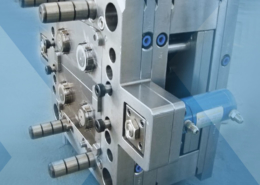
How do I make a custom mold for soft plastic lures? I don't ... - custom soft pl
Author:gly Date: 2024-10-15
Factory 1: Nanlv Industry Area, Xinji City, Hebei Province, China. Factory 2: Fudong Industry Area, Xinji City, Hebei Province, China.
Particles to expand mutual fused into the overall foaming process occurs in a closed cavity, the space between the particles decreases gradually with the foaming process until disappear, so into the cavity of the vapor flow resistance increases gradually, steam pressure rises to a predetermined pressure value, the pressure value is called moulded foam type pressure, namely the end of the moulded foam molding, closed this time of steam, stop the heating, ventilation with cooling stereotypes.
Steam moulded foam molding of products from the mold after into the chamber (50-60 ℃) and dry, take off products surface moisture.
Molding pressure is directly related to the density of foam plastics.In addition, the density of foamed plastics depends on the density of prefoamed particles.
Steam mould-pressure foaming is a common and economical method for the manufacture of expandable styrene foamed plastics and bulk materials.The method is to fill the mold cavity with prefoaming particles, close the mold and press the mold to prevent the foaming process from opening.
Steam through the mold wall hole or slot directly into the cavity surface and particle thermal softening, particle bubble hole evaporates into gas and vapor infiltration bubble hole, foaming agent particles further expansion and increase the volume, because of the limitation of cavity space expansion of particle filled cavity space and melt the massing of after cooling to finalize the design, and die out, which is the polystyrene foam plastics.
Second step: In the second step, the particles reach the softening temperature through heating. The infiltration of the foaming agent into gas and heating medium in the bubble hole causes the particles to expand further. Due to the limitation of mold cavity volume, the expanded particles fill all cavity space and fuse into a whole.
MoldWiz®; XTEND®; PasteWiz® and CleanWiz® are registered trademarks of Axel Plastics Research Laboratories Inc. © 2012-2024 Axel Plastics Research Laboratories, Inc. All rights reserved. Sitemap | Privacy Policy | Cookie Policy | Human Rights Commitment Statement
Please note, AXEL can provide other types of internal mold release for resins other than polyolefins. If you are rotationally molding nylon or other types of resin, please contact us for a recommendation.
Axel Plastics Research Laboratories, Inc. | info@axelplastics.com | 50 Cambridge Drive | Monroe, Connecticut 06468 | 1 (800) 332-AXEL | (203) 590-2000
Moulded foaming is the main manufacturing method of automatic foamed sheet machine for the foamed polystyrene foamed plastic products, such as the foamed plastic products for packaging and the foamed plastic bulk materials.
Sometimes, the easiest and best explanation comes from just seeing it, and that’s why we have this video portal. More here.
The following products represent those that are most commonly used in rotational molding. These releases are suitable for use with fabricated and cast aluminum and steel molds and plated metal surfaces. Solvent-based mold releases are generally preferable for cast iron molds.
GETTING A QUOTE WITH LK-MOULD IS FREE AND SIMPLE.
FIND MORE OF OUR SERVICES:
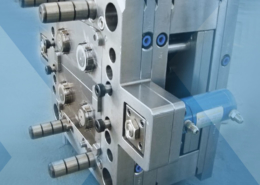
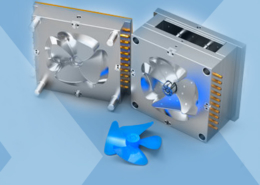
Plastic Molding

Rapid Prototyping
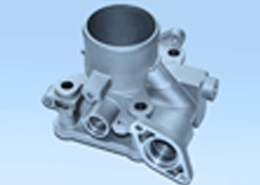
Pressure Die Casting
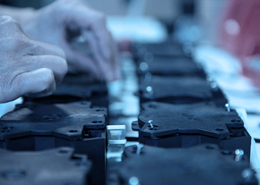
Parts Assembly
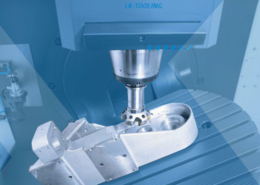