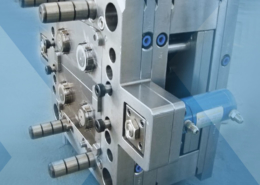
Exploring the Innovations in Acrylic Injection Molding
Author:gly Date: 2024-06-08
Introduction:
Acrylic injection molding stands at the forefront of modern manufacturing, revolutionizing the production of a wide array of products with its versatility and precision. From intricate medical devices to sleek consumer electronics, acrylic injection molding has become indispensable across industries. This article delves into the intricacies of acrylic injection molding, unveiling its techniques, applications, and innovations, thereby igniting curiosity and understanding among readers.
Technological Advancements
In recent years, technological advancements have propelled acrylic injection molding to new heights of precision and efficiency. The integration of computer-aided design (CAD) software with molding machines has streamlined the manufacturing process, allowing for intricate designs with minimal margin for error. Additionally, the advent of multi-material injection molding techniques has opened doors to unparalleled creativity, enabling the seamless fusion of acrylic with other materials, thereby enhancing functionality and aesthetics.
The introduction of advanced cooling systems has significantly reduced production cycles, maximizing output without compromising quality. Furthermore, the implementation of real-time monitoring and control systems ensures consistent product quality, minimizing defects and rework. These technological innovations underscore the pivotal role of acrylic injection molding in modern manufacturing, driving efficiency, and innovation.
Applications in Various Industries
The versatility of acrylic injection molding finds expression across diverse industries, catering to a spectrum of applications. In the automotive sector, acrylic components are renowned for their durability, clarity, and resistance to harsh environmental conditions. From headlamp lenses to interior trim components, acrylic injection molding facilitates the production of high-quality automotive parts that meet stringent industry standards.
In the healthcare industry, acrylic injection molding plays a pivotal role in the manufacturing of medical devices and equipment. The biocompatibility of acrylic makes it ideal for applications such as surgical instruments, diagnostic devices, and laboratory equipment. Moreover, the ability to achieve precise dimensions and complex geometries ensures the seamless integration of acrylic components into medical devices, enhancing their performance and usability.
Environmental Sustainability
Amid growing concerns about environmental sustainability, acrylic injection molding has emerged as a frontrunner in eco-friendly manufacturing practices. The recyclability of acrylic resin allows for the efficient utilization of resources, minimizing waste and reducing the environmental footprint of production processes. Furthermore, advancements in biodegradable acrylic formulations offer a sustainable alternative to traditional petroleum-based plastics, promoting a circular economy and mitigating environmental impact.
Future Perspectives and Conclusion
In conclusion, acrylic injection molding stands as a testament to the ingenuity and innovation driving modern manufacturing. From technological advancements to diverse applications and environmental sustainability, acrylic injection molding continues to redefine the boundaries of possibility. As we look to the future, continued research and development hold the promise of further enhancing the capabilities of acrylic injection molding, ushering in a new era of efficiency, sustainability, and creativity in manufacturing.
In summary, the exploration of acrylic injection molding not only elucidates its significance in contemporary manufacturing but also underscores its potential for future advancements. By embracing innovation and sustainability, acrylic injection molding paves the way for a brighter, more resilient future, where precision meets possibility.
GETTING A QUOTE WITH LK-MOULD IS FREE AND SIMPLE.
FIND MORE OF OUR SERVICES:
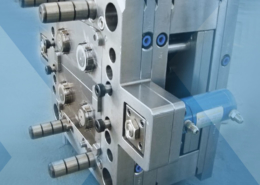
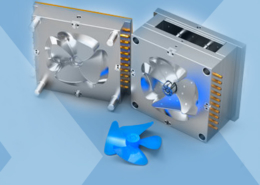
Plastic Molding

Rapid Prototyping
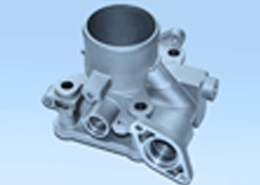
Pressure Die Casting
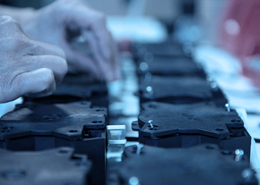
Parts Assembly
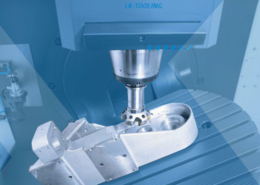