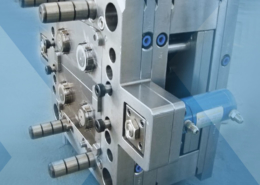
Compared Hard and Soft Tooling for Injection Molding ... - soft tooling for inje
Author:gly Date: 2024-10-15
Today, structural foam molding is a highly evolved technique that can create lighter, stronger, and more resilient plastic parts than traditional injection molded parts. In this article, we discuss the structural foam molding technique in-depth, its design considerations, and key differences with traditional injection molding techniques.
RapidDirect, for example, now combines the latest Big Data analytics, software, and hardware to enable Industry 4.0 integration. This way, there is a guarantee for innovative approaches and best practices. It, in turn, results in smarter production and ensures the cost-efficiency of low-volume plastic parts production.
If you want to produce high-quality machined parts with a sleek appearance, it’s essential to consider some critical factors related to CNC machining.
This practice significantly increases mold manufacturing costs and lead times. A more cost-effective finish is an as-milled surface that probably shows some tool marks. The two other options available involve the use of 600 gritstone or bead blasting textured finish. The chosen finish must be compatible with the part’s function.
Ejection of low volume plastic parts can be manual or via the use of ejector pins. In the latter, the clamping plate moves backward and the mold halves open. Afterward, the ejector pins push out the final part.
Machining of aluminum molds occurs using end mills. Therefore, sharp internal corners may be a concern. Sharp corners on injection molded parts often create stress and compromise a part’s integrity. As such, it will be best to use vertexes or rounded edges (radii) for plastic part design. This will ensure a more substantial product and improved moldability.
Structural foam molding is a type of manufacturing process in which, the packing stage involves mixing the molten resin with a blowing agent to create thermoplastic foam. The chemical blowing agent is subjected to heat and it works by creating a microcellular structure to expand the material and form the part against the mold.
It will be best to go for a company that can offer low-volume but high-quality injection molded products without compromising the specification. This means that the low volume injection molding company must fully comply with the design specification. Recommendations are allowed based on experience, knowledge, and expertise. You must approve every adjustment to the design.
Structural foam molding techniques can manufacture thick-walled parts and intricately detailed parts without causing any depressions or sink marks and it is thus more efficient than traditional injection molding techniques. In addition, the low-pressure injection process of structural molding reduces stress and plastic warpage issues.
Most engineers and designers prefer 3D printing for quick iterations during plastic product production. 3D-printed parts often come with layered surfaces. However, the surfaces can be easily sanded and painted for the desired surface finish.
You should note that in structural foam molding, the part walls must be thicker as thin walls can deter the required reaction to create the cellular structure.
You should note that although Aluminum molds are cost-effective, however; they aren’t long-lasting, especially when subjected to the high pressures of traditional injection molding techniques.
The rise of various advanced technologies continues to evolve the manufacturing space. In so doing, there is an increased potential to eliminate quoting delays and improve prototype manufacturing techniques. The visibility of orders within the supply chain becomes a lot more straightforward. Also, customers can manage their orders from anywhere via a convenient platform.
Low volume production involves manufacturing smaller quantities in the small run. Therefore, there will not be any major impact if a company decides to modify or alter the design. That way, the product can be perfect before it gets to the consumer.
Low volume injection molding is an efficient process for high-quality manufacturing. However, finding the best plastic injection molding services provider could be challenging. Here are a few factors to consider before choosing a plastic molding company:
While we cannot do foam molding, you can still reach out to us to have a look at your part. In many assemblies, there are parts that can be manufactured by injection molding, which is our core competency for decades.
A quality plastic injection molding process provides immediate feedback to help improve manufacturability. It enables the testing of new concepts in various industries before the mass production of parts.
Structural foam molding is a low-pressure injection molding process which is why aluminum molds are suitable and can be used for this technique. In addition, structural foam injection molding can incorporate other types of materials such as metal and wood.
From its name, on demand allows businesses to make parts based on demand. As a result, there is less need for large inventories leading to lower storage costs. Furthermore, it becomes easier to adapt to fluctuations in demand which makes low volume plastic injection molding suitable for businesses that operate in unpredictable industries.
Small batches do not require the hardened steel mold tooling typical of the traditional molding method. Rather, it uses the softer aluminum material for making the molds. Aluminum is a considerably softer material than steel. Thus, aluminum molds are easier and faster to work with.
Aluminum has a better heat transfer rate than steel which reduces the complexity in positioning the cooling lines. Furthermore, it makes more room for more mold components. As a result, the low volume plastic manufacturing process ensures better design flexibility, closing the gap between prototyping and high-volume production.
