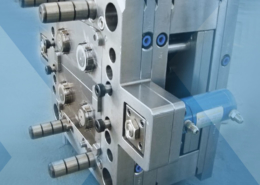
How Can You Solve The Ejected Mark Issues In Molded Parts - ejector rod injectio
Author:gly Date: 2024-10-15
Silicone over plastic. Adding a silicone layer to a plastic material such as PC for water resistance, sealing, and enhanced tactile properties.
Electronics. Overmolding ensures durability and strain relief for cable connectors, safeguarding cable connections in challenging environmental conditions.
At its core, rapid injection molding involves injecting thermoplastic resins into a mold at high pressure, which then cools and solidifies to form the desired part. This technique is renowned for its speed, which does not compromise the quality or the versatility of the produced parts. Whether for prototyping or small to medium-sized production runs, this method stands out for its ability to deliver reliable results swiftly.
Overmolding works by first placing the injection-molded part into a mold. Next, a second material is injected over or around the part. The two materials are then bonded together during the curing process.
Thermoplastic over metal. Coating metal parts with a protective or cushioning plastic layer, such as encasing steel components with PP, to enhance corrosion resistance and reduce noise or vibration.
What is Delrin and why is it unique among the many manufacturing materials available? Delrin, or POM-H (homopolymer acetal), is used in CNC machining, 3D printing and injection molding to create durable, precise components. This article explores Delrinâs properties and how to get the most out of the material.
Thermoplastic over thermoplastic. Using two different thermoplastic materials, such as a rigid plastic material like PC and a softer rubber-like material like TPU for improved grip or comfort.
Aerospace. Within aircraft interiors, overmolding enhances passenger comfort and cockpit functionality, seen in armrests, seat cushions, and control grips.
Rapid injection molding is cost-effective, especially for low to medium volume productions. The use of aluminum molds, which are less expensive and quicker to manufacture than traditional steel molds, significantly reduces upfront costs. This affordability enables companies to manage their budget more effectively while still achieving high-quality outputs.
What are the common applications of injection molding? What sets it apart as a manufacturing process? This article covers the key benefits of injection molding and provides insight into whether injection molding is right for your industryâs applications.
Despite its advantages, overmolding presents challenges in terms of design complexity, material compatibility, production costs, quality control, and specialized tooling requirements. Learn more about the challenges in order to overcome them.Â
Find out about the manufacturing technique used to injection mold a second material over or around a part to create a new one.
Tool design. Design molds with appropriate gating, runner systems, and cooling channels to ensure uniform material flow and efficient part production.
They are capable enough to manufacture anywhere from a few parts to thousands. There are many manufacturers who use this process for producing molding parts as per their client’s requirements. Most essentially, this is the most convenient way to meet the client’s needs and specifications effectively sans hassle.
To get a quote for your overmolding project, start by uploading a part. You can also contact our injection molding experts with any questions or special requirements.Â
Absolutely. By utilizing high-quality materials and precise manufacturing processes, rapid injection molding produces parts that meet or exceed the durability and performance standards of traditional injection molding methods.
Want to learn more about die casting? In this article, weâll take a look at the process, its history and current uses, advantages, design guidelines, and more.
In overmolding, a variety of materials can be used to achieve specific properties and functions. Several common combinations include:
Applying the following best practices can help ensure successful overmolding, leading to high-quality products with optimal functionality and aesthetics.
Why is it important to design draft angles for injection molding custom parts? This article covers why draft angles are essential and how to design them better to get the most out of your injection molding designs.
In this article, weâll take a look at common factors that influence the cost of injection molding, including equipment, labor, and materials â as well as tips for reducing manufacturing costs.
Complex design and engineering. Overmolding requires careful design considerations and engineering expertise to ensure proper material compatibility, bonding, and mold design, which can increase development time and costs.
Overmolded material placement. Position the overmolded material's injection points away from critical features and edges to avoid material entrapment or disruption.
Enhanced functionality. Overmolding allows the integration of different materials with distinct properties, resulting in improved grip, cushioning, insulation, or sealing, enhancing the overall functionality of the product.
Durability and protection. Overmolding can add a protective layer, such as a rubber coating, to shield delicate components from impact, moisture, or environmental factors, extending product lifespan.
Rapid injection molding stands out for its ability to streamline the journey from conceptual design to finished product, offering plenty of advantages.
Thermoplastic over elastomer. Combining a rigid plastic such as ABS with a flexible elastomer for products requiring both durability and flexibility, like tool handles or medical devices.
Although there is always a premium to pay for an exceptionally speedy turnaround, rapid injection molding is quite affordable as compared to the traditional process. The cost is of it inexpensive than might be expected owing to the automation procedure of this sort of mold making.
Overmolding improves grip, durability, aesthetics, and reduces assembly steps, creating versatile and comfortable products.
Level up your injection molding knowledge and find practical tips about selecting materials, working with draft angles, and reducing costs.
Avoid sharp corners. Rounded edges and corners help prevent stress concentration and facilitate material flow during the overmolding process.
