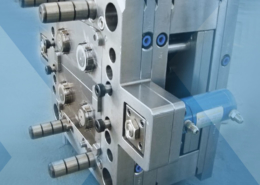
Exploring Thermolator Injection Molding - thermolator injection molding
Author:gly Date: 2024-10-15
Keeping the cleanroom environment free from contaminants requires precise control of the area's airflow, temperature, and humidity and strict cleaning procedures for the people, equipment, and materials that pass in and out of the cleanroom.
Our external audits have always confirmed our high-quality standards. An external certified professional verifies our airflow, filter flow, and bioburdens. We are ISO 14644 certified, and our cleanrooms are suited for manufacturing various types of medical devices.
Additionally, standards significantly drive the cleanroom technology and processes needed in medical device manufacturing. Most medical device manufacturing must be conducted in a cleanroom between Class 100,000 (ISO 8) and Class 100 (ISO 5).
Our cleanroom facilities are ideal for testing, developing, and assembling highly sensitive parts and products. These parts are made from materials engineered to deliver very specific physical and chemical characteristics.
Our quality management systems ensure our customer’s requirements are always exceeded. Developing processes and procedures aimed at continuously improving operations and meeting the never ending demands of the manufacturing sector.
Spectrum designed the cleanroom to manage the unique challenges of cleanroom molding and workflow. Real-time data capture, process quality monitoring, and in-cavity pressure monitoring are components of this cleanroom’s ultra-modern digital technology framework.
The building of a custom plastic mould requires great precision using design software and metal working equipment such as CNC milling stations, EDM machines etc. Custom Plastic Mould costs vary depending on:
A cleanroom is a controlled environment where technicians use equipment and gear to minimize and eliminate pollutants such as dust, microbes, and other airborne particles.
Custom Plastic Injection moulding is the preferred manufacturing process when you need to produce amounts of the same plastic part. The process involves heating up small plastic granules, usually to a liquid state and then injecting it under pressure into the cavity of a mould. After you have finalised the custom design of the plastic part you want to make, the first step in getting the part injection moulded is to build the mould.
Our injection-molded solutions include premium, high-quality components and fully assembled medical devices. We have years of experience with complex molding projects working with highly engineered performance medical plastics.
Not all parts require cleanroom injection molding. We also offer injection molding services for lower-risk applications that require a controlled environment but no certification. Do you have any questions about our cleanroom and injection molding services? Contact us for more information.
No components are too difficult at Allmould Plastics, with an extensive range of injection moulding machines of all different sizes and tonnages there is no project we can’t look into.
Our machine capacity dynamically adapts to various requirements. Our ability to process all plastics is further highlighted through a specialised focus on engineering plastics. At Allmould Plastics our purpose built facility is equipped with the latest machines, automation and robotics, to ensure a lean manufacturing process of optimal production efficiency.
At Allmould Plastics we have the latest technology robotic Automation. Above are medical parts that have been removed from the injection moulding machine. Once these parts have been taken from the mould they go through a series of QA checks before being placed in the correct packaging for dispatch.
The work area and personnel within the Minneapolis cleanroom conform to environmental control standards through the use of:
Many medical devices come into contact with or are inserted into the human body. Therefore, manufacturers must utilize the highest standards of precision and cleanliness when producing medical device products to ensure the safety of patients.
Cleanrooms are classified into different levels, depending on the “allowable” amount of particles (contaminants) in the space. This is conveyed as the number of particles per cubic meter.
As an Australian Manufacturer for over 25 years, Allmould Plastics have the expertise and the facility to take your project from initial idea right through to finished product. Offering the most innovative rapid prototyping and plastic injection moulding in Australia.
Our team believes in 100% safe working environment and procedures. We offer clean room facilities and a purpose built injection moulding workshop. We can assure you we can achieve great results and complete customer satisfaction.
Medical injection molding is typically conducted in an ISO Class 8 cleanroom. An ISO 8 cleanroom provides air quality levels with an allowable maximum of 100,000 particles (≥0.5 um) per cubic foot of interior air with a minimum of 20 air exchanges per hour.
Take a virtual tour at Spectrum Minneapolis. Imagine your next complex, tight-tolerance injection molding, and assembly project becoming a reality with the help of our expert engineers and manufacturing teams.
From your initial thoughts on a part through to full scale production Allmould Plastics can take you down the right pathway. As seen in the image a client’s initial thought was then designed by our R&D team, drawn, prototyped, mould designed and finally manufactured in masses.
Allmould Plastics are extremely passionate about bringing a company or a person’s dream into a reality. Please do not hesitate to contact our helpful team if you have any question or would like a quote.
Above is an injection mould Allmould Plastics made to produce plastic bottle preforms. Countless hours are poured into the design of these types of moulds from our Engineers to guarantee maximum production along with short cycle times.
Cleanroom molding is vital for industries where precision, cleanliness, and contamination control are paramount. It helps companies meet regulatory standards, produce high-quality, reliable products, and maintain the integrity of sensitive materials. This specialized manufacturing process plays a crucial role in ensuring the safety, functionality, and quality of products in various high-stakes industries.
GETTING A QUOTE WITH LK-MOULD IS FREE AND SIMPLE.
FIND MORE OF OUR SERVICES:
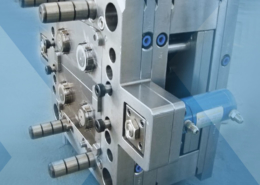
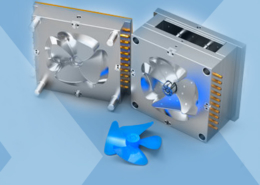
Plastic Molding

Rapid Prototyping
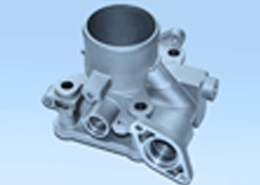
Pressure Die Casting
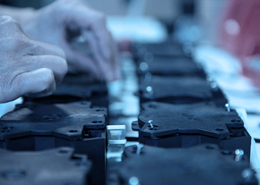
Parts Assembly
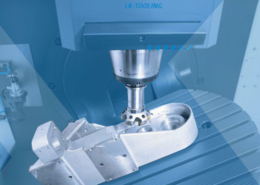