You must opt for an injection molding partner that offers a wide range of prototyping services. These include mold flow analysis, responsive manufacturing, and part design. Offering other manufacturing services such as CNC machining and injection molding will be a quality addition. Such companies will understand your requirements better and tackle production problems early.
One of the most common mistakes you can make with plastic injection molding is choosing a better surface finish than necessary. This may badly impact the product’s functions. For example, very smooth surface finishes require hand-polishing of mold cavity surfaces. The polishing may be done with diamond buff up to 2 Ra.
Only thermoplastics can be used to manufacture plastic parts via the structural foam molding technique and thus, this technique is extremely limited to the type of materials that can be used for manufacturing.
3D printing is a quality-focused manufacturing process considered an alternative to quick turn molding by many product designers and manufacturers. It does not require upfront investment into mold creation and has a short lead time.
Furthermore, aluminum tooling allows for easier heat treatment because there is no need for the extra annealing step. This is unlike steel which needs annealing to reduce any internal stress and to toughen the metal sufficiently. Moreover, aluminum molds support most surface treatments that you would normally use for steel.
The parts manufactured via structural foam techniques aren’t as dense as similar parts that are manufactured using other processes and are thus lighter. The finished part manufactured via structural foam molding is typically 10 – 40% lighter than an equivalent solid part.
We boast of a fast turnaround on our low-volume plastic injection molding services without compromising on quality. Choosing RapidDirect would mean that you get quality prototypes with short lead times and budget-friendly prices. Upload your design file, and let us offer you our best services.
The extremely high level of precision needed within the aerospace industry makes CNC machining a suitable manufacturing process for the sector.
In structural foam molding, bosses are frequently used to insert and attach fasteners to assemble multiple structural foams, and ribs are commonly used to increase part rigidity and load-bearing capability. Ribs are also incorporated instead of increasing wall thickness.
This pattern helps in creating a urethane mold and pouring suitable resin into the mold will allow the manufacture of several copies of the product. A urethane mold can last for up to 20 runs and is a cost-effective option that allows product designers to test design requirements and gather feedback early.
You should note that there is a higher resistance in wall sections that are less than 0.250” / 6.35 mm however; this can be compensated with increased injection pressure.
The honeycomb structure that is created during the structural foam molding process enables a very high strength-to-weight ratio as compared to the parts manufactured via traditional injection molding techniques.
The rapid manufacturing industry is in a massive transition state and with low volume injection molding, plastic part manufacturers can easily cater to the market needs as the process allows you to create a small quantity of plastic parts with consistent characteristics and qualities.
A good on-demand injection molding company for producing a small batch of plastic parts must adhere to the best standards of efficiency and quality. The machines should work with the latest technologies with high-quality project management software for better communication.
After you inject molten material into the plastic injection mold, the molten plastic cools and solidifies. The cooling/solidification time depends on the type of mold taking longer to cool due to a slower thermal transfer occurring in plastic than metal. In such a case, cooling is improved by using compressed air or interchangeable stacks.
A structural foam is a type of composite material that is created when a polymer combines an inert physical gas, such as nitrogen, or a chemical blowing agent during the molding process. It has a low-density, cellular network at its core and is combined with a high-density solid skin. The cellular core decreases the overall weight while the solid surface enables the part to stay strong and impact resistant.
This is a low-pressure injection molding process and the intended aim is to reduce the density and thus, the weight of the finished part.
Standardization and quality are part of our companies core values. We deliver the best possible experience and product to our customers, every single time consistent. Take a look at our certificates!
This technique involves low temperatures and pressures leading to the use of inexpensive materials. Furthermore, surface finish is important because the product may pick up some details of the mold. Generally, manufacturers limit thermoforming to manufacturing relatively simple components like packaging trays, vehicle door panels, etc.
Injection molding is a cost-effective solution for mass-production technique but with low volume plastic molding, small and medium-scale businesses can produce small quantities of plastic parts. This leads to faster market entry, better product quality control, shorter lead time, etc. This article talks about everything you need to know about small run injection molding so you can make a better-informed decision.
Incorporating draft angles leads to the production of low volume plastic parts with tapered edges. As a result, there is less friction during demolding, which prevents mold/part damage, and easier part removal. A good rule of thumb in injection molding is adding a draft angle of 1 to 2 degrees.
This depends on the type of machine but involves the transfer of the molten plastic to the injection barrel and subsequent injection to the mold.
On-demand low volume manufacturing is a relatively new concept in the manufacturing world. It brings about several dramatic changes to how engineers interact with suppliers and manufacturers. This is even more so when it comes to custom plastic fabrication.
These thermoplastic resins come in different additive fillers, color options, and properties such as strength, thermal and chemical resistance, durability, etc.
