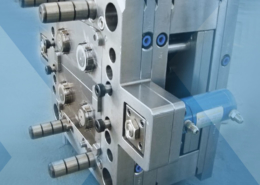
Exploring Plastic Molded Products: A Comprehensive Analysis
Author:gly Date: 2024-06-08
Plastic molded products constitute a significant portion of modern manufacturing, offering versatility, affordability, and efficiency in various industries. This article provides an in-depth exploration of plastic molded products, covering their significance, applications, manufacturing processes, sustainability considerations, and future prospects.
1. Introduction
Plastic molded products encompass a broad spectrum of items produced through injection molding, blow molding, or compression molding techniques. These products serve diverse purposes, ranging from consumer goods to automotive components and medical devices. Their ubiquity in everyday life underscores their importance and relevance in contemporary manufacturing.
2. Applications
Plastic molded products find extensive applications across industries such as:
Consumer Goods:
From kitchenware to electronic casings, plastic molded products dominate the consumer goods market due to their cost-effectiveness and design flexibility.
Automotive:
Components like dashboards, bumpers, and interior trims rely heavily on plastic molding for their production, enabling lightweighting and intricate designs.
Medical:
Medical devices and equipment often utilize plastic molded parts for their sterilizability, biocompatibility, and ease of fabrication.
3. Manufacturing Processes
Plastic molded products undergo several manufacturing processes, including:
Injection Molding:
This widely-used technique involves injecting molten plastic into a mold cavity under high pressure, allowing for complex geometries and mass production.
Blow Molding:
Ideal for hollow objects like bottles and containers, blow molding forms plastic by inflating a heated hollow tube, shaping it against a mold cavity.
Compression Molding:
Suited for larger, thicker parts, compression molding involves placing preheated plastic in a heated mold cavity and applying pressure until it solidifies.
4. Design Considerations
Designing plastic molded products requires attention to:
Material Selection:
Choosing the right thermoplastic material based on properties like strength, durability, and chemical resistance is crucial for product performance.
Tooling Design:
Optimal mold design influences part quality, cycle time, and production cost, necessitating expertise in mold flow analysis and tooling optimization.
Structural Integrity:
Ensuring adequate wall thickness, ribbing, and fillets in the design minimizes defects like warping, sink marks, and part distortion.
5. Sustainability
The sustainability of plastic molded products involves:
Recyclability:
Selecting recyclable plastics and designing products for ease of disassembly facilitate recycling and circularity, reducing environmental impact.
Biodegradability:
Exploring biodegradable plastics derived from renewable sources offers alternatives to conventional plastics, mitigating plastic pollution.
Resource Efficiency:
Optimizing material usage, minimizing waste, and employing energy-efficient manufacturing processes contribute to sustainable production practices.
6. Challenges and Opportunities
Despite their numerous advantages, plastic molded products face challenges such as:
Environmental Concerns:
The proliferation of plastic waste poses environmental threats, necessitating innovations in recycling, bioplastics, and waste management.
Regulatory Compliance:
Evolving regulations regarding plastic usage, recycling targets, and environmental standards compel manufacturers to adapt and innovate.
Technological Advancements:
Emerging technologies like 3D printing and advanced materials offer opportunities for enhancing design flexibility, reducing lead times, and improving product performance.
7. Future Outlook
The future of plastic molded products lies in:
Advanced Materials:
Continued research into bio-based polymers, nanocomposites, and recyclable materials will drive sustainability and performance improvements.
Digitalization:
Adoption of digital design tools, simulation software, and additive manufacturing technologies will streamline product development and customization.
Circular Economy Initiatives:
Embracing circular economy principles, such as closed-loop recycling and product life extension, will foster a more sustainable approach to plastic manufacturing.
Conclusion
Plastic molded products constitute a vital aspect of modern manufacturing, offering versatility, efficiency, and innovation across diverse industries. By addressing design considerations, sustainability challenges, and technological advancements, the industry can navigate towards a more sustainable and resilient future. Embracing innovation and collaboration will be key in shaping the next generation of plastic molded products.
GETTING A QUOTE WITH LK-MOULD IS FREE AND SIMPLE.
FIND MORE OF OUR SERVICES:
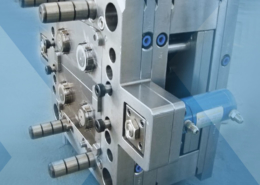
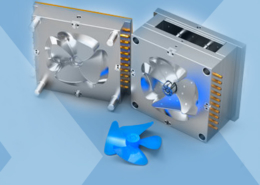
Plastic Molding

Rapid Prototyping
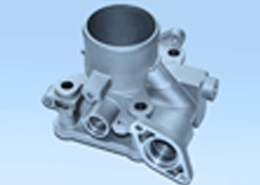
Pressure Die Casting
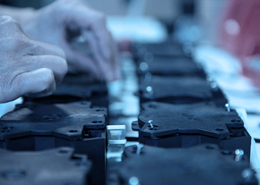
Parts Assembly
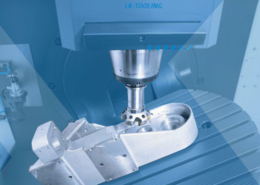