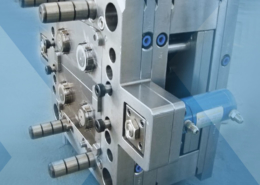
Extreme Molding: Silicone Injection Molding Leaders in the US - us injection mol
Author:gly Date: 2024-10-15
Plastic injection molding machines play a crucial role in determining the quality and consistency of injection molding results. Several factors related to the machine can affect the injection process and ultimately influence the quality of the molded parts such as: Clamping force, Injection Pressure and Speed, Injection Volume and Shot Size, Temperature Control & Cooling system.
How much will my injection molding project cost?Estimate the cost of your injection molding project with us. HLH Rapid has over 20 years of experience in building custom tools and plastic injection moulded parts for engineers and industrial designers in a wide range of industries from automotive, medical, electronic devices and more. We can build low-cost and high quality tools from a wide range of material grades and well designed tools.To get started, simply submit your 3D drawings and project details to our site submission form to get a free injection moulding quote or to speak with an expert from our engineering team.
Plastic Injection Parts are manufactured using the injection molding process, which is one of the most popular methods for producing plastic parts and components. In the process, the plastic injection parts can be mass-produced quickly and cost-efficiently.
Plastic Raw Material (Resin) significantly impacts the final product's properties, including strength, flexibility, durability, and appearance. Different plastics have instinct melting points, shrinkage rates, flow characteristics, and mechanical properties (tensile strength, impact resistance, elasticity…), which can affect how to design the mold, and how they behave during cooling and solidification.
Several popular types of mold: two-plate mold, three-plate mold, hot runner mold, cold runner mold, multi-cavity mold.
Firstly, we would like to offer an overview about Plastic Injection Process, its Pros & Cons, Materials and Applications in general.
3. Size and Weight Limitations: may not be suitable for very large or heavy parts due to equipment and handling limitations.
This process involves 2 main stages. First, inject molten material, typically thermoplastic or thermosetting polymers, into a pre-designed mold cavity under high pressure and heat. Second, once the material cools and solidifies within the mold, the finished product is ejected. Depending on a specific item, the mold can produce one or many items per injection, which we call a number of gates per mold.
Amorphous materials: lack a regular molecular structure, a random arrangement of polymer chains, resulting in solidifying more rapidly, shorter cycle times, making amorphous plastics suitable for simple design and high-volume production.
1. High Initial Tooling Costs: perhaps expensive pre-designed molds (tooling), particularly for complex parts with intricate features.
Additionally, despite with the same machine, different parameters set up definitely affect the finished injection result. Thus, the injection molding process parameters must be carefully controlled to achieve optimal results. These parameters include injection pressure, injection speed, melt temperature, mold temperature, cooling time, and holding pressure and time etc.
There are several things you can do to help control and lower costs when it comes to mould making. The top tooling cost reduction tips include:
During the injection process, crystalline materials tend to solidify more slowly compared to amorphous materials, resulted in better flow, which can be advantageous for molding intricate or large parts.
