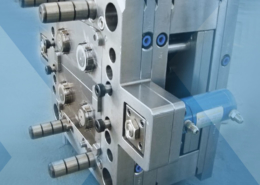
Exploring Two Shot Injection Molding: Revolutionizing Manufacturing
Author:gly Date: 2024-06-08
Introduction
In the realm of manufacturing, innovation continually reshapes the landscape, driving efficiency, precision, and versatility. Two shot injection molding emerges as a pivotal advancement, revolutionizing the way complex parts are produced. This technique, also known as dual-shot, twin-shot, or 2K molding, offers a paradigm shift by enabling the creation of multi-material or multi-color components in a single process. Its impact spans across industries, from automotive and electronics to healthcare and consumer goods. Understanding the intricacies of two shot injection molding unveils a world of possibilities, where design constraints dissolve, and engineering boundaries expand.
Understanding Two Shot Injection Molding
Two shot injection molding encompasses a sophisticated process that integrates two different materials or colors into a single mold. Unlike traditional injection molding, which involves one material at a time, this technique injects the primary material initially, followed by a secondary material injection in the same mold. The result is a seamless integration of distinct materials or colors, yielding complex geometries and enhanced functionalities.
Process and Equipment
The process of two shot injection molding begins with the design of a specialized mold, often featuring multiple cavities and complex channels to facilitate material flow. High-precision injection molding machines equipped with dual barrels and specialized nozzles execute the sequential injections. The coordination between machine, mold, and materials is paramount, demanding meticulous control of temperature, pressure, and timing.
Applications Across Industries
The versatility of two shot injection molding transcends industry boundaries, finding application in diverse sectors. In automotive manufacturing, it enables the production of intricately designed interior components with soft-touch finishes and vibrant color accents. In electronics, the technique facilitates the encapsulation of delicate circuits with resilient, protective housings. Furthermore, in medical device manufacturing, it allows for the integration of biocompatible materials, enhancing patient safety and comfort.
Advantages and Challenges
Two shot injection molding offers a plethora of advantages, including reduced production costs, minimized assembly processes, and improved product durability. By consolidating multiple components into a single part, manufacturers streamline assembly lines, decrease material waste, and enhance product aesthetics. However, challenges such as material compatibility, tooling complexity, and process optimization persist, requiring careful consideration and expertise.
Future Perspectives and Innovations
As technology evolves and material sciences advance, the future of two shot injection molding appears promising. Continued research and development efforts aim to overcome existing limitations and expand the capabilities of this technique. Innovations in materials, including biodegradable polymers and conductive compounds, hold the potential to unlock new applications and redefine manufacturing standards. Moreover, advancements in digital design tools and simulation software empower engineers to explore complex geometries and optimize part performance with unprecedented precision.
Conclusion
In conclusion, two shot injection molding stands as a testament to human ingenuity and engineering prowess. Its ability to seamlessly integrate multiple materials or colors within a single part redefines the possibilities of modern manufacturing. From enhancing product aesthetics to improving functionality and durability, this technique transcends traditional constraints, paving the way for a new era of innovation. As industries continue to embrace the potential of two shot injection molding, collaboration between researchers, engineers, and manufacturers will drive progress, shaping the future of production methodologies.
GETTING A QUOTE WITH LK-MOULD IS FREE AND SIMPLE.
FIND MORE OF OUR SERVICES:
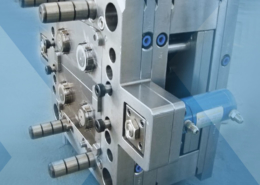
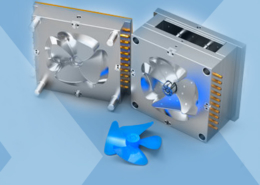
Plastic Molding

Rapid Prototyping
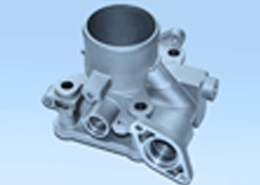
Pressure Die Casting
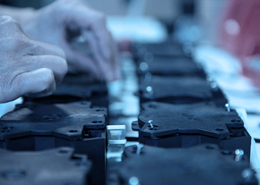
Parts Assembly
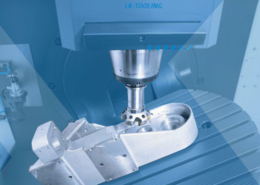