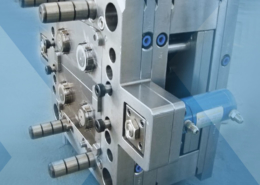
Exploring Prototype Plastic Molding: Revolutionizing Manufacturing
Author:gly Date: 2024-06-08
Prototype plastic molding stands at the forefront of modern manufacturing, embodying innovation and efficiency in the production process. This method, characterized by its versatility and precision, has garnered significant attention across industries for its ability to swiftly transform concepts into tangible prototypes. With its roots deeply embedded in engineering and design, prototype plastic molding has reshaped the landscape of product development, offering a cost-effective solution for businesses to iterate and refine their ideas before mass production.
The Evolution of Plastic Molding
Plastic molding techniques have evolved significantly since their inception, tracing back to the mid-19th century with the advent of injection molding. Initially, these methods primarily served industrial applications, but with technological advancements, particularly in computer-aided design (CAD) and computer-aided manufacturing (CAM), the scope of plastic molding expanded exponentially. Today, prototype plastic molding stands as a pinnacle of this evolution, enabling rapid prototyping with unparalleled precision and efficiency.
Technological Innovations
Technological innovations have been instrumental in propelling prototype plastic molding to new heights. The integration of 3D printing technology, for instance, has revolutionized the prototyping process by offering greater design freedom and reducing lead times. Additionally, advancements in materials science have broadened the range of polymers available for molding, allowing for the creation of prototypes with varying properties, from rigid to flexible, to simulate the characteristics of the final product accurately.
Applications Across Industries
The versatility of prototype plastic molding transcends industry boundaries, finding applications in automotive, aerospace, healthcare, consumer electronics, and beyond. In the automotive sector, for instance, manufacturers leverage prototype plastic molding to develop functional prototypes of components such as dashboards, bumpers, and interior trim, facilitating design validation and performance testing. Similarly, in the healthcare industry, medical device companies utilize this technology to prototype intricate devices and equipment, expediting the development process while ensuring regulatory compliance and patient safety.
Cost-Efficiency and Time Savings
One of the most compelling advantages of prototype plastic molding lies in its cost-efficiency and time savings. Traditional prototyping methods often entail substantial investment in tooling and machining, coupled with lengthy lead times. In contrast, prototype plastic molding offers a rapid and cost-effective alternative, allowing for quick iterations and modifications without the need for expensive tooling. This agility is particularly valuable in today's fast-paced market environment, where speed to market can determine the success or failure of a product.
Precision Engineering
Precision engineering is a hallmark of prototype plastic molding, underpinning its ability to produce highly detailed and accurate prototypes. Through advanced manufacturing techniques such as computer numerical control (CNC) machining and multi-cavity molds, manufacturers can achieve intricate geometries and tight tolerances with minimal margin for error. This level of precision not only enhances the aesthetic appeal of prototypes but also ensures functional integrity and performance consistency, laying the foundation for successful product launches.
Sustainability Considerations
Amid growing concerns about environmental sustainability, prototype plastic molding offers a compelling proposition by minimizing material wastage and energy consumption. By employing additive manufacturing processes and optimizing part designs for material efficiency, manufacturers can reduce the ecological footprint of prototyping activities while maximizing resource utilization. Furthermore, the recyclability of many thermoplastic materials used in prototype plastic molding contributes to a circular economy model, where waste is minimized, and resources are conserved.
Challenges and Future Outlook
Despite its numerous benefits, prototype plastic molding faces certain challenges, including material selection, surface finish consistency, and scalability for mass production. Addressing these challenges requires continued research and development efforts aimed at refining existing processes and exploring novel techniques. Looking ahead, the integration of artificial intelligence and machine learning algorithms holds promise for optimizing mold design, predicting material behavior, and streamlining production workflows, thereby further enhancing the efficacy and efficiency of prototype plastic molding.
Conclusion
In conclusion, prototype plastic molding represents a transformative force in modern manufacturing, offering unparalleled flexibility, precision, and cost-efficiency in the prototyping process. From automotive to healthcare, its applications span across diverse industries, driving innovation and accelerating product development cycles. While challenges persist, ongoing technological advancements and a commitment to sustainability position prototype plastic molding as a cornerstone of 21st-century manufacturing, poised to shape the future of product innovation and design.
GETTING A QUOTE WITH LK-MOULD IS FREE AND SIMPLE.
FIND MORE OF OUR SERVICES:
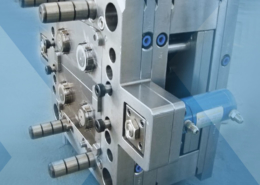
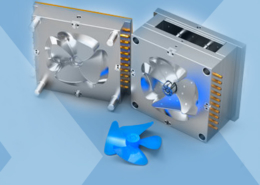
Plastic Molding

Rapid Prototyping
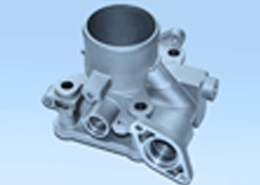
Pressure Die Casting
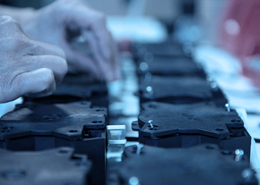
Parts Assembly
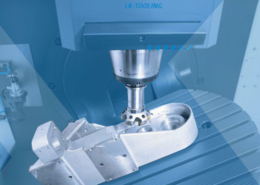