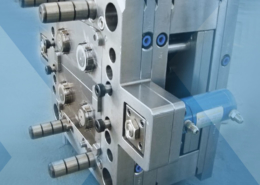
Exploring the World of the Strongest Injection Molded Plastics
Author:gly Date: 2024-06-08
Injection molding has revolutionized the manufacturing industry, offering unparalleled precision and efficiency in the production of plastic components. Among the myriad of plastics available for injection molding, some stand out for their exceptional strength and durability. In this comprehensive exploration, we delve into the realm of the strongest injection molded plastics, uncovering their properties, applications, and potential for innovation.
Understanding Strength in Injection Molded Plastics
Strength in injection molded plastics is a multifaceted property influenced by factors such as material composition, processing parameters, and part design. The strongest injection molded plastics exhibit high tensile strength, impact resistance, and dimensional stability, making them ideal for demanding applications across various industries.
Material Composition
The choice of material is paramount in determining the strength of injection molded plastics. Engineering-grade thermoplastics such as PEEK (Polyetheretherketone), PAI (Polyamide-imide), and PEI (Polyetherimide) are renowned for their exceptional mechanical properties, including high tensile strength and heat resistance. These materials offer a unique combination of strength and versatility, making them suitable for a wide range of applications in aerospace, automotive, and medical industries.
Processing Parameters
The strength of injection molded plastics is also influenced by processing parameters such as melt temperature, injection speed, and mold temperature. Optimal processing conditions are essential to ensure uniform melt distribution, minimize voids and defects, and enhance the mechanical properties of the final part. Advanced molding techniques such as gas-assisted injection molding and sequential valve gating can further improve part quality and strength.
Applications in Demanding Environments
The strongest injection molded plastics find widespread use in applications where exceptional strength and durability are required to withstand harsh operating conditions.
Aerospace Industry
In the aerospace industry, where safety and reliability are paramount, injection molded plastics play a critical role in the production of lightweight, high-strength components for aircraft and spacecraft. Materials such as PEEK and PEI are valued for their exceptional strength-to-weight ratio, chemical resistance, and thermal stability, making them ideal for structural components, interior panels, and engine parts.
Automotive Industry
In the automotive industry, injection molded plastics are used extensively in the production of structural components, interior trim, and under-the-hood parts. The strongest injection molded plastics provide excellent impact resistance, fatigue strength, and dimensional stability, ensuring long-term performance and reliability in demanding automotive applications.
Pushing the Boundaries of Strength and Innovation
As technology advances and new materials are developed, the potential for innovation in the field of injection molded plastics continues to expand.
Nanocomposites
Nanocomposites, composed of a polymer matrix reinforced with nanoparticles, offer the promise of unprecedented strength, stiffness, and thermal stability. By incorporating nanoscale reinforcements such as carbon nanotubes or graphene into the polymer matrix, researchers are able to enhance the mechanical properties of injection molded plastics, opening up new possibilities for lightweight, high-performance materials.
Additive Manufacturing
Additive manufacturing techniques such as 3D printing are revolutionizing the production of injection molds, allowing for the rapid prototyping and fabrication of complex geometries with minimal material waste. By leveraging the flexibility of additive manufacturing, designers can optimize part designs for strength and performance, pushing the boundaries of what is possible in injection molded plastics.
Conclusion
In conclusion, the world of the strongest injection molded plastics is characterized by innovation, precision, and versatility. With their exceptional strength, durability, and performance, these materials are driving advancements across a wide range of industries, from aerospace and automotive to healthcare and consumer electronics. As we look to the future, continued research and development efforts hold the promise of unlocking new materials and manufacturing techniques, further expanding the capabilities of injection molded plastics and pushing the boundaries of what is possible in engineering and design.
GETTING A QUOTE WITH LK-MOULD IS FREE AND SIMPLE.
FIND MORE OF OUR SERVICES:
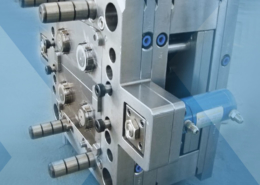
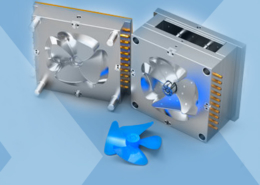
Plastic Molding

Rapid Prototyping
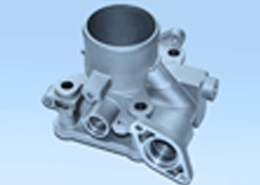
Pressure Die Casting
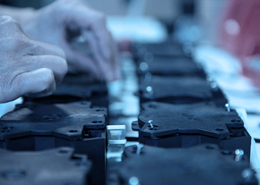
Parts Assembly
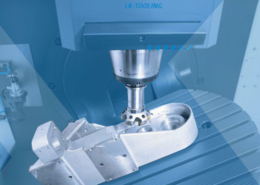