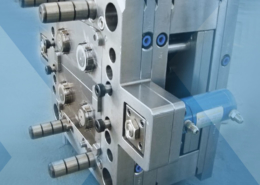
Extrusion and injection moulding grade LDPE Granules - ldpe injection molding
Author:gly Date: 2024-10-15
Lining: Generally, PTFE and PFPE (written as F4 and F46) plastic are lined with ferrous metal pipes and pipe fittings, which can be used for chemical anticorrosion and corrosion-resistant materials.
PTFE resin → Mashed and sieved → Die-pressed moulding → Sintering and shaping → Tube outer circle turning → Inspection → Surface activation treatment → FRP → Flange mounting → Flange wrapping → solidification → Flange head-turning → Core removal → Mounting gasket → Flanging → Finished
PFA has a very low hygroscopicity of 0.03%, so it does not need to be dried. Before injection, the insert should be preheated to about 140 ° C. The three-stage temperature of the injection barrel is 200-210, 300-310, 350-410 ° C The nozzle temperature is slightly lower than the higher temperature of the barrel, the mould temperature is 140-230 ℃, the injection pressure is 40-90 MPa, the injection speed should be slightly slower, and the load holding time should not be too long. The cooling time is 40-150 seconds.
Chen Hsong Propels Plastic Industry Forward and Receives Minister’s Acknowledgment at Second Technology Conference in Mumbai, India
Compression moulding is divided into three steps: preforming, sintering and cooling. Preforming is to add PTFE powder into the mould evenly and pressurize it at room temperature to form a dense perform (i.e., blank); sintering is to heat the preform above the melting point, and cooling is the process of reducing the sintering temperature to room temperature.
Teflon PTFE plastic raw material processing is roughly divided into four types: compression moulding, roll moulding, injection moulding, and secondary processing.
The Chen Hsong Group has offices and distributors all around the globe. Select your region from below or search our global list of distributors.
Welding: There are two types: hot-press welding and hot-air welding. For hot-press welding, it must be heated to above 327 ° C in special pliers, and it can be welded under pressure.
The raw material is polymerized by suspension method, and the soft and fine powder with a particle size of 20-500 microns is preferred. During the pressing process, it is necessary to "deflate", the preforming pressure is 17-35 MPa, and the holding time depends on the thickness of the blank. For example, a 100 mm thick blank should be held for 15 minutes.
One-way rolling is to reheat the transparent film and quickly process it through two equally rotating rollers of the calendar. Rolling magnification is controlled in the range of 1.5-2.5; the general roller speed is 20 rpm.
Such as PTFE machine tool guide soft belt: use suspension PTFE fine particles, after crushing, pass 20 mesh sieve, bronze powder or aluminium powder particle size is 200 mesh, hold pressure for 100 mm high rough for 5 minutes, deflate three times in the middle, sinter The heating rate is 50-60 ℃ / hour, the temperature is kept at 320 ℃ for 1 hour, and the temperature is reduced to 150 ℃. Before turning the blank, it should be preheated to 80 ° C, and then kept for one hour after heat preservation. The soft tape should be treated with sodium naphthalene. Among them, 51 g of naphthalene, 100 ml of tetrahydrofuran, an appropriate amount of sodium metal, and a soft tape with a thickness of less than 1 mm in the sodium naphthalene treatment solution for 1-3 minutes, and then washed with hot water at 90 ° C.
Ms. Lai Yuen CHIANG, Chairman and CEO of Chen Hsong Earns “GBA Outstanding Women Entrepreneur Award – Supreme Honorable Winner 2023” Title
When moulding, attention should be paid to the impact of compression ratio (generally PTFE is 4-6) and moulding shrinkage rate (usually PTFE is 2.6-4.5%) on the product.
Chen Hsong Propels Plastic Industry Forward and Receives Minister’s Acknowledgment at Second Technology Conference in Mumbai, India
For example, PTFE can be blended into polyphenylene, polyimide, polyparaben, filled with graphite, molybdenum disulphide, bronze powder, etc. can be used on hydraulic gates, fluoroplastic 46 can be used on corrosion-resistant ball valves. The moulding temperature is 320-350 ℃, the moulding pressure is 3-30 MPa, and the setting temperature is 120-150 ℃.
The varieties of fluoroplastics are developed into fluorinated epoxy resins (for optical communication systems). Perfluoro elastomers (for semiconducting devices), thermoplastic fluoroelastomers (for medical treatment, cable coating). And perfluoro polymers Ether (for high and low-temperature grease). There are also solvent-free processing of polyvinyl fluoride, only need to add nine parts of lubricants, four parts of heat stabilizers, two pieces of other additives can be processed. TRUNNANO (Luoyang Trunnano Tech Co., Ltd ) is a professional new nano material manufacturer with over 12 years experience in chemical products research and development. If you are looking for high quality new nano material, please feel free to contact us and send an inquiry.
PFA (copolymer of tetrafluoroethylene and perfluoroalkyl vinyl ether) that is, meltable PTFE can be injection moulded. Its processing temperature is comprehensive, up to 425 ℃, its decomposition temperature is above 450 ℃, generally control the processing temperature range is 330-410 ℃.