Injection molding is a manufacturing process widely known for its ability to produce parts cost effectively and consistently. While the process comes with significant cost benefits, unlike 3D printing and CNC machining, it demands a high level of ‘financial commitment.’ In this article we will go through How much does injection molding cost?So, how much can you expect injection molding to cost? Injection molding projects can cost anywhere from $10,000 or less to $100,000. The total cost of injection molding quote is essentially made up of two parts: mould cost + part cost. Mold Cost (Tooling Cost)The injection molding mold cost is also known as the tooling cost. Tooling refers to the design and manufacturing of the mold used to create injection-molded parts and is often the most expensive component of an injection molding project. Simple molds are typically in the $3,000 to $6,000 range while the price for larger, more complex, higher-production / steel moulds, or multi-cavity moulds can cost from $7,000 and up. Factors that determine tooling costs in injection molding include:1. MaterialsThe most common materials used to make molds are steel and aluminum, with steel lasting longer. While it’s often said that aluminum costs less, this is not always the case. High-quality but low-cost Chinese steel grades, such as S50C and P20, suitable for rapid tooling and low-volume production purposes, can serve as cheaper alternatives to aluminium. 2. Machining TimeThis is largely determined by the complexity and size of the mold, the number of cavities in the mold, and the level of precision required. Undercuts mean side actions, sliders and lifters which means added complexity, more work and higher costs. If you can reduce these features as much as possible and keep your design simple, you will significantly save on lead time and costs. 3. QuantityQuantity of parts required will impact two fold, first in the tool design itself. If you are looking at very high numbers of parts it might make sense to go with multi-cavity tools, which are larger and more expensive but will bring part costs down. Also the higher the quantity required the better the steel used to machine the cavity, core and inserts will need to be. Low quantities can often be realized using low grade steels or aluminiums’ bringing costs down. 4. TexturesAchieving specific textures or finishes by applying an SPI or VDI finish on the molded part can will impact the costs of your tool. High polished or transparent finishes require both better quality steels and much more work to achieve than a standard polish. To keep costs down, only requests high quality finishes where necessary. Tips to reduce injection mold tooling costsThere are several things you can do to help control and lower costs when it comes to mould making. The top tooling cost reduction tips include: Getting rid of undercuts as they make the tooling process more complicated and costly.Only specify tolerance where necessary.Only requests high quality textures and finishes where necessary.Planning ahead to determine the quantity required to optimize the selection of tooling type (multi-cavity, etc.) and material grade (low-grade aluminium or steels, etc.).Consider Chinese mold manufacturers for steel tooling. Part CostOnce the initial costs of the molds are covered, the cost per unit during manufacturing is relatively low. Typically, you can expect the cost per part to range from $0.20 to $10.00 per piece or higher, depending on the quantity. Factors that determine injection molding part unit costs include:1. MaterialPlastic pellet resins used in injection molding can range from $1 per kg to $5 per kg or higher, depending on the type of material. Specialty materials, such as glass-filled polymers or elastomers used to achieve specific properties, will typically incur higher costs. To reduce costs, stick to readily available, easy to process material like PP or ABS as far as possible. 2. Cycle timeCycle time or injection moulding time includes setup and running time for each part, this is where the manufacturer’s overheads are. More intricate designs, parts with complex features or larger parts may slow down the time it takes to remove the part from the mold, increasing overall cycle time and costs. Keep in mind that a high-viscosity will require longer injection and cooling time. 3. Secondary OperationsAny additional processes such as assembly, post-molding treatments, or finishing, will increase the unit cost. To keep molding costs and time and down, if it can be done in the tool itself, you should work with your supplier to try and achieve it that way. Tips to reduce the injection molding per part costsThere are several things you can do to help lower the overall per part cost. The top tips to reduce the injection moulding per part costs include: Simplify part geometry to facilitate easier mold release and less wastage.Consider standard resins over specialty materials unless specific properties are essential.Design parts with finishes in mind to minimize additional post-processing steps.
This is largely determined by the complexity and size of the mold, the number of cavities in the mold, and the level of precision required. Undercuts mean side actions, sliders and lifters which means added complexity, more work and higher costs. If you can reduce these features as much as possible and keep your design simple, you will significantly save on lead time and costs.
4. Wide Material Selection: a wide range of thermoplastic and thermosetting materials, offering flexibility in material selection to meet specific performance requirements.
