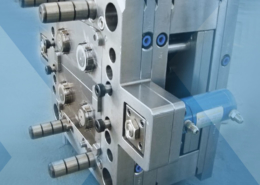
Exploring Prototype and Plastic Mold: Revolutionizing Manufacturing
Author:gly Date: 2024-06-08
In the ever-evolving landscape of manufacturing, the interplay between prototypes and plastic molds stands as a testament to innovation and efficiency. The marriage of these two elements has significantly transformed the way products are developed and produced across various industries. This article delves into the intricate realm of prototype development and plastic mold fabrication, unraveling their significance, processes, applications, and future prospects.
Prototype Development
The Evolution of Prototyping
Prototype development has undergone a remarkable evolution, transitioning from rudimentary models crafted by hand to sophisticated digital designs realized through advanced technologies such as 3D printing and computer-aided design (CAD). This evolution has not only accelerated the product development cycle but has also enhanced the precision and quality of prototypes, enabling manufacturers to iterate and refine their designs with unprecedented ease.
Prototyping Techniques and Technologies
A myriad of prototyping techniques and technologies have emerged, each offering unique advantages and applications. From rapid prototyping using additive manufacturing processes like stereolithography (SLA) and selective laser sintering (SLS) to subtractive methods such as CNC machining, manufacturers have a diverse array of tools at their disposal to materialize their design concepts into tangible prototypes. These techniques empower designers to test functionality, evaluate ergonomics, and gather user feedback early in the development phase, thereby mitigating risks and optimizing product performance.
The Role of Prototypes in Product Development
Prototypes serve as invaluable tools throughout the product development lifecycle, facilitating collaboration between designers, engineers, and stakeholders. By providing a physical representation of abstract concepts, prototypes bridge the gap between imagination and reality, enabling stakeholders to visualize, evaluate, and iterate on design iterations iteratively. Moreover, prototypes serve as effective communication tools, allowing designers to convey their ideas more persuasively and stakeholders to provide actionable feedback based on tangible evidence.
Plastic Mold Fabrication
Precision Engineering with Plastic Molds
Plastic mold fabrication lies at the heart of modern manufacturing, enabling mass production of intricate plastic components with unparalleled precision and repeatability. The process involves the creation of a precise negative cavity, into which molten plastic is injected and cooled to form the desired shape. With advancements in mold design, materials, and manufacturing techniques, plastic molds can accommodate complex geometries, intricate details, and tight tolerances, making them indispensable in industries ranging from automotive and electronics to healthcare and consumer goods.
The Art and Science of Mold Design
Designing an effective plastic mold requires a combination of artistry and engineering prowess. Mold designers meticulously craft the mold cavity, runner system, and cooling channels to optimize part quality, minimize cycle times, and maximize production efficiency. Utilizing computer-aided design (CAD) software and simulation tools, designers can analyze flow dynamics, predict potential defects, and optimize the mold design iteratively. By fine-tuning parameters such as gate location, venting, and cooling strategies, designers can achieve superior part quality and consistency, thereby reducing scrap rates and enhancing overall productivity.
Sustainable Practices in Mold Manufacturing
In an era of heightened environmental awareness, sustainable practices in mold manufacturing have gained prominence. Manufacturers are increasingly adopting eco-friendly materials, optimizing production processes, and implementing recycling initiatives to minimize waste and reduce environmental impact. Furthermore, advancements in biodegradable and recyclable plastics are reshaping the landscape of plastic mold fabrication, offering greener alternatives without compromising performance or quality. By embracing sustainability, manufacturers can align with consumer preferences, meet regulatory requirements, and contribute to a more sustainable future.
Conclusion
In conclusion, the synergy between prototype development and plastic mold fabrication heralds a new era of innovation and efficiency in manufacturing. From ideation to production, prototypes serve as tangible manifestations of creativity and ingenuity, while plastic molds enable cost-effective mass production of high-quality components. By harnessing the power of advanced technologies, embracing sustainable practices, and fostering collaboration across disciplines, manufacturers can unlock new opportunities for growth and differentiation in an increasingly competitive market landscape. As we embark on this transformative journey, let us continue to push the boundaries of possibility, pioneer new solutions, and shape a future where imagination knows no limits.
GETTING A QUOTE WITH LK-MOULD IS FREE AND SIMPLE.
FIND MORE OF OUR SERVICES:
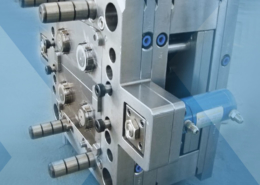
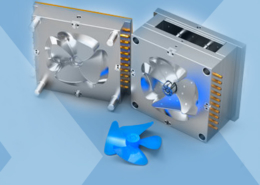
Plastic Molding

Rapid Prototyping
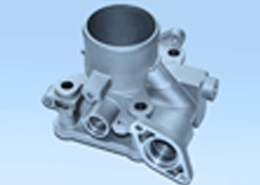
Pressure Die Casting
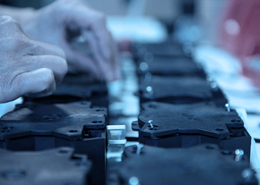
Parts Assembly
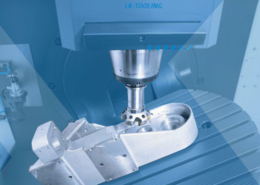