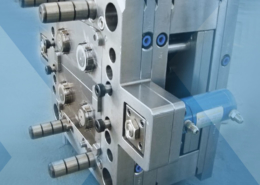
Plastic Molding 1: Revolutionizing Manufacturing Processes
Author:gly Date: 2024-06-08
Plastic molding, particularly Plastic Molding 1, stands at the forefront of modern manufacturing processes, reshaping industries and revolutionizing production capabilities. This article delves into the intricacies of Plastic Molding 1, shedding light on its significance, processes, applications, and future prospects.
The Genesis of Plastic Molding 1
Plastic Molding 1 marks a significant advancement in the realm of manufacturing, characterized by precision, efficiency, and versatility. Originating from the innovative fusion of engineering and material sciences, Plastic Molding 1 introduces novel techniques and materials, paving the way for groundbreaking achievements in various sectors.
Evolution of Plastic Molding Techniques
The evolution of plastic molding techniques led to the emergence of Plastic Molding 1, driven by the quest for enhanced performance, cost-effectiveness, and sustainability. From conventional injection molding to cutting-edge additive manufacturing, each iteration contributed to refining processes and expanding possibilities.
Technological Breakthroughs
Technological breakthroughs, such as computer-aided design (CAD), simulation software, and robotic automation, play a pivotal role in optimizing Plastic Molding 1 processes. These innovations empower manufacturers with unprecedented control, precision, and scalability, driving the adoption of Plastic Molding 1 across industries.
Versatility and Applications
Plastic Molding 1 transcends traditional boundaries, offering unparalleled versatility and adaptability to diverse applications.
Automotive Industry
In the automotive industry, Plastic Molding 1 revolutionizes vehicle design, enabling the production of lightweight, aerodynamic components with superior strength and durability. From intricate interior panels to structural components, plastic molding technologies enhance performance while reducing fuel consumption and emissions.
Healthcare Sector
In the healthcare sector, Plastic Molding 1 facilitates the manufacturing of precision medical devices, implants, and packaging solutions. With biocompatible materials and micro-scale fabrication capabilities, plastic molding technologies contribute to advancements in diagnostics, treatment, and patient care.
Consumer Electronics
In the realm of consumer electronics, Plastic Molding 1 drives innovation, enabling the production of sleek, ergonomic devices with seamless integration of functionalities. From smartphone casings to wearable gadgets, plastic molding technologies elevate the user experience while meeting stringent quality and safety standards.
Sustainability and Environmental Impact
Plastic Molding 1 underscores the industry's commitment to sustainability, addressing environmental concerns and promoting circular economy principles.
Material Innovations
Material innovations, such as biodegradable polymers and recycled plastics, mitigate the environmental footprint of plastic molding processes. By embracing sustainable alternatives, manufacturers uphold ecological stewardship and reduce dependence on finite resources.
Waste Reduction Strategies
Waste reduction strategies, including lean manufacturing principles and closed-loop recycling systems, minimize material wastage and optimize resource utilization throughout the product lifecycle. Through continuous improvement initiatives, Plastic Molding 1 cultivates a culture of environmental responsibility and resource efficiency.
Future Perspectives and Challenges
As Plastic Molding 1 continues to evolve, its future trajectory is shaped by emerging trends, technological advancements, and societal demands.
Advancements in Materials Science
Advancements in materials science, such as smart polymers and self-healing materials, hold the promise of further enhancing the capabilities and functionalities of Plastic Molding 1. By harnessing the potential of advanced materials, manufacturers can unlock new opportunities for innovation and differentiation.
Integration of Industry 4.0 Technologies
The integration of Industry 4.0 technologies, including artificial intelligence, internet of things (IoT), and digital twinning, transforms Plastic Molding 1 into a connected, intelligent manufacturing ecosystem. Real-time data analytics and predictive maintenance optimize production efficiency and enable agile, responsive operations.
Addressing Regulatory and Ethical Considerations
Addressing regulatory and ethical considerations, such as product safety, intellectual property rights, and workforce well-being, is essential for the sustainable growth of Plastic Molding 1. Collaboration between stakeholders, policymakers, and industry leaders is crucial to fostering a conducive environment for responsible innovation and ethical practices.
Conclusion: Shaping the Future of Manufacturing
In conclusion, Plastic Molding 1 represents a paradigm shift in manufacturing processes, driven by innovation, sustainability, and adaptability. With its transformative capabilities and endless possibilities, Plastic Molding 1 is poised to shape the future of manufacturing, empowering industries to achieve greater efficiency, agility, and resilience. Embracing the principles of continuous improvement and responsible innovation, we can harness the full potential of Plastic Molding 1 to create a more sustainable, prosperous future for generations to come.
GETTING A QUOTE WITH LK-MOULD IS FREE AND SIMPLE.
FIND MORE OF OUR SERVICES:
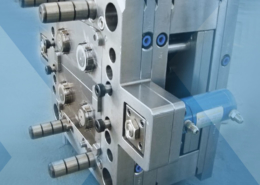
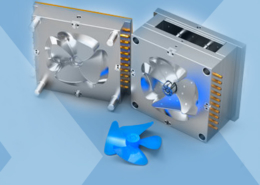
Plastic Molding

Rapid Prototyping
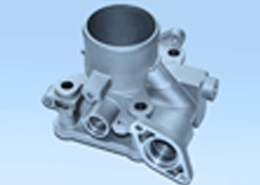
Pressure Die Casting
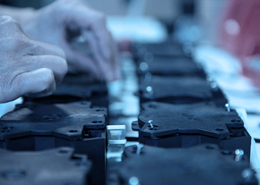
Parts Assembly
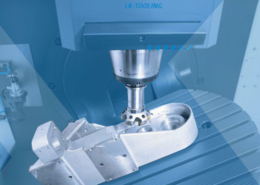