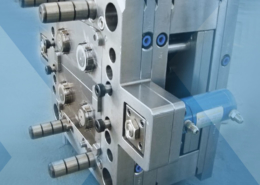
Thermoplastic Injection: Revolutionizing Manufacturing
Author:gly Date: 2024-06-08
Thermoplastic injection molding stands at the forefront of modern manufacturing processes, revolutionizing industries with its versatility, efficiency, and precision. Originating in the late 19th century, this technique has undergone remarkable advancements, making it indispensable across various sectors today. This article delves into the intricacies of thermoplastic injection molding, exploring its principles, applications, advancements, and future prospects.
Principles of Thermoplastic Injection
Thermoplastic injection involves melting plastic pellets and injecting the molten material into a mold cavity under high pressure. Upon cooling and solidification, the mold opens, releasing the final product. The process hinges on precision control of temperature, pressure, and cooling rate to achieve desired outcomes. Its fundamental principle lies in the ability to repeatedly mold complex shapes with high accuracy and consistency.
Applications Across Industries
Thermoplastic injection finds applications across a myriad of industries, ranging from automotive and aerospace to consumer goods and healthcare. In automotive manufacturing, it facilitates the production of intricate components, enhancing vehicle performance and safety. Similarly, in healthcare, it enables the fabrication of medical devices with stringent quality standards, ensuring reliability and sterility.
Advancements in Material Science
Recent advancements in material science have expanded the capabilities of thermoplastic injection molding. Innovations such as biodegradable polymers and conductive plastics have opened new avenues in sustainability and electronics. Moreover, the development of nanocomposites and reinforced polymers has led to materials with enhanced strength, durability, and thermal stability, broadening the scope of applications.
Automation and Industry 4.0 Integration
The integration of automation and Industry 4.0 technologies has transformed the landscape of thermoplastic injection molding. Robotics and artificial intelligence optimize production processes, minimizing cycle times and reducing waste. Furthermore, the implementation of real-time monitoring systems enables predictive maintenance and quality control, ensuring consistency and reliability in output.
Environmental Considerations
Despite its numerous benefits, thermoplastic injection molding poses environmental challenges, primarily concerning plastic waste and energy consumption. Efforts towards sustainability include the adoption of recyclable materials, energy-efficient machinery, and closed-loop systems for material recovery. Additionally, research focuses on bio-based polymers and novel recycling methods to mitigate environmental impact.
Conclusion
In conclusion, thermoplastic injection molding stands as a cornerstone of modern manufacturing, driving innovation and progress across industries. Its principles of precision and repeatability, coupled with advancements in material science and technology, have propelled it to the forefront of production processes. However, addressing environmental concerns remains imperative for its sustainable future. By embracing sustainability initiatives and continued research, the potential of thermoplastic injection molding can be maximized, ushering in a new era of manufacturing excellence.
GETTING A QUOTE WITH LK-MOULD IS FREE AND SIMPLE.
FIND MORE OF OUR SERVICES:
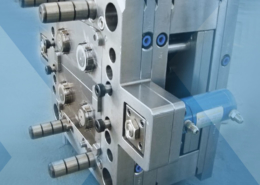
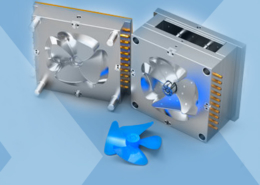
Plastic Molding

Rapid Prototyping
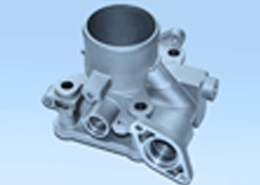
Pressure Die Casting
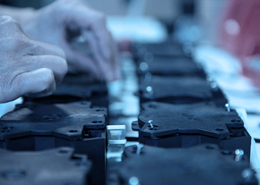
Parts Assembly
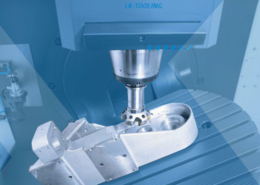