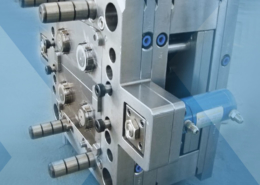
How Much Does A Plastic Injection Mold Cost? - plastic injection price
Author:gly Date: 2024-10-15
It's most often used for the manufacturing plastic parts at scale due to its low material waste and low cost per part. It’s an ideal manufacturing process for industries like medical devices, consumer products, and automotive.
It also offers a wide range of chemicals, colors, medicinal components, and agricultural goods. In 2019, BASF employed approximately 117,000 people in over 200 countries, including over 50,000 in Germany and 34,000 in the plastics and resins business.
The polymers you employ have an impact on the final functionality of your goods. Your product may not function correctly if you use the incorrect polymer. A flexible resin is unsuitable for applications requiring stiffness and strength. Non-medical grade or non-food grade resins, on the other hand, can provide significant health dangers and risks when employed in medical or food activities.
Lanxess is a German specialty chemicals business headquartered in Cologne. The firm was formed in 2004 as a spin-off of Bayer AG’s chemicals department and portions of its polymers sector. Plastics, rubbers, intermediates, and specialty chemicals are the primary products developed, manufactured, and marketed by the company.
No one ever said that designing and manufacturing molded parts was easy. Our goal is to get you through it quickly and with quality parts. A good starting point is our Design for Moldability Toolkit.
Critical-to-quality (CTQ) dimensions you call out on models let us know what areas are most crucial to the success of your parts. Once the parts start molding, the process and samples are qualified using automated inline CMM technology, generating a detailed FAI and process capability study with no additional lead time.
Ineos Group Limited is a global chemical corporation based in Rolle, Switzerland. INspec Ethylene OxideSpecialties is an abbreviation for INspec Ethylene OxideSpecialties. Plastics, resins, and intermediates are manufactured for all key markets, notably packaging, medicines, herbicides and pesticides, textiles, consumer products, construction and real estate, and automotive and transportation.
Recognizing the performance standards that the parts must satisfy is critical. These specifications will guide the component designer, plastic injection molding manufacturer, and resin supplier in selecting the optimum polymer for the application. Finally, it is advantageous to collaborate closely with a supplier from the start to choose the appropriate resin for your next product.
LG Chemical, based in Seoul, South Korea, is the biggest Korean chemical business. It produces chemical products, polyolefins, polyvinyl chloride, polystyrene, artificial rubbers, and specialty polymers. The firm is also a significant manufacturer of IT and electrical materials, as well as batteries. In 2019, the firm generated around $25.5 billion in annual revenues and employed approximately 15,000 employees worldwide.
Our digital factories create prototypes and low-volume parts fast, while our manufacturing network, offers advanced capabilities and volume pricing.
The firm operates in 24 countries, has 171 locations, and employs approximately 19,000 people. In 2018, the firm made around $60 billion in revenue.
With the current aforementioned information, there is no doubt that your struggles with getting a plastic pellet supplier for your project are now over. We hope that the information provided the much-needed confidence in starting the next plastic manufacturing project if you want to be a molding manufacturer. Go through the article again and find the best supplier that best suits your specific needs before making a choice. Happy shopping!
Want to learn more about injection molding? Sign up to receive a Design Cube. This physical aid demonstrates how to properly design features commonly found on molded parts.
Depending on your application's requirements, you can choose from the following when requesting an injection molding quote.
The company also is in major nations and digs for oil and gas on 6 continents. The firm is a global leader in the production of polyolefins, as well as other plastics and resins. In 2016, the firm generated about $290 billion in yearly revenues and employed approximately 75,600 employees globally.
It has been very enlightening to us here at HP that we are able to get parts so rapidly out of the actual materials that we're going to use in the final production.
SABIC (Saudi Arabia Basic Industries Corporation) is a commercial petrochemical corporation located in Riyadh, Saudi Arabia, that was formed in 1976. It has a wide range of applications, including chemicals and compounds, industrial plastics, fertilizer, and metal alloys.
