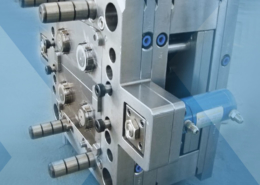
Understanding Ultem Injection Molding: Revolutionizing Manufacturing
Author:gly Date: 2024-06-08
Ultem injection molding stands at the forefront of modern manufacturing techniques, revolutionizing the production of high-performance thermoplastic components. With its exceptional properties and versatility, Ultem has become a preferred choice for industries ranging from aerospace to medical devices. This article aims to delve into the intricacies of Ultem injection molding, shedding light on its process, advantages, applications, and future prospects.
Introduction to Ultem Injection Molding
Ultem injection molding involves the fabrication of intricate parts using Ultem resin, a thermoplastic material known for its outstanding mechanical properties, high heat resistance, and excellent chemical resistance. Developed by SABIC, Ultem offers a unique combination of strength, stiffness, and dimensional stability, making it ideal for demanding applications in diverse industries.
Process Overview
The process of Ultem injection molding begins with the melting of Ultem resin pellets in an injection molding machine. The molten material is then injected into a mold cavity under high pressure, where it cools and solidifies to form the desired part. This process allows for the production of complex shapes with tight tolerances, ensuring consistent quality and performance.
Injection Molding Machine
Injection molding machines used for Ultem molding are equipped with high-temperature capabilities to accommodate the elevated processing temperatures required for Ultem resin. Precise control of temperature, pressure, and cooling is essential to achieve optimal results and minimize defects.
Mold Design and Tooling
The design of the mold plays a critical role in Ultem injection molding. Factors such as gate location, cooling channels, and part geometry must be carefully considered to ensure proper filling, uniform cooling, and efficient ejection. Advanced tooling technologies, such as conformal cooling, can further enhance productivity and part quality.
Processing Parameters
Optimizing processing parameters is essential to achieve the desired properties in Ultem molded parts. Variables such as melt temperature, injection speed, packing pressure, and cycle time must be carefully controlled to prevent issues such as warping, sink marks, or voids.
Advantages of Ultem Injection Molding
Ultem injection molding offers numerous advantages over traditional manufacturing methods and alternative materials.
High Temperature Resistance
Ultem resin exhibits exceptional heat resistance, with continuous-use temperatures exceeding 350°F (177°C). This makes it suitable for applications where exposure to elevated temperatures is common, such as automotive components and electronic devices.
Chemical Resistance
Ultem is highly resistant to a wide range of chemicals, including acids, bases, and solvents. This property makes it ideal for applications in harsh environments where exposure to corrosive substances is a concern, such as chemical processing equipment and medical devices.
Strength and Stiffness
Ultem offers excellent mechanical properties, including high tensile strength, modulus of elasticity, and impact resistance. This makes it well-suited for structural components that require strength and rigidity, such as aircraft interiors and industrial machinery.
Applications
Ultem injection molding finds applications across various industries, where its unique combination of properties enables the production of high-performance components.
Aerospace
In the aerospace industry, Ultem is used to manufacture lightweight, yet durable components for aircraft interiors, including seat components, cabin panels, and overhead bins. Its flame-retardant properties and compliance with industry regulations make it an ideal choice for these critical applications.
Medical Devices
Ultem is widely used in the medical device industry for the production of surgical instruments, diagnostic equipment, and disposable components. Its biocompatibility, sterilizability, and resistance to body fluids make it suitable for use in demanding healthcare environments.
Electronics
In the electronics industry, Ultem is utilized for the fabrication of components such as connectors, sockets, and housings for electronic devices. Its high dielectric strength, dimensional stability, and flame-retardant properties make it an excellent choice for applications requiring electrical insulation and reliability.
Future Directions
As technology continues to advance, the future of Ultem injection molding holds promise for further innovation and growth. Continued research into material formulations, process optimization, and advanced manufacturing techniques will likely expand the range of applications and enhance the performance of Ultem-molded components. Additionally, efforts to improve sustainability and reduce environmental impact through recycling and eco-friendly production methods will shape the future landscape of Ultem injection molding.
Conclusion
In conclusion, Ultem injection molding represents a significant advancement in the field of manufacturing, offering unparalleled performance, versatility, and reliability. From aerospace to medical devices, Ultem has established itself as a go-to material for demanding applications, thanks to its exceptional properties and processing capabilities. As industries continue to push the boundaries of innovation, Ultem injection molding will undoubtedly play a pivotal role in shaping the future of manufacturing.
This article has provided an in-depth exploration of Ultem injection molding, from its fundamental principles to its practical applications and future prospects. By understanding the intricacies of Ultem molding, manufacturers can unlock new opportunities for product development, cost savings, and performance improvement. As technology evolves and market demands shift, embracing Ultem injection molding will be essential for staying competitive in an ever-changing landscape of manufacturing.
GETTING A QUOTE WITH LK-MOULD IS FREE AND SIMPLE.
FIND MORE OF OUR SERVICES:
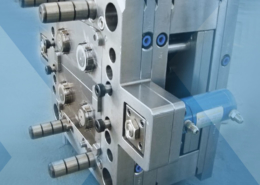
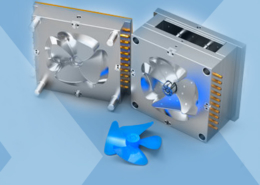
Plastic Molding

Rapid Prototyping
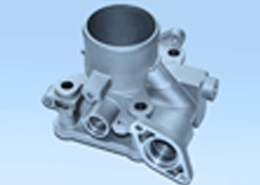
Pressure Die Casting
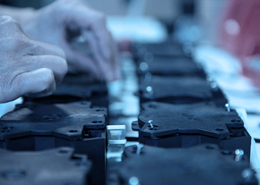
Parts Assembly
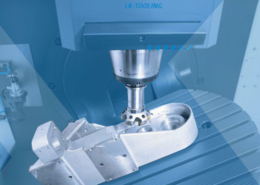