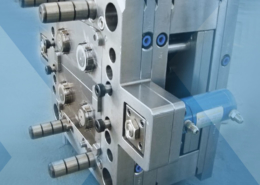
Exploring Prototype Injection Molding: Revolutionizing Product Development
Author:gly Date: 2024-06-08
Introduction
Prototype injection molding stands as a cornerstone in the realm of product development, offering a rapid and cost-effective means of producing prototypes for evaluation, testing, and refinement. This article delves into the realm of prototype injection molding, exploring its significance, techniques, applications, advancements, and challenges. By understanding the intricacies of prototype injection molding, engineers and innovators can accelerate the product development cycle, minimize time-to-market, and optimize design iterations with precision and efficiency.
Significance of Prototype Injection Molding
Accelerating Time-to-Market
Prototype injection molding enables designers and engineers to swiftly transform conceptual designs into physical prototypes, expediting the product development process. By facilitating rapid iteration and validation of designs, prototype molding shortens development cycles and enhances competitiveness in dynamic market landscapes.
Facilitating Design Optimization
The iterative nature of prototype injection molding empowers designers to iteratively refine and optimize product designs based on real-world testing and feedback. This iterative approach minimizes design flaws, enhances functionality, and maximizes manufacturability, leading to superior end products with enhanced performance and reliability.
Minimizing Development Costs
Compared to traditional manufacturing methods, prototype injection molding offers a cost-effective solution for producing small batches of prototypes. By minimizing tooling costs, material wastage, and labor expenses associated with conventional prototyping techniques, prototype molding enables cost-efficient exploration of design alternatives and feasibility studies.
Techniques in Prototype Injection Molding
Rapid Tooling
Rapid tooling techniques, such as aluminum or soft steel molds, expedite the manufacturing process by reducing lead times and costs associated with traditional tooling methods. These rapid tooling solutions are well-suited for low-volume production runs and iterative prototyping cycles.
3D Printing Integration
Integration of 3D printing technologies with prototype injection molding further enhances flexibility and agility in product development. By leveraging 3D printed molds or inserts, designers can rapidly iterate on designs, validate concepts, and produce functional prototypes with intricate geometries and complex features.
Material Selection Versatility
Prototype injection molding offers a wide range of thermoplastic materials, each with unique properties and characteristics suited to specific application requirements. From standard resins to advanced engineering polymers, material selection versatility enables engineers to tailor prototypes to meet performance, aesthetic, and functional criteria.
Challenges and Future Directions
Complexity and Tolerance Control
As product designs become increasingly complex and demanding, maintaining tight tolerances and ensuring part quality poses challenges in prototype injection molding. Advancements in mold design, process optimization, and quality control methodologies are essential to address these challenges and enhance the accuracy and consistency of molded prototypes.
Scalability and Production Integration
While prototype injection molding excels in low-volume production and prototyping stages, integrating prototyped designs into full-scale production environments requires careful consideration of scalability, tooling amortization, and manufacturing efficiency. Future research may focus on bridging the gap between prototype and production processes to streamline transitions and optimize manufacturing workflows.
Sustainability and Material Innovation
Addressing environmental concerns and advancing sustainable practices in prototype injection molding is imperative for minimizing environmental impact and meeting regulatory requirements. Research efforts may concentrate on developing bio-based materials, recycling technologies, and eco-friendly manufacturing processes to promote sustainability and circularity in product development cycles.
Conclusion
In conclusion, prototype injection molding serves as a catalyst for innovation, agility, and efficiency in product development. By offering rapid iteration, design flexibility, and cost-effective prototyping solutions, prototype molding empowers designers and engineers to transform concepts into reality with speed and precision. As technology advances and industry demands evolve, continued research and innovation in prototype injection molding will drive progress, unlock new possibilities, and shape the future of product development. Embracing challenges, leveraging emerging technologies, and prioritizing sustainability will ensure that prototype injection molding remains a cornerstone in the quest for innovation and excellence in the dynamic landscape of product design and manufacturing.
GETTING A QUOTE WITH LK-MOULD IS FREE AND SIMPLE.
FIND MORE OF OUR SERVICES:
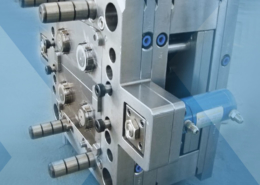
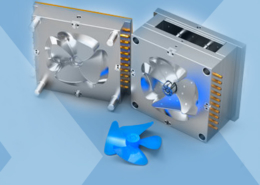
Plastic Molding

Rapid Prototyping
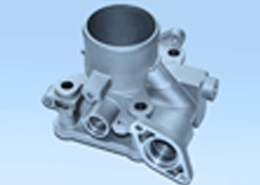
Pressure Die Casting
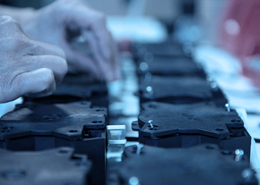
Parts Assembly
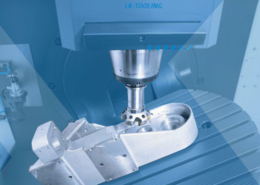