clean rooms, airflow management, filtration systems, and material handling procedures to prevent contamination from external sources.
Material Handling and Preparation
The handling and preparation of raw materials in clean room injection molding are subject to strict protocols to prevent contamination. Raw materials are stored in sealed containers, and material handling equipment is designed to minimize contact with airborne particles. Additionally, material drying and purification processes may be employed to ensure the cleanliness of the resin before injection molding.
Process Control and Monitoring
Clean room injection molding processes are closely monitored and controlled to maintain cleanliness and quality standards. This includes real-time monitoring of environmental conditions, machine parameters, and part quality throughout the production cycle. Any deviations from predefined criteria are promptly identified and addressed to ensure product integrity.
Applications and Industries
Clean room injection molding finds applications in industries where contamination control is critical to product performance and safety.
Medical Devices
In the medical device industry, clean room injection molding is used to produce components such as syringes, catheters, and surgical instruments. These components require a high level of cleanliness to ensure patient safety and regulatory compliance.
Pharmaceutical Packaging
Clean room injection molding is employed in the production of pharmaceutical packaging components such as vials, ampules, and closures. These components must maintain sterility and integrity to preserve the efficacy and shelf life of pharmaceutical products.
Electronics
In the electronics industry, clean room injection molding is utilized to manufacture components for sensitive electronic devices such as connectors, housings, and encapsulations. The cleanliness of these components is crucial to prevent performance degradation and reliability issues.
Advantages and Challenges
Advantages
High Precision
: Clean room injection molding enables the production of precision components with tight tolerances and consistent quality.
Contamination Control
: The controlled environment of clean rooms minimizes the risk of contamination, ensuring product integrity and reliability.
Regulatory Compliance
: Clean room injection molding facilities adhere to regulatory standards and certifications, providing assurance of product safety and quality.
Challenges
Cost
: The construction and operation of clean room facilities entail significant capital investment and operating expenses.
Complexity
: Maintaining cleanliness and compliance with regulatory requirements adds complexity to the injection molding process, requiring specialized expertise and resources.
Process Limitations
: Clean room injection molding may have limitations in terms of material selection, part size, and production volume compared to conventional injection molding processes.
Future Directions and Opportunities
The future of clean room injection molding holds promise for innovation and advancement in several key areas.
Materials Development
Research and development efforts are focused on the development of advanced materials with enhanced properties such as biocompatibility, durability, and chemical resistance. These materials will expand the applications of clean room injection molding in diverse industries and enable the production of next-generation products.
Automation and Robotics
Advancements in automation and robotics technology will enhance the efficiency, productivity, and repeatability of clean room injection molding processes. Automated systems for material handling, mould changing, and quality inspection will reduce cycle times, minimize human intervention, and improve process control.
Conclusion
In conclusion, clean room injection molding represents a pinnacle of precision manufacturing, offering unparalleled cleanliness, quality, and reliability in the production of plastic components for sensitive applications. With its stringent cleanliness standards, advanced technology, and diverse applications, clean room injection molding continues to drive innovation and advancement across industries. By embracing technological advancements, materials innovation, and collaborative partnerships, the clean room injection molding industry is poised for continued growth and evolution in the years to come, shaping the future of manufacturing in the process.
GETTING A QUOTE WITH LK-MOULD IS FREE AND SIMPLE.
FIND MORE OF OUR SERVICES:
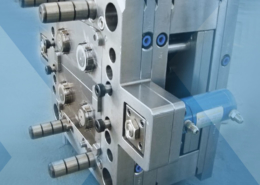
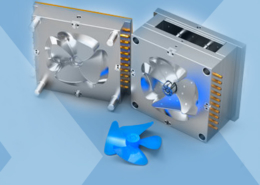
Plastic Molding

Rapid Prototyping
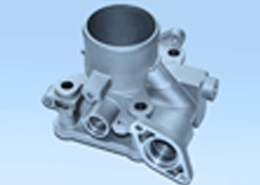
Pressure Die Casting
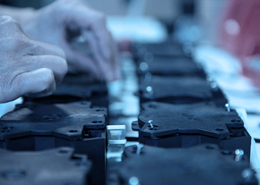
Parts Assembly
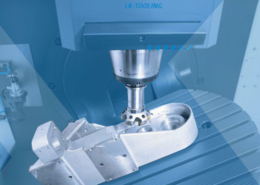