Rapid injection molding provides unparalleled flexibility in product development. Design changes can be quickly implemented without significant cost penalties, allowing for iterative design improvements. This adaptability is essential for optimizing product design and functionality.
Selecting the right partner is crucial for the success of your rapid injection molding project. Here are key factors to consider:
Process complexity. Overmolding involves multiple steps and material transitions, increasing the complexity of the manufacturing process and potentially leading to quality control challenges.
While both processes share the core principle of injecting molten material into a mold, rapid injection molding is distinguished by its speed and flexibility. Standard injection molding is typically geared towards high-volume production, necessitating more extensive tooling and setup time. In contrast, rapid injection molding focuses on accelerating the production process, making it ideal for short runs and tight deadlines.
Overmolding involves placing an injection-molded part into a mold and injecting a second material to bond and create a single, integrated product.
Reduced assembly. Overmolding combines multiple components into a single piece, reducing the need for complex assembly processes, lowering labor costs, and minimizing the risk of assembly errors.
Draft angles. Incorporate draft angles to aid in easy part ejection from the mold, reducing the risk of damage during demolding.
How do you optimize part design for injection molding? This complete guide to designing for injection molding provides basic and advanced design tips, including guidelines for creating snap-fits, living hinges and undercuts, and accounting for optimial surface finishes.
Embracing rapid injection molding is a strategic decision that can significantly enhance your product development process.
Industrial tools. Overmolding improves ergonomics in handheld power tools, reducing operator fatigue and enhancing control during industrial use.
When producing parts with injection molding, understanding the range of materials that are available is crucial. Find out more about those materials, their properties, and factors to consider when choosing a material for injection molded parts.
One of the most significant advantages of rapid injection molding is its unmatched speed and efficiency. The process allows for the swift development of prototypes, facilitating a faster transition to production stages. This rapid progression is crucial for beating competitors to market and testing concepts without costly delays.
Rapid injection molding method is revolutionizing how products come to life, blending efficiency and speed with engineering. This process makes it possible to manufacture many durable consumer and industrial items cheaper than everything else. It produces around 32% of plastics by weight.
Construction. Safety equipment such as hard hats and tool handles benefit from overmolding, providing impact resistance and improved grip for construction workers.
Proper wall thickness. Maintain consistent and appropriate wall thickness to ensure even material flow and prevent defects like sink marks or voids.
While tooling costs can be higher, overmolding often reduces assembly and enhances product lifespan, justifying the investment.
The process offers remarkable versatility, accommodating a wide range of materials and design specifications. Whether you’re working with engineering resins, ABS, polypropylene, or polycarbonate, rapid injection molding meets diverse material requirements. Additionally, it supports complex designs, ensuring that the final parts meet precise specifications.
To demystify the process, it’s crucial to break down the main stages involved in rapid injection molding. Each phase plays its role in ensuring the final product meets the specified requirements with precision:
In a nutshell, you can get your injection molded plastic part within a short span of time to market. To get the best quality of Rapid Injection Molding Services, get in touch with 3ERP for a free quote. We’ll gladly offer advice about your best options. Combining our expertise, engineering capabilities, and advanced technology we can offer rapid tooling solutions
Consider shrinkage. Account for material shrinkage differences between the injection-molded part and overmolded material to prevent warping or dimensional inconsistencies.
Packaging. Overmolding contributes to the creation of ergonomic and comfortable grips on packaging machinery handles, improving operator experience and efficiency.
Quality control. Ensuring consistent bonding between different materials can be challenging, and defects like delamination or inconsistent adhesion may arise, requiring meticulous quality control measures.
Ensuring proper material bonding, design intricacies, and quality control are challenges in achieving consistent overmolding results.
Want to learn more about exactly how an injection molding machine functions, as well as its individual parts? This article puts injection molding machines under the microscope, with detailed descriptions of their components and an in-depth guide to the injection molding process.
Overmolding is a manufacturing process that is often used in injection molding, in which a part is encased or covered with a second material â typically a rubber or plastic â to create a single, integrated product. It enhances product durability, grip, aesthetics, and functionality.
Improved aesthetics. Different colors, textures, and finishes can be achieved through overmolding, enhancing the visual appeal of products and enabling branding opportunities.
A direct consequence of the process’s speed and efficiency is a substantial reduction in time to market. Companies can swiftly move from concept to commercialization, gaining a competitive edge in fast-paced markets. This agility is crucial for responding to consumer demands and market trends.
Rapid Tooling: Offers a cost-effective solution for producing molds for injection molding, especially beneficial for short production runs and prototyping. This application is crucial for industries that require molds quickly to test market reactions or to start production of parts without the delays associated with traditional tooling methods.
Costly tooling and equipment. The need for specialized molds and injection molding equipment tailored to overmolding can lead to higher initial investment and tooling costs compared to traditional molding processes.
Yes, rapid injection molding can manufacture complex parts. Advanced mold design and manufacturing technologies, like 3D printing and EDM, allow for intricate features and precise tolerances, making it ideal for complex components.
Find out about the manufacturing technique used to injection mold a second material over or around a part to create a new one.
