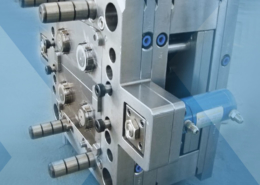
Exploring the Realm of Soft Plastic Injection Molds
Author:gly Date: 2024-06-08
Soft plastic injection molds represent a cornerstone of modern manufacturing, enabling the production of a wide range of flexible plastic parts used in various industries. From medical devices to consumer electronics, soft plastic injection molding offers unparalleled versatility and efficiency. In this article, we delve into the intricacies of soft plastic injection molds, exploring their applications, advantages, and impact on the manufacturing landscape.
Unveiling the Process
Understanding Soft Plastic Injection Molding
Soft plastic injection molding is a manufacturing process that involves injecting molten thermoplastic elastomers into a mold cavity under high pressure. Unlike traditional injection molding, which typically uses rigid plastics, soft plastic injection molding produces parts with flexible properties, making it ideal for applications requiring elasticity and durability.
Advanced Molding Techniques
Several advanced techniques are employed in soft plastic injection molding to achieve precise results. These include multi-cavity molds, which allow for the simultaneous production of multiple parts, and overmolding, where a soft elastomer is injected over a rigid substrate to create parts with different material properties in different areas.
Optimizing Design for Soft Plastic Molding
Design plays a crucial role in the success of soft plastic injection molding projects. Engineers must consider factors such as material selection, part geometry, and mold design to ensure optimal results. By leveraging computer-aided design (CAD) software and simulation tools, designers can refine their designs and anticipate potential issues before production begins.
Applications Across Industries
Medical Devices and Healthcare
Soft plastic injection molding is widely used in the medical device industry to produce components such as seals, gaskets, and flexible tubing. These parts are essential for medical devices such as catheters, syringes, and respiratory masks, where biocompatibility, flexibility, and durability are critical.
Consumer Electronics and Wearables
In the consumer electronics sector, soft plastic injection molding is employed to produce components with ergonomic designs and enhanced functionality. From smartphone cases with shock-absorbing properties to fitness trackers with flexible bands, soft plastic parts add value and differentiation to a wide range of electronic devices and wearables.
Automotive Interiors and Seating
Soft plastic injection molding is also utilized in the automotive industry to produce components for interiors and seating systems. From dashboard panels and door trims to armrests and headrests, soft plastic parts enhance comfort and aesthetics while meeting stringent safety and performance requirements.
Advantages and Considerations
Enhanced Flexibility and Comfort
One of the primary advantages of soft plastic injection molding is the enhanced flexibility and comfort it provides. By using soft elastomers with tailored durometer levels, manufacturers can create parts that conform to complex shapes and provide cushioning and support in applications where comfort is paramount.
Cost-Effective Production
Despite the initial investment in tooling and equipment, soft plastic injection molding can be a cost-effective manufacturing solution in the long run. By reducing the need for secondary operations such as bonding and assembly and minimizing material waste, soft plastic molding can streamline production processes and lower overall costs.
Maintenance of Tight Tolerances
However, it's essential to maintain tight tolerances and control processing parameters to ensure the quality and consistency of soft plastic molded parts. Factors such as material shrinkage, mold temperature, and injection pressure can affect part dimensions and mechanical properties and must be carefully monitored and optimized throughout the production process.
Conclusion
In conclusion, soft plastic injection molding is a versatile and impactful manufacturing process with applications across a wide range of industries. By combining advanced molding techniques with optimized designs, manufacturers can produce innovative products with enhanced functionality, comfort, and aesthetics. As technology continues to advance, the potential for soft plastic injection molding to drive innovation and efficiency in manufacturing is boundless, making it a technique worthy of further exploration and investment.
GETTING A QUOTE WITH LK-MOULD IS FREE AND SIMPLE.
FIND MORE OF OUR SERVICES:
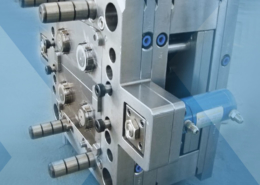
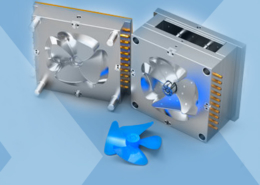
Plastic Molding

Rapid Prototyping
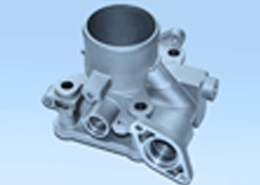
Pressure Die Casting
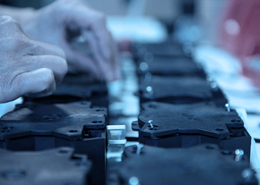
Parts Assembly
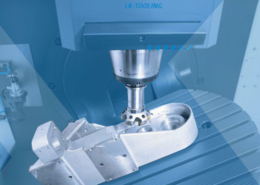