Injection molding is a manufacturing process widely known for its ability to produce parts cost effectively and consistently. While the process comes with significant cost benefits, unlike 3D printing and CNC machining, it demands a high level of ‘financial commitment.’ In this article we will go through
Material Max Temp Chemical resistance Tensile strength (psi) Flexural strength (psi) Impact strength (ft-lb/in) Several Applications POM 180~230oC Excellent 6,000~ 22,000 120,000~ 170,00 0.8~2 automotive parts, valve ball, piston, bushing, wheels PP 65~148oC Excellent 4,500~ 18,500 210,000~ 1,500,000 1.4~5.5 food storage and packing HDPE 120oC Good to excellent 3,200~ 4,500 145,000~ 225,000 0.4~4 bottles, toys, bins, bushing LDPE 65~90oC Good to excellent 1,200~ 4,000 35,000~ 48,000 Not breakable bags, wrap, bottle, valve flange cover PBT 120~150oC Good to excellent 7,250~ 14,500 11,600~ 21,750 2.0~7.5 washer, rings, pistons, bearing, bushings, wheels, rollers PTFE 160~180oC Excellent 2,900~ 4,350 2,030~ 5,075 2.44~3.50 seals, gaskets, bearings, bushings in food process, industrial parts, medical device ABS 60~93oC Poor to fair 6,600 270,000~ 380,000 3.0~7.5 Parts in pipes, automotive body, keyboards. Nylon 93~177oC Good to excellent 6,000~ 24,000 390,000~ 1,100,000 2~8 Apparel, automotive, electrical parts, medical devices. PC 288~316oC Poor to fail 8,500 13,500 2~18 Electric parts, compact discs, telecom. hardware.
Crystalline materials: with a highly ordered molecular structure, where polymer chains arrange themselves into regular crystalline regions.
Achieving specific textures or finishes by applying an SPI or VDI finish on the molded part can will impact the costs of your tool. High polished or transparent finishes require both better quality steels and much more work to achieve than a standard polish. To keep costs down, only requests high quality finishes where necessary.
Plastic pellet resins used in injection molding can range from $1 per kg to $5 per kg or higher, depending on the type of material. Specialty materials, such as glass-filled polymers or elastomers used to achieve specific properties, will typically incur higher costs. To reduce costs, stick to readily available, easy to process material like PP or ABS as far as possible.
There are several things you can do to help lower the overall per part cost. The top tips to reduce the injection moulding per part costs include:
Factors such as resin grade, additives, fillers, and colorants also play a role in determining the material's behavior during the molding process.
1. High Efficiency: high-volume production of identical parts with minimal material waste, highly automated, fast cycle times and efficient production, minimal Post-Processing.
4. Parting Line and Flash: possible parting lines and flash, which may require additional trimming or finishing operations to remove.
The design of the mold and the quality of tooling are critical factors in achieving desired injection molding part. The mold design determines the part's shape, dimensions, surface finish, and intricacies, while the tooling quality influences the precision and consistency of the molding process. Key considerations include gating and venting design, cooling system efficiency, draft angles, wall thickness uniformity, and parting line location. Poorly designed molds or inadequate tooling can lead to defects such as warping, sink marks, flash, or short shots.
In addition, crystalline materials typically exhibit higher shrinkage upon cooling compared to amorphous materials. Therefore, adjustments in mold design and process parameters may be necessary to compensate for this shrinkage and prevent defects like warping or dimensional inaccuracies.
To get started, simply submit your 3D drawings and project details to our site submission form to get a free injection moulding quote or to speak with an expert from our engineering team.
The injection molding mold cost is also known as the tooling cost. Tooling refers to the design and manufacturing of the mold used to create injection-molded parts and is often the most expensive component of an injection molding project. Simple molds are typically in the $3,000 to $6,000 range while the price for larger, more complex, higher-production / steel moulds, or multi-cavity moulds can cost from $7,000 and up.
Bueno provides Injection Parts especially items in flow control industry such as Valve Parts, Plastic Ball, Filler Piston, Bushing, Washer, Flange Cover, Valve Body and other OEM custom services.
Several popular types of injection machine: two-plate direct pressure type, all-electric type, hydraulic injection type
BUENO can offer plastic engineering, injection molding parts, engineering plastic machining and rubber parts for injection molding.
5. Wide Range Application: a wide range of application both daily life products and specific industries, such as in medical, home appliance & household items, cosmetic packaging, Electronic enclosures, Agriculture.
2. Lead Time for Tooling: long lead time of the injection mold, several weeks to months, which may delay the start of production.
Once the initial costs of the molds are covered, the cost per unit during manufacturing is relatively low. Typically, you can expect the cost per part to range from $0.20 to $10.00 per piece or higher, depending on the quantity.
