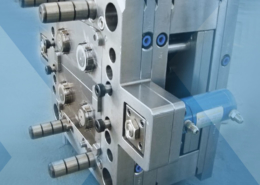
Exploring the Efficiency and Versatility of Thermolator Injection Molding
Author:gly Date: 2024-06-08
Introduction
In the realm of modern manufacturing, the innovation of Thermolator injection molding stands as a pinnacle of efficiency and versatility. As technology advances, so does the need for precise and rapid manufacturing processes, and Thermolator injection molding rises to meet these demands with its cutting-edge capabilities. This article aims to delve into the intricacies of Thermolator injection molding, elucidating its fundamental principles, applications, advantages, and future prospects.
Fundamental Principles
Thermal Regulation Mechanism:
Thermolator injection molding operates on the principle of precise thermal regulation. The system consists of a series of heaters and coolers strategically positioned within the mold cavity, ensuring uniform temperature distribution throughout the molding process. This meticulous control of temperature is paramount in achieving impeccable product quality and minimizing defects.
Injection Process Dynamics:
Central to Thermolator injection molding is the injection process dynamics. Molten material, typically plastic resin, is injected into the mold cavity under high pressure. The material fills the cavity, taking the shape of the mold, and subsequently cools and solidifies. This process is characterized by its speed, accuracy, and repeatability, making it ideal for mass production of intricate components.
Applications
Automotive Industry:
One of the primary applications of Thermolator injection molding lies within the automotive industry. From dashboard components to intricate engine parts, Thermolator injection molding enables the production of high-precision components with unparalleled efficiency. The ability to customize molds swiftly facilitates rapid prototyping and iterative design processes, allowing automotive manufacturers to stay ahead in a competitive market.
Consumer Electronics:
In the realm of consumer electronics, Thermolator injection molding plays a pivotal role in the production of casings, buttons, and internal components. The demand for sleek, lightweight, and durable electronic devices necessitates advanced manufacturing techniques, and Thermolator injection molding rises to the occasion. Its ability to mold intricate geometries with micron-level precision ensures seamless integration of components in modern gadgets.
Medical Devices:
In the medical sector, where precision and reliability are paramount, Thermolator injection molding finds extensive utility. From syringe components to surgical instruments, the medical device industry relies on Thermolator injection molding for the production of sterile, high-quality components. The biocompatibility of materials used in the process ensures compliance with stringent regulatory standards, making Thermolator injection molding indispensable in the healthcare landscape.
Advantages
Enhanced Efficiency:
One of the most significant advantages of Thermolator injection molding is its enhanced efficiency. By streamlining the manufacturing process and minimizing material wastage, Thermolator injection molding significantly reduces production costs and lead times. The ability to produce intricate components with minimal human intervention further augments operational efficiency, making it a preferred choice for industries seeking to optimize their manufacturing processes.
Versatility in Material Selection:
Another notable advantage of Thermolator injection molding is its versatility in material selection. From commodity plastics to engineering-grade polymers, Thermolator injection molding accommodates a wide range of materials, each tailored to specific application requirements. This versatility enables manufacturers to explore novel materials, opening doors to innovation and product differentiation in competitive markets.
Environmental Sustainability:
In an era marked by growing environmental consciousness, Thermolator injection molding offers a sustainable manufacturing solution. By minimizing material wastage and energy consumption, Thermolator injection molding reduces the carbon footprint associated with traditional manufacturing processes. Furthermore, the recyclability of thermoplastic materials used in the process contributes to a circular economy, aligning with global sustainability goals.
Conclusion
In conclusion, Thermolator injection molding stands as a testament to human ingenuity in the realm of manufacturing. Its unparalleled efficiency, versatility, and sustainability make it a cornerstone of modern industrial processes. As technology continues to advance, Thermolator injection molding will undoubtedly evolve, opening new avenues for innovation and shaping the future of manufacturing. Embracing this transformative technology is not only essential for staying competitive but also for ushering in a new era of precision engineering and sustainable development.
GETTING A QUOTE WITH LK-MOULD IS FREE AND SIMPLE.
FIND MORE OF OUR SERVICES:
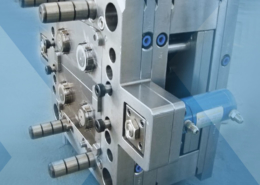
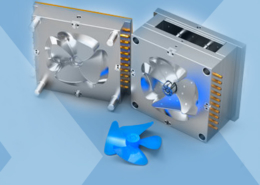
Plastic Molding

Rapid Prototyping
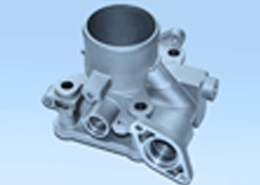
Pressure Die Casting
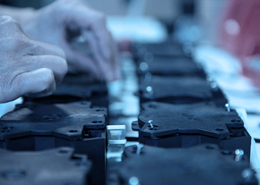
Parts Assembly
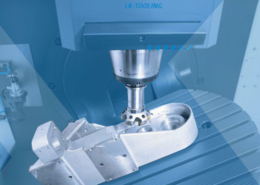