Cutting: Similar to the metal cutting method, the equipment includes lathes, drilling machines, planers, etc. Note that the new body must be placed for 24 hours before cutting.
Multi-directional rolling is a moulding method in which the sintered and quenched film is placed on a calendar to perform multi-directional rolling and gradually reduce the film thickness. The rolling ratio is in the range of 2-2.5. The temperature of the drum should be controlled at 150-200 ° C. When the steam is heated, the steam pressure is 0.5-0.9 MPa. The rolling ratio is an important parameter, too large and too small are not suitable for the product. Sometimes it is necessary to repeat rolling several times to press a product.
Drain BasketJuly 25, 2022Air conditioning components: Panels,frames, wind bladesMarch 11, 2022Plastic Helmet VisorMarch 11, 2022Stationary Bicycle Belt Drive CoverJanuary 25, 2022
For example, the tube blank of F46 heat-shrinkable tube is prepared by water-cooled vacuum setting method, the drawing ratio of the machine is 3-7, the length of the melting cone is controlled at 10-20 mm, the temperature of the inflation die is 80-160 ° C, and the inflation pressure is 0.1- 0.2 MPa, linear traction speed 80-500 mm / min. There are also blown F4 spiral tubes.
For cooling, slow cooling is generally used at a speed of 15-25 ° C / hour. In exceptional cases, such as a few thin plates with a thickness of less than 5 mm or push-moulded thin-walled tubes, rapid cooling is used.
Ms. Lai Yuen CHIANG, Chairman and CEO of Chen Hsong Earns “GBA Outstanding Women Entrepreneur Award – Supreme Honorable Winner 2023” Title
Attention should be paid to sintering: the heating rate can be 20-120 ℃ / hour. The larger the product, the slower the heating rate. The suspension resin sintering temperature is higher, 370-380 ℃, while the dispersion resin sintering temperature is lower, 360- At 370 ℃, the sintering temperature is high, and the shrinkage and porosity increase accordingly. The sintering time should be adequately controlled.
Ms. Lai Yuen CHIANG, Chairman and CEO of Chen Hsong Earns “GBA Outstanding Women Entrepreneur Award – Supreme Honorable Winner 2023” Title
The PTFE diaphragm is roll-formed. Roll forming can be divided into two processes: unidirectional rolling and multi-directional rolling. After rolling, the PTFE diaphragm changes from the original opaque colour to a translucent crystal colour.
Such as polyvinylidene fluoride sealing ring: add 1 part of the acid absorber, mix ball mill for 24 hours, in the press with template temperature of 195-250 ℃, slowly pressurize to 2.5-3.5 MPa, deflate 1-2 times in the middle, When the mould temperature rises to 180-190 ° C, it is quickly moved to a cold press to cool under 14 MPa pressure. It is taken out at 50 ° C, trimmed to remove burrs, and then put into a 130 ° C oven. After heat treatment for 24 hours, the packaging can be inspected.
Ms. Lai Yuen CHIANG, Chairman and CEO of Chen Hsong Earns “GBA Outstanding Women Entrepreneur Award – Supreme Honorable Winner 2023” Title
New Energy – New Generation! Chen Hsong Group signs strategic cooperation agreement with Chinese electric vehicle manufacturer BYD
Fluorine plastic moulding can process plates, rods, sleeves, tapes, sealing rings, diaphragms and parts with metal inserts.
The glass fibre reinforced PTFE pipe is used as the inner liner of the steel pipe to solve the corrosion problem of the pipeline. The technological process is as follows:
Some fluoroplastics are pressurized at a time above the melting point temperature. This moulding die is called a hot compression die, and the corresponding PTFE die is called a cold compression die.
Due to the processing characteristics of the fluoroplastics, some products are difficult to form at one time, and they must be processed twice to obtain usable finished products. Secondary processing techniques include cutting, welding, lining, inflation, etc.
Otima Veggie TraySeptember 30, 2022Washing Machine BalancerSeptember 30, 2022Plants POTSeptember 29, 2022Silicone LampJuly 25, 2022
Inflation: The products are bellows, shrinkable heat tube, heat-shrinkable film, etc. It is divided into continuous inflation and intermittent inflation.
GETTING A QUOTE WITH LK-MOULD IS FREE AND SIMPLE.
FIND MORE OF OUR SERVICES:
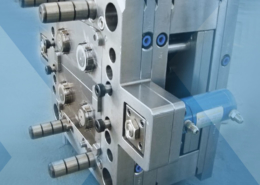
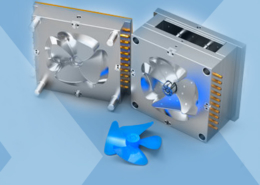
Plastic Molding

Rapid Prototyping
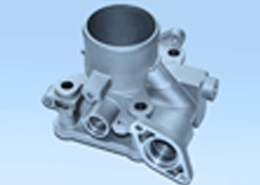
Pressure Die Casting
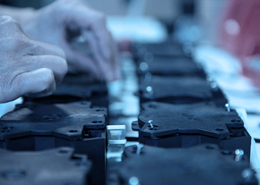
Parts Assembly
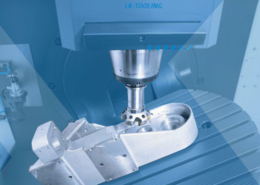