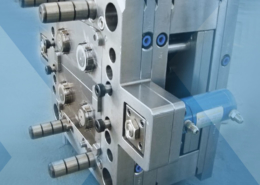
How Do You Choose the Right Plastic for Your Prototype Part? - prototype plastic
Author:gly Date: 2024-10-15
Injection molding means that the HDPE plastic is shaped by pressure in a heated mold. It is a very fast production method and the labor cost is low. It is popular with the production of smooth surface products in the production of complicated parts. Since we are working with a large number of injection equipment, our company is a competent company that fulfills the needs with the most affordable prices.
Maspi aspires to be among the best plastic molding companies in the use of recycled plastic materials. Reuse of discarded waste elements is an unavoidable driver for the company, this in fact generates value not only from an economic point of view but also in terms of sustainability.
Each recycled material in order to be properly reused must be carefully separated and identified exactly so that it can later be properly reprocessed.
Post-consumer recycled plastics are items used and consumed by humans such as, plastic bottles, tetrapak, or food tubs. Even these can be reused for the production of new items as long as one is able to properly separate the different types of plastic. In the furniture industry, this type of recyclate has not yet been used frequently, so Maspi is engaging in the study and analysis of a new polymer from tetrapak recycling in order to create new more sustainable designs.
Post-consumer recycled plastics are items used and consumed by humans such as, plastic bottles, tetrapak, or food tubs. Even these can be reused for the production of new items as long as one is able to properly separate the different types of plastic. In the furniture industry, this type of recyclate has not yet been used frequently, so Maspi is engaging in the study and analysis of a new polymer from tetrapak recycling in order to create new more sustainable designs.
In the HDPE production market, the products that are produced with injection molding technique constitute 30% of total production. HDPE injection products, which are used in many areas, lead the market since they provide many advantages. The melting of HDPE by the heat and shaping it in the injection machine is the most common method for producing plastic materials. The process consists of closing, injection, ironing, cooling, mold opening and removal from the mould. Every stage is performed automatically and the finished part is removed from the mold during the extraction process.
In general, HDPE injection has 700-2000 kgf / cm² pressure, 160-250ºC temperature and 10-30 seconds production time. There are different injection devices that produce many products including the smallest parts, and the largest plastic parts. The hot runner system is used in injection molding for reducing the need for the material, labor and machine capacity.
HDPE injection material is used in the production of covers, cases, plastic pallets, kitchen items, toys and many other products and this is a high density polyethylene material. With the injection molding, the HDPE takes every shape. Since the values of temperatures and pressure value depending on the product, it can be widely used.
Maspi reuses in each of its products, thanks to Restylon co-injection technology, certified post-industrial recycled material that allows to drastically cut CO2 emissions by one-third and to avoid having to dispose of waste from the production area, which is instead stored and reinserted when needed.
© 2021 © MASPI S.R.L. | Via Castegnate, 86 - 24030 Terno d'Isola (BG) | Tel. +39.035.4944117 | P.IVA IT00781490164 Web Horizondesign
Maspi aspires to be among the best plastic molding companies in the use of recycled plastic materials. Reuse of discarded waste elements is an unavoidable driver for the company, this in fact generates value not only from an economic point of view but also in terms of sustainability. Maspi reuses in each of its products, thanks to Restylon co-injection technology, certified post-industrial recycled material that allows to drastically cut CO2 emissions by one-third and to avoid having to dispose of waste from the production area, which is instead stored and reinserted when needed. Each recycled material in order to be properly reused must be carefully separated and identified exactly so that it can later be properly reprocessed.
Post-industrialrecycled materials are the residual and discarded materials from the first production of a plastic items in companies. They are the most widely used materials in the plastic recycled sector because of their greater availability and facility of certification. At Maspi, each plastic material is carefully certified to be reused in a second production. This type of recyclate is the most used by Maspi for the Restylon Co-injection production.
Post-industrialrecycled materials are the residual and discarded materials from the first production of a plastic items in companies. They are the most widely used materials in the plastic recycled sector because of their greater availability and facility of certification. At Maspi, each plastic material is carefully certified to be reused in a second production. This type of recyclate is the most used by Maspi for the Restylon Co-injection production.
We have started our journey in 2012 to facilitate our customers’ lives and to offer many opportunities that would enrich your lives. Over time, we have developed ourselves and have succeeded in becoming a respectable, reliable and global company in the petrochemical sector, after increasing our resources and enhancing our product range.
GETTING A QUOTE WITH LK-MOULD IS FREE AND SIMPLE.
FIND MORE OF OUR SERVICES:
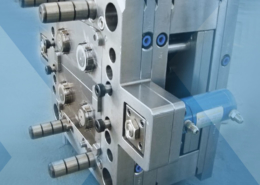
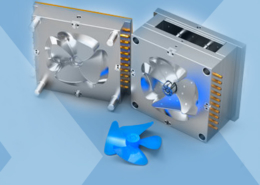
Plastic Molding

Rapid Prototyping
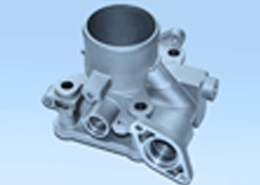
Pressure Die Casting
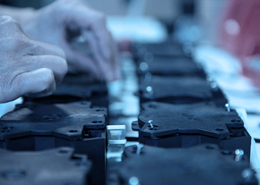
Parts Assembly
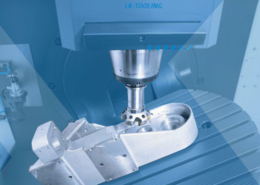