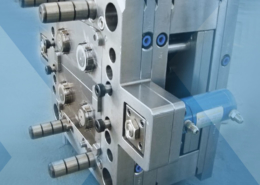
Plastic Molding 1 2: Revolutionizing Manufacturing
Author:gly Date: 2024-06-08
Plastic molding 1 2 stands at the forefront of modern manufacturing, offering unparalleled versatility, efficiency, and precision. From intricate components in automotive engineering to everyday consumer products, plastic molding 1 2 has revolutionized the production landscape. In this article, we delve into the intricacies of plastic molding 1 2, exploring its various aspects and implications.
1. Evolution of Plastic Molding
Plastic molding has undergone significant evolution since its inception, propelled by advancements in materials science, technology, and manufacturing processes. Initially limited to simple shapes and designs, modern plastic molding 1 2 techniques boast remarkable sophistication, enabling the production of complex geometries with micron-level precision. Injection molding, blow molding, and compression molding are among the prominent methods driving this evolution, each offering distinct advantages in terms of cost-effectiveness, scalability, and product quality.
The transition from conventional molding to plastic molding 1 2 represents a paradigm shift in manufacturing, unlocking new possibilities across diverse industries. This evolution has been fueled by relentless innovation, with manufacturers continually pushing the boundaries of what is achievable with plastic materials.
2. Advanced Materials and Applications
The versatility of plastic molding 1 2 is amplified by the wide array of materials available for use. Traditional thermoplastics such as polyethylene and polypropylene remain staples in the industry, prized for their affordability and ease of processing. However, the emergence of engineering-grade polymers and composite materials has expanded the application potential of plastic molding 1 2, catering to demanding requirements in terms of strength, durability, and chemical resistance.
From aerospace components to medical devices, the application spectrum of plastic molding 1 2 is vast and diverse. High-performance polymers like PEEK and ULTEM have found niche applications in industries where extreme conditions and stringent regulatory standards prevail. Moreover, the advent of bio-based and recyclable plastics underscores the industry's commitment to sustainability and environmental stewardship.
3. Precision Engineering and Quality Assurance
At the heart of plastic molding 1 2 lies precision engineering, a cornerstone of modern manufacturing. Computer-aided design (CAD) and computer-aided manufacturing (CAM) technologies play pivotal roles in optimizing tooling designs, minimizing material wastage, and streamlining production workflows. Moreover, real-time monitoring and process control systems ensure consistency and reproducibility in part quality, mitigating the risk of defects and deviations.
Quality assurance is paramount in plastic molding 1 2, with stringent standards and protocols governing every stage of the production cycle. Advanced inspection techniques, including dimensional analysis and non-destructive testing, safeguard the integrity of manufactured components, instilling confidence in end-users and stakeholders alike.
4. Future Perspectives and Challenges
Looking ahead, the future of plastic molding 1 2 holds immense promise, albeit with certain challenges to overcome. The ongoing pursuit of sustainability and circular economy principles necessitates the development of biodegradable materials and closed-loop recycling systems. Additionally, the advent of additive manufacturing technologies presents both opportunities and disruptions to traditional molding processes, prompting industry players to adapt and innovate.
Furthermore, the convergence of digitalization and automation is poised to redefine the manufacturing landscape, ushering in an era of smart factories and interconnected supply chains. Harnessing the potential of artificial intelligence and predictive analytics will be crucial in optimizing production efficiency, minimizing downtime, and driving continuous improvement.
In conclusion, plastic molding 1 2 epitomizes the synergy between innovation, engineering prowess, and market demand. Its transformative impact extends far beyond the realm of manufacturing, shaping the way we design, produce, and consume goods. By embracing emerging technologies and embracing sustainability, the industry is poised to chart a course towards a more efficient, resilient, and sustainable future.
This article has explored the multifaceted realm of plastic molding 1 2, shedding light on its evolution, applications, engineering intricacies, and future prospects. As a cornerstone of modern manufacturing, plastic molding 1 2 continues to push the boundaries of what is achievable, driving innovation and progress across diverse industries. Embracing the principles of sustainability and digitalization will be instrumental in overcoming future challenges and unlocking new opportunities in the dynamic landscape of plastic molding 1 2.
GETTING A QUOTE WITH LK-MOULD IS FREE AND SIMPLE.
FIND MORE OF OUR SERVICES:
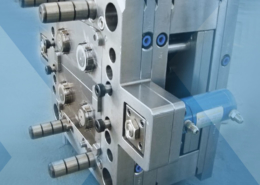
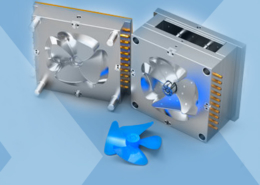
Plastic Molding

Rapid Prototyping
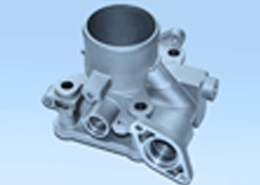
Pressure Die Casting
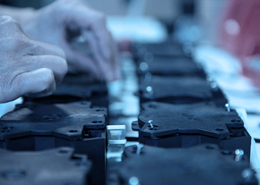
Parts Assembly
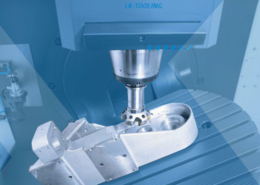