Material compatibility. Choose materials that bond well together and have similar melting temperatures to ensure a strong and reliable bond between layers.
In injection molding, âovermoldingâ refers to a process where multiple materials are used to create a cohesive, often multi-textured product with improved qualities and versatility. Hereâs a guide to using the technique, including how it works, its common industrial uses, and more.
What are the most common defects in the injection molding process and how do you avoid them? This article provides six essential design tips for avoid production defects while reducing the cost and lead time of your molded parts.
The precision of rapid injection molding leads to minimal waste production, aligning with sustainable manufacturing practices. The efficient use of materials not only conserves resources but also reduces the overall environmental footprint of the manufacturing process.
 Overmolding offers versatile solutions to manufacturing challenges by combining different materials to enhance product functionality, durability, ergonomics, and aesthetics. The following are several of the advantages of overmolding.Â
The cost-effectiveness of rapid injection molding depends on the project scope. For low to medium volume productions and prototyping, it’s often more cost-efficient than traditional methods due to lower tooling costs and faster turnaround times.
Lastly, rapid injection molding allows companies to respond swiftly to market changes. Whether adjusting to new consumer preferences or incorporating the latest technological advancements, this process supports dynamic adaptation, ensuring businesses remain relevant and competitive.
Specialize in CNC machining, 3D printing, urethane casting, rapid tooling, injection molding, metal casting, sheet metal and extrusion
Below are 8 key industries that significantly benefit from rapid injection molding, showcasing the diverse applications and use cases of this innovative technology.
Limited material options. Material compatibility is crucial in overmolding, limiting the selection of suitable combinations â and potentially restricting the ability to achieve specific material properties.
Robotics. Overmolded grippers provide robotic systems with a balance of flexibility and rigidity, enabling secure handling of diverse objects.
Rapid injection molding represents a significant advancement in manufacturing, offering speed, flexibility, and high-quality production.
Central to rapid injection molding is a range of specialized equipment, each serving a critical role in the creation of high-quality parts, tooling and prototypes.
Learn what to consider when making a choice between 3D printing and injection molding, the benefits of each manufacturing method, and more.
Rapid injection molding is a type of injection molding designed to produce parts quickly and efficiently, bridging the gap between initial prototypes and mass production. It is exceptionally suited for generating anywhere from a few units to 10,000 parts within a matter of weeks. It embodies the intersection of speed and accuracy, making it a go-to choice for companies across various industries.
Design for bonding. Create proper surface features, undercuts, and interlocking structures to facilitate mechanical bonding between the injection-molded part and the overmolded material.
Venting. Integrate venting features in the design to allow air and gases to escape during injection, preventing voids and trapped air pockets.
Molds for rapid injection molding differ significantly from those used in traditional injection molding, mainly due to the focus on speed and flexibility.
Achieving precision and consistency is paramount in manufacturing. Rapid injection molding excels in producing parts with tight tolerances and uniform quality. This precision ensures that every part functions correctly, meeting or exceeding the performance standards set by the project.
The future outlook for rapid injection molding in the manufacturing industry is promising. As technologies evolve and demand for faster, more efficient production continues to rise, rapid injection molding will remain a crucial tool for innovators and manufacturers alike.
Want to learn how to design undercuts that donât cause damage to your parts? Check out our article, which offers tips and tricks for DFM with undercuts, examples of when you might need them, and more. Undercuts in injection-molded parts present a host of challenges to designers and manufacturers. In this article, weâll take a look at the definition of undercuts, their purpose, applications, and tips for designing parts with them.
Ergonomic design. Overmolding enables the creation of ergonomic shapes and contours, enhancing user comfort and interaction, making products more user-friendly and intuitive to use.
Various combinations include thermoplastics, elastomers, metals, and silicone, chosen for desired properties like grip, flexibility, or sealing.
Medical equipment. Overmolding is employed in medical device housings, enhancing durability and ergonomic design for instruments like handheld scanners and diagnostic tools.
GETTING A QUOTE WITH LK-MOULD IS FREE AND SIMPLE.
FIND MORE OF OUR SERVICES:
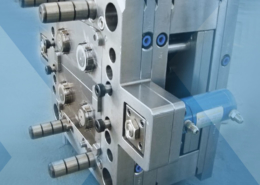
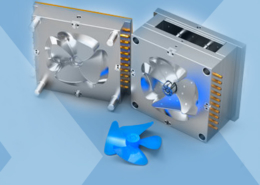
Plastic Molding

Rapid Prototyping
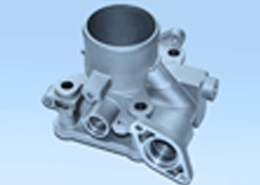
Pressure Die Casting
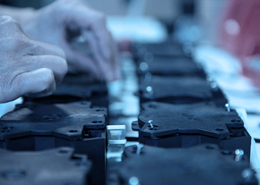
Parts Assembly
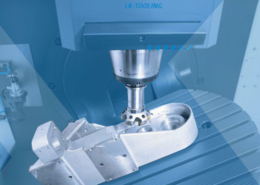