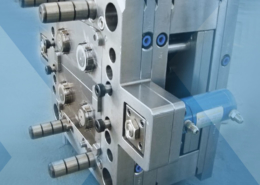
Exploring Two Shot Moulding: Revolutionizing Plastic Manufacturing
Author:gly Date: 2024-06-08
Introduction
In the realm of plastic manufacturing, innovation is paramount to efficiency, cost-effectiveness, and product quality. Two shot moulding stands as a testament to such innovation, revolutionizing traditional plastic injection moulding processes. This technique, also known as dual-shot, twin-shot, or multi-shot injection moulding, has garnered immense attention in recent years due to its ability to create complex, multi-material components with unparalleled precision and efficiency. In this article, we delve into the intricacies of two shot moulding, exploring its processes, applications, advantages, challenges, and future prospects.
Processes and Methodology
Two shot moulding involves injecting two different materials into a single moulding cycle, enabling the production of intricate parts with varying colors, textures, or properties. The process typically begins with the injection of the first material into the mould cavity, followed by the rotation or movement of the mould to accommodate the second material. This sequential injection ensures precise positioning and bonding between the materials, resulting in seamless integration and enhanced product functionality.
The methodology behind two shot moulding revolves around precision engineering and advanced mould design. Manufacturers employ specialized equipment, such as rotary or shuttle moulding machines, to facilitate the sequential injection process. Moreover, meticulous attention is paid to material selection, compatibility, and processing parameters to achieve optimal results. The integration of automation and robotics further streamlines production and enhances repeatability, ensuring consistent part quality and dimensional accuracy.
Applications and Industries
The versatility of two shot moulding transcends various industries, ranging from automotive and electronics to healthcare and consumer goods. In automotive manufacturing, this technique is employed to produce interior components, such as dashboard panels, buttons, and trim with integrated functionalities and aesthetic appeal. Similarly, in the electronics sector, two shot moulding is utilized to create housings for devices, incorporating soft-touch grips, buttons, and seals for enhanced usability and durability.
In the healthcare industry, two shot moulding finds applications in the production of medical devices and equipment, such as syringe plungers, drug delivery systems, and surgical instruments. The ability to combine different materials with varying hardness, biocompatibility, and sterilization properties enables the creation of complex yet functional components vital for patient care and safety. Additionally, in the consumer goods sector, this technique facilitates the manufacturing of ergonomic handles, grips, and closures with customizable colors and textures, enhancing product differentiation and brand recognition.
Advantages and Benefits
Two shot moulding offers a myriad of advantages over traditional moulding processes, making it a preferred choice for complex component manufacturing. Firstly, it eliminates the need for secondary assembly operations, reducing production time, labor costs, and material waste. By consolidating multiple components into a single moulding cycle, it enhances part integrity, dimensional accuracy, and overall product quality. Moreover, the seamless integration of different materials enables the creation of innovative designs, functional features, and aesthetic finishes, enhancing product performance and market competitiveness.
Furthermore, two shot moulding facilitates design freedom and flexibility, allowing for the incorporation of intricate geometries, undercuts, and overmoulding without compromising structural integrity. This flexibility extends to material selection, enabling engineers to combine rigid and flexible polymers, thermoplastics, elastomers, and additives to meet specific application requirements. Additionally, the scalability and repeatability of two shot moulding make it ideal for high-volume production, catering to the demands of mass manufacturing while maintaining consistency and cost-effectiveness.
Challenges and Considerations
Despite its numerous benefits, two shot moulding presents certain challenges and considerations that need to be addressed for successful implementation. One such challenge is material compatibility and adhesion, as improper bonding between the materials can lead to delamination, voids, or part failure. To mitigate this risk, thorough material testing and compatibility studies are essential, ensuring proper surface preparation, adhesion promoters, and mould surface treatments are employed.
Moreover, the complexity of two shot moulding processes requires a deep understanding of mould design, tooling, and process parameters to achieve desired results. Issues such as warpage, sink marks, and knit lines may arise due to material shrinkage, cooling rates, and moulding conditions, necessitating iterative adjustments and optimization. Additionally, the initial investment in tooling and equipment for two shot moulding may be higher compared to traditional moulding methods, requiring careful cost-benefit analysis and long-term planning.
Conclusion
In conclusion, two shot moulding stands at the forefront of plastic manufacturing, offering unparalleled capabilities in creating complex, multi-material components with precision and efficiency. From automotive and electronics to healthcare and consumer goods, its applications span across diverse industries, driving innovation and product differentiation. While it presents challenges in material compatibility, process complexity, and initial investment, the benefits of reduced assembly, enhanced design freedom, and improved product quality outweigh the obstacles. As technology advances and market demands evolve, two shot moulding is poised to play a pivotal role in shaping the future of plastic manufacturing, unlocking new possibilities and opportunities for innovation.
Through continuous research, development, and collaboration, the potential of two shot moulding can be further explored and expanded, paving the way for advancements in material science, moulding technologies, and sustainable practices. By harnessing the power of two shot moulding, manufacturers can overcome traditional limitations, unleash creativity, and deliver superior products that meet the ever-changing needs and expectations of consumers in a rapidly evolving global marketplace.
GETTING A QUOTE WITH LK-MOULD IS FREE AND SIMPLE.
FIND MORE OF OUR SERVICES:
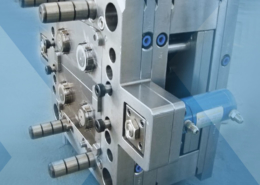
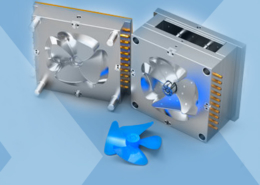
Plastic Molding

Rapid Prototyping
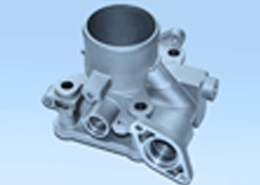
Pressure Die Casting
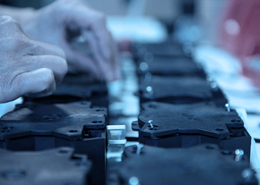
Parts Assembly
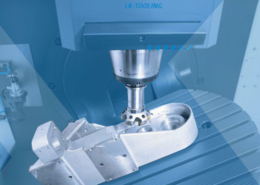