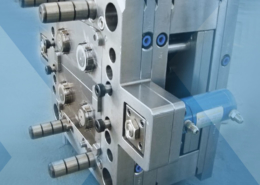
Unraveling the Potential of Soft Tooling Injection Molding
Author:gly Date: 2024-06-08
Soft tooling injection molding stands as a revolutionary approach in the realm of manufacturing, offering flexibility, cost-effectiveness, and rapid turnaround times. This article aims to captivate readers' interest by introducing the concept of soft tooling injection molding, providing background information, and delving into various aspects of this innovative technique.
Introduction to Soft Tooling Injection Molding
Soft tooling injection molding, also known as rapid tooling or prototype tooling, refers to the use of temporary or semi-permanent molds made from materials such as silicone, polyurethane, or aluminum for the production of plastic parts. Unlike traditional steel molds, soft tooling allows for quick iterations, low setup costs, and reduced lead times, making it an attractive option for prototyping, low-volume production, and product development.
Advantages of Soft Tooling Injection Molding
Soft tooling injection molding offers several advantages over conventional molding methods.
Cost-Effectiveness
One of the primary benefits of soft tooling is its cost-effectiveness, especially for small production runs or prototypes. The lower material and machining costs associated with soft tooling make it an economical choice for testing designs, validating concepts, and launching new products without significant upfront investment.
Quick Turnaround
Soft tooling enables rapid turnaround times, allowing manufacturers to iterate designs and produce functional prototypes in a matter of days rather than weeks or months. This accelerated timeline accelerates the product development process, reduces time-to-market, and enhances competitiveness in fast-paced industries.
Flexibility
Soft tooling offers greater flexibility in design modifications and part revisions compared to traditional steel molds. Changes can be implemented quickly and cost-effectively, allowing for on-the-fly adjustments based on feedback, testing results, or design iterations without the need for extensive tooling modifications.
Process Overview
The process of soft tooling injection molding involves several key steps, from mold design to part production.
Mold Design
Soft tooling molds are typically designed using computer-aided design (CAD) software, taking into account part geometry, material properties, and production requirements. Mold designs can range from simple single-cavity molds to complex multi-cavity molds, depending on the desired part complexity and production volume.
Mold Fabrication
Once the mold design is finalized, the soft tooling is fabricated using additive manufacturing techniques such as 3D printing or subtractive manufacturing methods such as CNC machining. The choice of fabrication method depends on factors such as material properties, surface finish requirements, and production volume.
Injection Molding
Once the soft tooling is fabricated, it is mounted onto an injection molding machine, and the molding process begins. Molten thermoplastic resin is injected into the mold cavity under high pressure, where it cools and solidifies to form the desired part. The molded parts are then ejected from the mold, trimmed, and finished as needed.
Applications
Soft tooling injection molding finds applications across various industries, offering versatility and cost-effectiveness for a wide range of projects.
Prototyping
Soft tooling is widely used for prototyping purposes, allowing designers and engineers to quickly iterate designs, test concepts, and validate product performance before investing in expensive production tooling. By producing functional prototypes early in the design process, manufacturers can identify and address potential issues, reduce development costs, and accelerate time-to-market.
Low-Volume Production
Soft tooling is also well-suited for low-v
GETTING A QUOTE WITH LK-MOULD IS FREE AND SIMPLE.
FIND MORE OF OUR SERVICES:
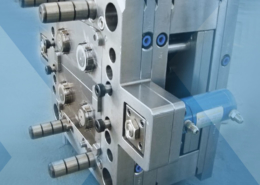
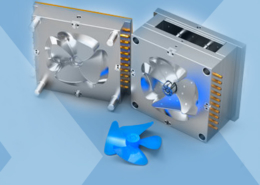
Plastic Molding

Rapid Prototyping
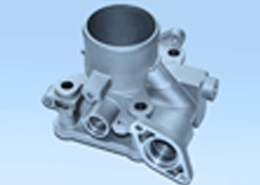
Pressure Die Casting
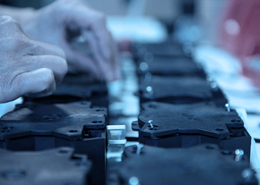
Parts Assembly
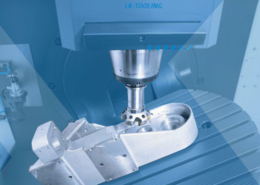