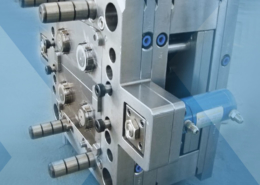
Unveiling the Versatility of ABS Molding
Author:gly Date: 2024-06-08
ABS molding, a prevalent technique in the realm of injection molding, plays a pivotal role in the production of a wide array of plastic components. In this article, we delve into the world of ABS molding, exploring its applications, properties, advantages, challenges, and future prospects.
Introduction
ABS (Acrylonitrile Butadiene Styrene) molding stands as a cornerstone of modern manufacturing, offering a versatile solution for producing plastic parts with a balance of strength, rigidity, and impact resistance. From automotive components to consumer electronics and household appliances, ABS molding finds applications across diverse industries, driving innovation and efficiency in product design and manufacturing processes. As we embark on a journey to unravel the intricacies of ABS molding, we uncover its significance in shaping the modern industrial landscape.
Properties of ABS Material
ABS material exhibits a unique combination of properties that make it well-suited for injection molding applications. Its high impact resistance, coupled with good tensile strength and dimensional stability, makes ABS an ideal choice for parts subjected to mechanical stress or varying environmental conditions. Moreover, ABS offers excellent surface finish and can be easily machined, painted, or coated to achieve desired aesthetics and functionality. These inherent properties of ABS material contribute to its widespread adoption in diverse industries, ranging from automotive and electronics to consumer goods and medical devices.
Injection Molding Process
The injection molding process for ABS material involves the heating of ABS pellets to a molten state, followed by the injection of the molten material into a mold cavity under high pressure. Once injected, the ABS material cools and solidifies within the mold, taking on the desired shape and features. The versatility of ABS molding allows for the production of complex parts with intricate geometries, sharp corners, and fine details. Additionally, ABS material can be blended with additives or reinforcements to further enhance its properties, such as flame retardancy, UV resistance, or improved mechanical strength.
Applications of ABS Molding
ABS molding finds applications in a wide range of industries, thanks to its versatility, durability, and cost-effectiveness. In the automotive sector, ABS is used to produce interior and exterior components such as dashboards, trim panels, grilles, and bumpers. In the electronics industry, ABS is employed to manufacture housings, enclosures, and structural components for devices ranging from smartphones and laptops to home appliances and industrial equipment. Moreover, ABS molding is prevalent in the production of consumer goods such as toys, furniture, sporting equipment, and medical devices, showcasing its adaptability to diverse manufacturing requirements.
Advantages and Challenges
ABS molding offers several advantages, including excellent impact resistance, dimensional stability, and ease of processing. Its ability to be molded into complex shapes with precise details and tight tolerances further enhances its appeal for manufacturers. However, ABS molding also presents challenges such as warping, shrinkage, and surface defects, particularly in large or thin-walled parts. Mitigating these challenges requires careful consideration of mold design, processing parameters, and material selection, as well as the use of advanced simulation tools and process optimization techniques.
Future Prospects and Innovations
Looking ahead, the future of ABS molding is ripe with opportunities for innovation and advancement. Emerging trends such as additive manufacturing, digitalization, and sustainable materials hold promise for expanding the capabilities and applications of ABS molding. Moreover, ongoing research and development efforts aimed at improving material formulations, processing technologies, and recyclability will further drive the adoption of ABS molding in various industries. By embracing innovation and embracing sustainability, ABS molding can continue to play a vital role in shaping the future of manufacturing, delivering solutions that meet the evolving needs of customers and society.
Conclusion
In conclusion, ABS molding stands as a versatile and indispensable technique in modern manufacturing, offering a robust solution for producing plastic parts with superior properties and performance. Through its unique combination of properties, including impact resistance, dimensional stability, and ease of processing, ABS material enables the creation of innovative products across diverse industries. By understanding the principles, applications, advantages, and challenges of ABS molding, manufacturers can harness its full potential to drive innovation, efficiency, and sustainability in the dynamic world of injection molding.
Through continuous research, collaboration, and technological advancement, ABS molding can pave the way for new possibilities and applications, contributing to the advancement of industries and the improvement of products. As we navigate the future of manufacturing, ABS molding remains a steadfast ally, providing solutions that empower manufacturers to create, innovate, and thrive in a rapidly evolving global landscape.
GETTING A QUOTE WITH LK-MOULD IS FREE AND SIMPLE.
FIND MORE OF OUR SERVICES:
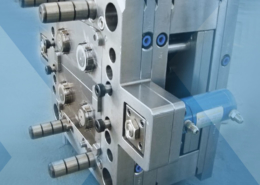
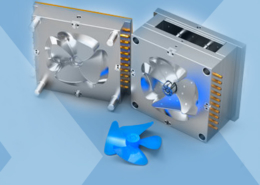
Plastic Molding

Rapid Prototyping
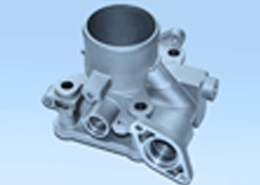
Pressure Die Casting
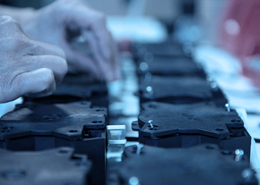
Parts Assembly
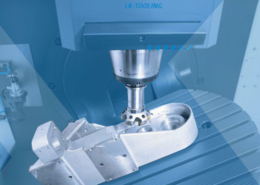