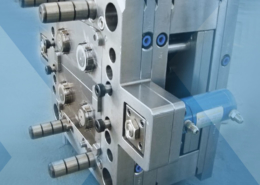
Exploring the Dynamics of Thin Wall Moulding
Author:gly Date: 2024-06-08
Thin wall moulding represents a sophisticated technique within the realm of injection moulding, characterized by the production of intricately designed, lightweight plastic components with minimal wall thickness. This article aims to unravel the intricacies of thin wall moulding, providing readers with insights into its principles, applications, challenges, and future prospects.
Introduction to Thin Wall Moulding
Thin wall moulding refers to the process of manufacturing plastic parts with significantly reduced wall thickness compared to conventional injection moulding. This technique involves precise control of injection parameters, mould design, and material selection to achieve thin-walled parts without compromising structural integrity or quality. Thin wall moulding finds widespread applications in industries such as packaging, electronics, automotive, and medical, where lightweight, high-performance components are in demand.
Evolution and Significance
The evolution of thin wall moulding technology has been driven by the need for lightweight, cost-effective solutions in various industries. As consumer preferences shift towards sleek, compact designs, manufacturers are compelled to explore innovative techniques to produce thinner, lighter components without sacrificing functionality or durability. Thin wall moulding enables the creation of complex geometries, intricate details, and precise features, opening up new possibilities for product design and performance optimization.
Key Considerations in Thin Wall Moulding
Achieving success in thin wall moulding requires careful consideration of various factors, ranging from material selection to process optimization and tooling design.
Material Selection and Properties
The choice of material plays a crucial role in thin wall moulding, influencing part performance, manufacturability, and cost-effectiveness. High-flow thermoplastics such as polypropylene (PP), polycarbonate (PC), and acrylonitrile butadiene styrene (ABS) are commonly used for thin wall applications due to their excellent flow properties, impact resistance, and dimensional stability. Understanding the rheological behavior, melt flow index, and mechanical properties of the selected material is essential for optimizing the injection process and ensuring part quality.
Process Optimization and Control
Optimizing the injection moulding process parameters is paramount for achieving consistent, high-quality results in thin wall moulding. Factors such as injection speed, pressure, temperature, cooling time, and packing pressure must be meticulously controlled to prevent defects such as warpage, sink marks, and short shots. Advanced simulation software and real-time monitoring systems facilitate process optimization, allowing manufacturers to identify potential issues and fine-tune parameters for optimal performance.
Challenges and Solutions
Despite its numerous advantages, thin wall moulding poses challenges related to part design, tooling complexity, and material behavior. Addressing these challenges requires innovative solutions and continuous improvement efforts.
Part Design and Geometry
Designing thin-walled parts requires careful consideration of geometry, wall thickness, draft angles, and ribbing to ensure adequate strength, stiffness, and dimensional stability. Utilizing advanced CAD software and design optimization techniques enables engineers to create efficient, lightweight components while minimizing material usage and production costs.
Tooling Design and Manufacture
The design and manufacture of moulds for thin wall moulding present unique challenges due to the intricacy and precision required. High-speed machining, EDM (electrical discharge machining), and CNC (computer numerical control) technologies are employed to produce complex mould cavities with tight tolerances and fine surface finishes. Additionally, innovative cooling strategies, such as conformal cooling channels, help to minimize cycle times and improve part quality.
Future Perspectives and Conclusion
In conclusion, thin wall moulding represents a paradigm shift in injection moulding technology, offering unparalleled opportunities for lightweight, high-performance component production. By leveraging advanced materials, process optimization techniques, and innovative tooling solutions, manufacturers can unlock the full potential of thin wall moulding to meet the evolving demands of modern industries.
Looking ahead, the future of thin wall moulding lies in continuous innovation, research, and collaboration across the supply chain. Emerging technologies such as additive manufacturing, multi-material moulding, and Industry 4.0 integration are poised to further revolutionize the field, enabling the production of even thinner, lighter, and more complex parts with enhanced efficiency and sustainability. Embracing these advancements will position thin wall moulding as a cornerstone of modern manufacturing, driving progress and innovation in diverse industries.
GETTING A QUOTE WITH LK-MOULD IS FREE AND SIMPLE.
FIND MORE OF OUR SERVICES:
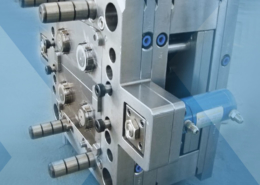
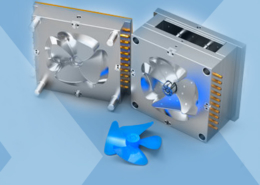
Plastic Molding

Rapid Prototyping
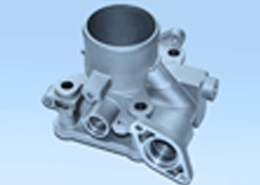
Pressure Die Casting
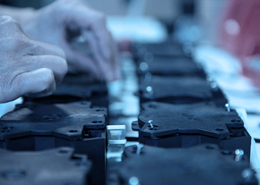
Parts Assembly
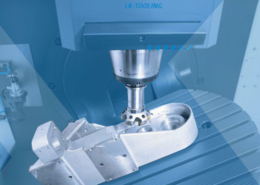