Our helpful design aid demonstrates part features that are too thin or too thick, bad bosses, right and wrong ribs, and other considerations to be mindful of while designing parts for injection molding.
SABIC is the third-largest manufacturer of polyethylene on the planet, as well as the fourth-largest manufacturer of polypropylene and polyolefins in broad. The firm has its operations running in over 40 countries, with 60 working production facilities, and staffs over 40,000 people. As per Forbes, SABIC made around $35 billion in sales in 2017.
While the molds themselves are similar, part quantities, lifetime maintenance, quality documentation, and pricing vary depending on which service option is chosen. The right one depends on your project needs.
Lanxess is also a significant provider of synthetic materials through its partnership with Saudi Aramco. In 2015, the firm had sales of EUR 7.9 billion, and it employs about 16,700 people across 54 industrial locations in 29 countries.
Choosing the proper resin is important in almost every aspect of the plastic injection molding process. There are hundreds of injection molded thermoplastics to select from, each with a unique set of characteristics. Because of its renowned characteristics: strength, durability, and toughness, plastics are being employed in more usages than ever before. Also, there are a variety of manufacturers that one can select from while you apply for assistance with designing plastic products. Do read on to find out more.
We have wide selection of more than 100 thermoplastic and thermoset materials. And if you're looking for alternative material options, check out our guide to resin substitutes for ABS, PC, PP, and other commonly molded plastics.
Proto Labs, Inc. 5540 Pioneer Creek Dr. Maple Plain, MN 55359 United States P: 877-479-3680 F: 763-479-2679 E: [email protected]
Injection molding is a manufacturing process that consists of filling a metal mold cavity with liquid plastic resin, which then cools and forms a plastic part.
BASF is a Global enterprise chemical corporation located in Ludwigshafen, Germany, that was founded in 1865. The firm is a major provider of plastics and resins, with one of the most diverse plastics portfolios.
Tough Black (Loctite Henkel 3843) and Ceramic-Filled (BASF 3280) are two new advanced photopolymer materials now available for 3D printing.
Chevron Phillips Chemical is a petrochemical business based in the Texas town of Woodlands. Chevron Corporation and Phillips Corporation equally own the firm, which was created in 2000 by combining both corporations’ chemical activities. It is a significant manufacturer of petrochemicals, polyolefins, and specialty chemicals. Chevron Phillips employs about 5,000 people across 31 manufacturing and research locations in the United States, Singapore, South Korea, Saudi Arabia, Qatar, and Belgium. In 2018, the firm made around $160 billion in revenue.
Thermoplastics are classified into three types based on their family and type: commodity plastics, engineering plastics, and highly specialized or high-performance resins.
Our basic guidelines for plastic injection molding include important design considerations to help improve part moldability, enhance cosmetic appearance, and reduce overall production time. View our design guidelines page for more details.
It might be difficult to understand all of the elements that go into determining the cost per component when making a purchase with your manufacturer. The basic answer to establishing the price is the business’s demands and specs, but calculating the cost per component of injection molding depends on numerous factors, ranging from the type of material used to the quantity of manpower necessary.
Our plastic injection molding process produces custom prototypes and end-use production parts with lead times as fast as 1 day. We use aluminum molds that offer cost-efficient tooling and accelerated manufacturing cycles, and stock about 200 different thermoplastic resins.
Lyondell Basell is one of the world’s major plastics, chemical products, and refining businesses, based in the Netherlands. Basell Polyolefins acquired Lyondell Chemical Firm in December 2007 for $12.7 billion, resulting in the formation of the company.
Dow is an American global chemical business that operates in over 35 countries and offers chemicals, polymers, and agricultural goods. It has over 6,000 product categories that are manufactured all around the world. Dow is the world’s largest manufacturer of chlorine and polyalkylene glycols, as well as the globally leading provider of every major polyethylene (PE) resin (2016). In 2008, it was recognized as the world’s largest plastics maker. In 2015, the firm generated about $49 billion in yearly revenues and employed roughly 49,500 employees globally.