Size ØA±0.7 ØB+0.7-0.7 ØC±0.7 ØD±0.7 ØE Type 150LB 300LB 150LB 300LB 150LB 300LB 150LB 300LB 150LB 150LB 300LB 1/2" 40 40 16.5 16.5 60.5 66.5 17 19 A A 3/4" 47 47 16.5 19.5 70 82.5 18 21 A A 1" 52 56 16.5 19.5 79.5 89 19 21 A A 1-1/4" 66 16.5 89.5 20 A 1-1/2" 75 75.5 16.5 22.5 98.5 114.5 20 24.5 28.5 C A 2" 95 96 19.5 19.5 120.5 127 23 28 41.4 C A 2" 95.5 19.5 120.5 23 A 2-1/2" 108 105 19 22 139.5 149 27 26.5 52.8 D B 3" 128 131 19 22 152.5 168 29 38 67.3 D A 4" 162 162 19 22 190.5 200 29 44 85 D A 5" 188 22 216 28.5 B A 6" 220 216 22 22 241.5 270 31 38.5 144.7 C A 8" 276 271 23 24 298.5 330 30 44.5 182.7 C B 10" 328 25.5 362 39.7 229.5 D 12" 381 25.5 432 38.6 B
Estimate the cost of your injection molding project with us. HLH Rapid has over 20 years of experience in building custom tools and plastic injection moulded parts for engineers and industrial designers in a wide range of industries from automotive, medical, electronic devices and more. We can build low-cost and high quality tools from a wide range of material grades and well designed tools.
Any additional processes such as assembly, post-molding treatments, or finishing, will increase the unit cost. To keep molding costs and time and down, if it can be done in the tool itself, you should work with your supplier to try and achieve it that way.
So, how much can you expect injection molding to cost? Injection molding projects can cost anywhere from $10,000 or less to $100,000. The total cost of injection molding quote is essentially made up of two parts: mould cost + part cost.
Cycle time or injection moulding time includes setup and running time for each part, this is where the manufacturer’s overheads are. More intricate designs, parts with complex features or larger parts may slow down the time it takes to remove the part from the mold, increasing overall cycle time and costs. Keep in mind that a high-viscosity will require longer injection and cooling time.
3. Design Flexibility: a high design flexibility, parts with as complex shapes, undercuts, and fine details, enabling engineers to optimize part designs for functionality, performance, and manufacturability.
The most common materials used to make molds are steel and aluminum, with steel lasting longer. While it’s often said that aluminum costs less, this is not always the case. High-quality but low-cost Chinese steel grades, such as S50C and P20, suitable for rapid tooling and low-volume production purposes, can serve as cheaper alternatives to aluminium.
2. Consistency and Precision: tight tolerances and high repeatability, ensuring consistent quality across large production runs.
Quantity of parts required will impact two fold, first in the tool design itself. If you are looking at very high numbers of parts it might make sense to go with multi-cavity tools, which are larger and more expensive but will bring part costs down. Also the higher the quantity required the better the steel used to machine the cavity, core and inserts will need to be. Low quantities can often be realized using low grade steels or aluminiums’ bringing costs down.
GETTING A QUOTE WITH LK-MOULD IS FREE AND SIMPLE.
FIND MORE OF OUR SERVICES:
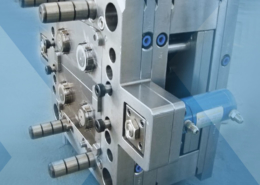
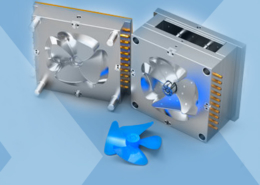
Plastic Molding

Rapid Prototyping
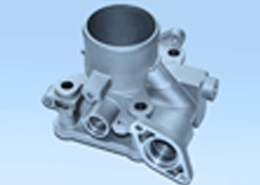
Pressure Die Casting
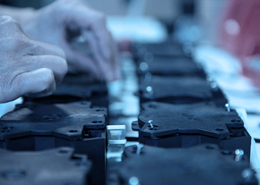
Parts Assembly
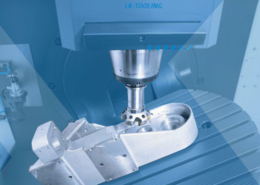