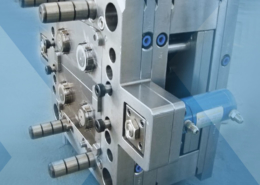
Exploring Advanced Plastic Moulding: Revolutionizing Manufacturing
Author:gly Date: 2024-06-08
Advanced plastic moulding stands at the forefront of modern manufacturing, offering innovative solutions for the production of high-quality plastic components. This article aims to delve into the intricacies of advanced plastic moulding, highlighting its techniques, applications, benefits, and future prospects, thus igniting the reader's interest and providing comprehensive background information.
Introduction to Advanced Plastic Moulding
Advanced plastic moulding represents a paradigm shift in manufacturing, leveraging cutting-edge technologies, materials, and processes to achieve unparalleled precision, efficiency, and versatility. From automotive and aerospace industries to consumer electronics and medical devices, advanced plastic moulding plays a pivotal role in shaping various sectors and driving technological innovation.
State-of-the-Art Moulding Techniques
Injection Moulding
Injection moulding stands as one of the most prevalent and versatile techniques in advanced plastic moulding. It involves injecting molten plastic into a mould cavity under high pressure, where it solidifies to form intricate and complex parts. With advancements in machine capabilities, process control, and material science, injection moulding offers unmatched precision, repeatability, and efficiency in producing plastic components of varying sizes and geometries.
Blow Moulding
Blow moulding is another essential technique in advanced plastic moulding, primarily used for manufacturing hollow plastic parts such as bottles, containers, and automotive fuel tanks. The process involves inflating a heated plastic preform or parison inside a mould cavity, resulting in a seamless and uniform container. Advanced blow moulding technologies, such as extrusion blow moulding and injection blow moulding, enable the production of lightweight, durable, and aesthetically pleasing plastic products with enhanced mechanical properties.
Compression Moulding
Compression moulding is well-suited for producing high-strength, fibre-reinforced plastic components used in industries such as aerospace, defence, and sports equipment. This technique involves placing a preheated composite material or thermoset plastic sheet in a heated mould cavity and applying pressure to compress and shape the material. With advancements in composite materials, mould design, and process optimization, compression moulding offers superior strength-to-weight ratios, fatigue resistance, and dimensional stability in engineered plastic parts.
Applications Across Industries
Automotive and Aerospace
In the automotive and aerospace industries, advanced plastic moulding is instrumental in producing lightweight, fuel-efficient, and aerodynamic components. From interior trim panels and exterior body panels to engine components and structural reinforcements, plastic moulding technologies enable manufacturers to achieve design flexibility, cost efficiency, and performance optimization in vehicles and aircraft.
Consumer Electronics and Appliances
Advanced plastic moulding plays a vital role in the consumer electronics and appliance sectors, where precision, aesthetics, and functionality are paramount. Plastic moulded parts such as casings, enclosures, and connectors are ubiquitous in smartphones, laptops, home appliances, and consumer gadgets. With advancements in micro-moulding, multi-shot moulding, and surface finishing techniques, manufacturers can produce compact, durable, and visually appealing plastic components that meet the demands of modern consumers.
Medical Devices and Healthcare
The medical industry relies on advanced plastic moulding for the production of critical components used in medical devices, diagnostic equipment, and healthcare products. From surgical instruments and implantable devices to drug delivery systems and diagnostic consumables, plastic moulded parts offer biocompatibility, sterilizability, and design versatility. With stringent regulatory requirements and evolving healthcare needs, advanced plastic moulding technologies enable manufacturers to innovate and deliver life-saving solutions to patients worldwide.
Advantages and Future Directions
Advanced plastic moulding offers numerous advantages, including design flexibility, cost efficiency, and rapid prototyping capabilities. Future directions may include the integration of digital technologies such as additive manufacturing, machine learning, and virtual prototyping to further enhance the efficiency, sustainability, and customization options in plastic moulding processes. Additionally, advancements in bio-based polymers, recycled materials, and circular economy initiatives hold promise for reducing environmental impact and promoting sustainable manufacturing practices in the plastics industry.
Conclusion
In conclusion, advanced plastic moulding represents a transformative force in manufacturing, empowering industries to innovate, optimize, and thrive in a competitive global market. By harnessing state-of-the-art technologies, materials, and processes, advanced plastic moulding enables manufacturers to meet the evolving needs of customers, address sustainability challenges, and drive progress towards a more efficient, resilient, and sustainable future.
GETTING A QUOTE WITH LK-MOULD IS FREE AND SIMPLE.
FIND MORE OF OUR SERVICES:
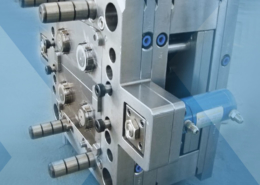
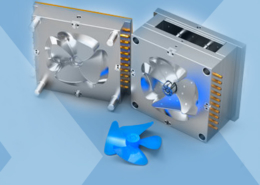
Plastic Molding

Rapid Prototyping
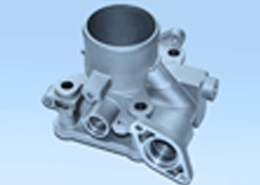
Pressure Die Casting
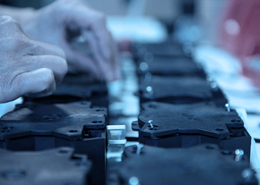
Parts Assembly
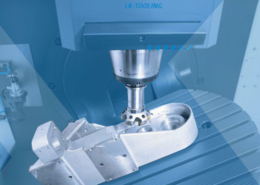