It is also applicable to make a small batch of a part providing an economical solution, especially for businesses without enough capital for large-scale production. It incurs lesser costs unlike traditional injection molding and supports small run production allowing businesses can respond quickly to changing market demands.
The whole low volume injection molding process translates to a shorter lead time. In mold design, the use of aluminum known for its soft nature makes the mold manufacturing process easier and quicker.
Traditional manufacturing involved the mass production of large-scale similar products. However, on-demand manufacturing enables low-volume, customized products such as small-scale plastic injection molding. It takes advantage of cloud-based technologies and self-service models. This allows customers to get quotes in real-time and keep tabs on their orders throughout manufacture.
The first step is the identification of the final plastic parts specifications and choosing the right materials. This will aid in the design of the mold. Metals are suitable for making injection molds with aluminum being the most popular.
This technique can be used to manufacture parts that have a certain range of wall thicknesses, and thus, is again limited to only certain types of parts.
Low-volume injection molding is a cost-effective manufacturing solution for small and medium-scale businesses. Key applications of the manufacturing solution include:
At VEM-Tooling, we have an experienced team of design experts and engineers who can help you choose the right solution for your project!
Just like any manufacturing technique, engineers must consider the design criteria early on in the process to manufacture parts efficiently via structural foam molding. Let’s understand the various design considerations for structural foam molding:
Parts that are manufactured via the structural foam molding technique are lightweight, strong, and durable. Structural foam molding may be the right design choice if you’re seeking to manufacture a lower-weight high-strength part.
It is the perfect method for prototyping plastic parts. It offers benefits such as quick and cost-effective production, easier testing, and validation of designs before mass production tooling, and easier refinement.
Despite being one of the oldest manufacturing methods, CNC machining remains a reliable small quantity plastic manufacturing method. It is versatile and can work with other types of materials including metals. Furthermore, it helps to create accurate molds, patterns or dies for various manufacturing processes such as molding, casting, and others.
Wall thickness is crucial in rapid injection molding. Walls should not be thicker than the recommended range for plastic families. When not considered, such walls may sink, warp, or experience other molding defects. The general rule of thumb is to use a wall thickness between 0.04 to 0.14 inches consistently across the whole part.
As the cooling occurs, a honeycomb structure develops to form the interiors whereas a solid skin is formed against the mold. The honeycomb structure of the interiors has various advantages such as preventing shrinkage and reducing product weight without compromising structural integrity.
Draft angles are necessary design considerations in structural foam molding and since lower pressures are applied in this technique, the draft angles can be smaller. You should however; note that higher cavity pressures make it difficult to release the part from the mold which is why the draft angle should be larger if the wall thickness is thin.
Injection molding is carried out in two stages. The first stage is an injection stage, where the molten resin is injected into a mold, and the second stage is the packing stage, where pressure is built and the molten resin takes the mold shape to form the plastic part. In structural foam molding, the injection stage is similar to the traditional injection molding technique, however in the latter stage, the resin is mixed with a blowing agent that is activated by the molten resin’s heat. At this stage, the blowing agent expands the resin and creates a cellular foamed structure which takes the mold shape and forms the part.
Despite using a softer tooling material, low volume plastic injection molding produces highly durable and functional parts
Structural foam molding is a type of manufacturing technique that has a unique approach and distinct advantages. It is a popular technique to create stronger, more rigid plastic parts and the means to reduce potential part weight for larger parts.
Components such as an ejector system are installed into the mold before being loaded on an injection molding machine. The engineer then configures the machine temperature, pressure, and injection speed and conducts a test run to check the production run quality.
Since the injection mold gets to the manufacturing facility a lot quicker, and it involves low production volume, production is fast. In many cases, this significantly accelerates time to market, making this technique beneficial for both small and large product teams.
If you wish to form multiple identical parts in a single shot, then a multi-cavity mold will be useful. It helps to produce two or more designs with tiny iterations at the same time. This enables the quick testing of different product designs simultaneously. Whenever there is a need for quantities beyond initial samples, they also serve as good options. At the same time, they can also help to reduce costs per unit.
The parts that are manufactured via structural foam molding have improved electrical insulation characteristics and better heat insulation as the cellular core of structural foam parts demonstrates excellent insulation properties, thus, making this technique apt for parts that require thermal or acoustic insulation.
The wall thickness in structural foam molding can be as low as 0.180” / 4.5 mm, and up to 0.500” / 12.7 mm or thicker. The optimal thickness of wall sections should be 0.250” / 6.35 mm.
RapidDirect is your number-one low-volume injection molding partner. We effectively combine our experience, expertise, and powerful facilities to get your plastic parts from production to market within a short time. Our rapid quotation system uses the latest technologies to give you quotes within seconds.