This complete reference guide walks you through everything from quoting, design analysis, and shipment to best practices that ensure your model is optimized for molding.
The manufacturing process for molded parts is complex. Before your parts are even molded, we're there to help you with comprehensive manufacturability feedback and consultative design services, so you can avoid mold design pitfalls before the resin hits the mold. From there, our production process is documented and optimized using scientific molding so you get high-quality parts consistently and reliably with every production run.
Eni S.p.A. (Ente Nazionale Idrocarburi) is a global Italian oil and gas corporation based in Rome. It is a significant producer of polymers and rubbers and is involved in the research, production, and processing of gas and oil. The firm employs approximately 31,000 individuals and works in 73 countries around the world. As per Forbes, ENI’s sales in 2019 were more than $89 billion.
Exxon Mobil Corporation is a global oil, gas, and chemical corporation based in Texas. It is a direct descendent of John D. Rockefeller’s Standard Oil Company and was created through the merging of Exxon and Mobil in 1999. ExxonMobil manufactures plastics, petrochemical products, fuel, and gasoline, along with other things.
LyondellBasell is the world’s leading manufacturer of polypropylene polymers and polypropylene substances, as well as one of the global highest polyethylene producers. It is also a significant manufacturer of high-value specialty polymers and resins. In 2019, the firm had around $34.7 billion1 in yearly revenues and employs roughly 19,400 employees globally.
Our thermoplastic injection molding is a standard process involving an aluminum mold with no heating or cooling lines running through it, which means cycle times are a bit longer. As part of the scientific molding process, our molders independently optimize and monitor fill speed, hold pressure, and hold time, and periodically inspect part quality and cosmetics. During the molding process, we use an automated inline CMM to ensure dimensional accuracy, as well as generate a detailed process capability study and FAI report.
Get machined parts anodized and chromate plated with our quick-turn finishing option. Eligible materials include aluminum 6061/6082 and 7075.
Resin pellets are loaded into a barrel where they will eventually be melted, compressed, and injected into the mold’s runner system. Hot resin is shot into the mold cavity through the gates and the part is molded. Ejector pins facilitate removal of the part from the mold where it falls into a loading bin. When the run is complete, parts (or the initial sample run) are boxed and shipped shortly thereafter.
The cost will fluctuate based on the thermoplastics utilized. The most important predictor of your pricing per part will be the resin you use. If your parts need the use of an industrial resin, which is recognized for its toughness and chemical resistance, the supplies will cost a few pennies more than a commodity polymer, such as polyethylene. It is also less expensive to use resins derived from recyclable plastic.
Tolerances: Typically, Protolabs can maintain a machining tolerance of +/- 0.003 in. (0.08mm) with an included resin tolerance that can be greater than but no less than +/- 0.002 in./in. (0.002mm/mm).
GETTING A QUOTE WITH LK-MOULD IS FREE AND SIMPLE.
FIND MORE OF OUR SERVICES:
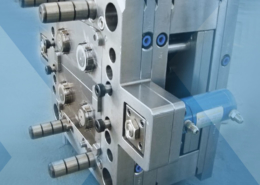
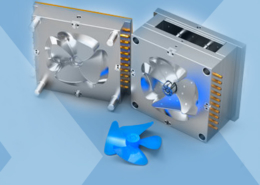
Plastic Molding

Rapid Prototyping
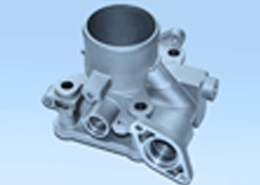
Pressure Die Casting
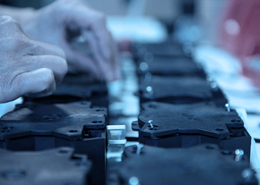
Parts Assembly
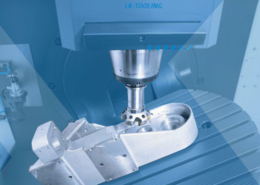