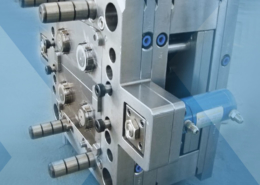
How Much Does an Injection Mold Cost - injection molding prototype cost
Author:gly Date: 2024-10-15
Polyethylene (PE or PET): Polyethylene is a very strong thermoplastic with an extremely high melting point and a high viscosity. Thin-walled, high-strength applications are the ideal application for polyethylene, and it is also frequently found in disposable plastic water bottles. Polyethylene boasts a high viscosity that makes it well-suited for more complex molds; however, mold setup and cooling times can be longer. For applications where recycling is a concern, polyethylene is one of the best choices you can make.
The material you use plays a role in the end function and performance of your product itself: choose the wrong material, and your product may not work properly. A more flexible resin isn’t suited to a function where rigidity and strength are required. More importantly, non-food grade or medical grade materials can present real health hazards and risks if used in food or medical functions.
Now that you know a few of the areas where material selection makes a difference, the following checklist can be a good reference point of factors you should consider:
As with all injection molded parts, it is important to maintain uniform wall thickness to avoid issues with warp and sink. Remember that it takes longer for thick walls to cool. Ensure that you have adequate draft so your part can eject from its mold easily. For PETG, between 1 and 3 degrees of draft is recommended. Thin sections should be reinforced with ribs and bosses, while thick sections should be replaced with gussets or fillets.
Tough Black (Loctite Henkel 3843) and Ceramic-Filled (BASF 3280) are two new advanced photopolymer materials now available for 3D printing.
Different resins have different qualities that play a role in the manufacturing process, like melting point, cooling point and viscosity. More complex molds may require a material that’s better able to reach all areas for full coverage, and different melting points and cooling points can help avert problems like sink and cavities in your product.
Knowing the requirements of your particular injection molding process (like mold design and complexity), as well as those of your end product, can help you choose a material with the qualities you need, at the lowest cost possible. Don’t end up paying a premium for material aspects and features that you don’t need.
Material selection plays an important part in just about every facet of the plastic injection molding process, so it’s critical not to overlook this step. Here, we’ll take a look at the “why” of material selection — how it affects your product and the manufacturing process — as well as the “what” — meaning, you’ll learn a bit about some of the most commonly used plastic injection molding materials, what their qualities are, and their functions.
Polystyrene (PS): Polystyrene is best for plastic injection molding where budget is a concern; however, there are tradeoffs in strength and other qualities. If a break-resistant product is required, it’s best to look elsewhere. Polystyrene is ideal, however, for disposable products, and is frequently used in food packaging as well as single-use lab applications like petri dishes. Note that polystyrene does not offer high resistance to heat (only up to about 212 degrees Fahrenheit/100 degrees Celsius).
Our digital factories create prototypes and low-volume parts fast, while our manufacturing network, offers advanced capabilities and volume pricing.
ABS: ABS is a very common thermoplastic that can be used for a wide variety of end products. It is relatively inexpensive and provides strong rigidity and resistance to breaking or shattering, even upon impact. It is also resistant to a number of acids and other corrosives, but not all of them. ABS is not suitable for food use, and it is flammable and shows poor resistance to sunlight. Aesthetically, ABS in its raw form appears white or translucent, although it can be colored using additives. ABS is found in applications like electronic casings, automotive components where shock resistance is important, and toys like Lego.
Polycarbonate (PC): Polycarbonate is a transparent thermoplastic that offers some of the strongest, most shatter-resistant construction available for plastic injection molded products. Polycarbonate is typically transparent in its raw form, and it is highly receptive to sterilization, making it well-suited for medical applications (although it may not be used for medical components intended for placement in the human body). While its strength and break resistance make polycarbonate a common choice in eyeglass lenses and some types of shatterproof or bulletproof glass, it is not very scratch resistant, and so will typically need to be treated or coated with a harder material after the injection molding process. Polycarbonate is also not especially resistant to repeated vibration or stress, as automotive or aerospace components would encounter, and should not be used for these applications.
Proto Labs, Inc. 5540 Pioneer Creek Dr. Maple Plain, MN 55359 United States P: 877-479-3680 F: 763-479-2679 E: [email protected]
Now, let’s take a look at some of the most common resins used in plastic injection molding, as well as some of their qualities and optimal uses.
Acrylic: Frequently used to mimic the appearance of glass, acrylic is used in applications like sunglasses and display cases. Acrylic has a high hardness rating, making it exceptionally scratch resistant, and it is also highly resistant to breakage.
The simple answer to the question of “why is material selection important for plastic injection molding?” is what we just mentioned — it factors into just about every aspect of the product development process. For instance:
Polyethylene terephthalate glycol is better known as PETG. It meets ISO 10993 and USP Class VI biocompatibility requirements. Tougher than its cousin, PET, it is highly processable, while remaining strong, transparent, and easily molded. Best of all, it’s a cost-effective material.
Polypropylene (PP): Polypropylene is commonly used in consumer-packaged goods like water bottles, as well as household items like garbage cans, pails and flatware. It is also frequently used in living hinges and scientific lab supplies due to its shatter-resistant properties. With its low cost, high strength and flexibility, polypropylene is ideally suited to high-volume production runs, and works well even in complex molds due to its very high viscosity. Polypropylene is readily available in a clear raw form, although it is naturally opaque.
Our helpful design aid demonstrates part features that are too thin or too thick, bad bosses, right and wrong ribs, and other considerations to be mindful of while designing parts for injection molding.
Get machined parts anodized and chromate plated with our quick-turn finishing option. Eligible materials include aluminum 6061/6082 and 7075.
Epoxy: Epoxy is a thermoset resin that as such, offers extremely high strength, as well as resistance to heat and many chemicals after curing. It is important to note that the qualities of epoxy differ based on the curing (or hardening) agent used, so be sure to have a thorough understanding of your product’s end requirements before choosing epoxy as a plastic injection molding resin. Due to its high electrical insulation abilities, epoxy is frequently used in circuits and transistors. Epoxy can also be found in motor and transformer components, as well as in marine applications, such as plugs.
GETTING A QUOTE WITH LK-MOULD IS FREE AND SIMPLE.
FIND MORE OF OUR SERVICES:
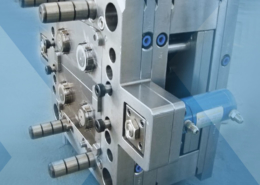
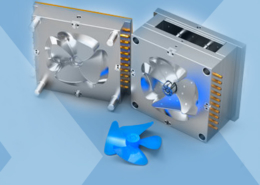
Plastic Molding

Rapid Prototyping
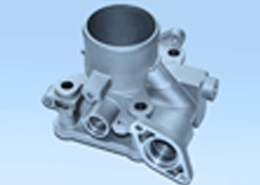
Pressure Die Casting
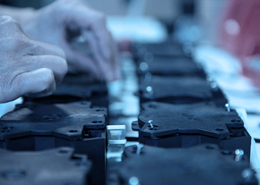
Parts Assembly
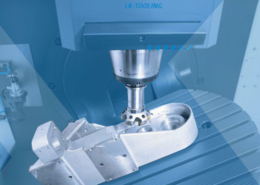