Structural foam molding is more economical than injection molding and other techniques. Since this technique can incorporate Aluminium molds instead of Steel molds, it gives the technique an edge in being cost-effective. The low pressure and clamping forces in this technique minimize the wear and tear. In addition, if Aluminum molds are maintained well, then their lifespan can be lengthened.
Since the structural foam molding process uses a blowing agent, it restricts the manufacturing of various part types and thus, has limited design flexibility.
If a company plans to have a mass-produced product, low volume injection plastic molding is the way to start. It helps to bridge the production gap between prototyping and production. This method brings a feasible prototype to production in a quick turn without requiring too much commitment. It also helps to fine-tune the product and the process.
Quality control involves inspecting low-volume plastic parts for any defect and ensuring they meet quality standards. Afterward, trim the molded parts and use secondary surface finishing operations.
Structural foam molding is also a competitive technique in terms of cycle times when compared to injection molding and other techniques thus, making this technique a cost-effective as well as time-saving process.
Urethane casting is an excellent alternative characterized by no upfront cost and reduced lead time. The manufacturing process involves creating a master pattern of the product with high-resolution 3D printing or CNC machining.
Low volume plastic injection molding offers several advantages that make it the manufacturing choice for several plastic parts over the traditional injection molding process. Here are some of its advantages.
Since the base is a cellular network and not a solid structure, the base material that is typically used to create a structural foam is a thermoplastic polymer rather than a thermoset. Some of the most commonly used thermoplastics in structural foam molding are polyurethane, polycarbonate, polyphenylene oxide, and acrylonitrile butadiene styrene.
With on-demand manufacturing, customers can order precise small series injection molding parts. The quantity on order will satisfy immediate production requirements. This will address several pain points regarding lead time, communication, design for manufacturability (DFM), and cost. With digital technology becoming central to the industry, on-demand manufacturing is leading a decent revolution.
An important step in low volume injection molding is the right selection of material among the several commercial-grade plastic materials available for manufacturing.
This involves using 3D printing to create a prototype of injection molds also known as 3D printed molds. Engineers can make use of the mold normally after checking for flaws in design and functionality and correcting the errors. The mold is then improved using manufacturing processes such as 3D printing or CNC machining.
Manufacturers need to understand this type of injection molding to gain an advantage in the evolving markets. As a result, this extensive guide takes you through everything you need to know about low volume injection molding.
The parts that are manufactured via the structural foam molding technique are much more impact-resistant and can be applied to manufacture large parts due to lower pressure and in metal-to-plastic replacement.
There are various other low volume plastic manufacturing methods aside from injection molding. Below are some of the alternatives you can choose for cost-effectiveness and faster time to market.
Structural foam molding also allows greater flexibility in terms of resin selection since even commodity resins can be used in this technique, thus enabling manufacturers to lean towards cost-effective resins if possible.
The first step in narrowing down your choice is to use the company’s volume capacity and specialization. Companies capable of low to moderate production (pars under 10,000) are advised. This is because they can offer prototypes quickly enough for testing.
Your choice of material depends on the intended application of the low volume plastic parts and their operating environment.
In the structural foam molding process, two components are stored in separate containers in liquid form which are then mixed to form a resin. This resin mix is injected into a pre-prepared mold which is then cured via chemical reaction. In this process, lesser quantities of the resin mix are used so that the resin itself does not fill the mold.
The blowing agent in this process is activated by the reaction between the two components and it further expands to fill the surplus space of the mold with foam which creates the honeycomb texture in the center. The surface cells collapse as they come in contact with the mold wall thereby creating a solid or rigid surface.
CNC machining is a costlier alternative but is suitable for quick production runs. In some cases, a CNC machining technique such as CNC milling is combined with other processes like 3D printing for effective production or achieving tighter tolerances.
This involves using a clamping system that can generate a clamping force that holds the mold in place, closing the gap between the mold halves. The clamping force should be equal to the injection force to prevent disruptive movement and should be lower in 3D printed injection molds that are protected by a metal frame.
Low volume plastic molding allows manufacturers to make parts without demanding minimum orders. Therefore, if you are looking to get small batch plastic manufacturing, this can be helpful. You will also avoid getting products from an outdated inventory. All of these translate to effective cost-saving.
The process of structural foam molding primarily involves the addition of a blowing agent and the modification of process parameters to create a sandwich construction. This particular construction is solid on the outer layers and has a foam core center.
Thermoforming is another alternative that involves creating molds over which there is the heating of a thin sheet of plastic formed using mechanical force, pressure, or vacuum which takes the mold’s shape with extra material being trimmed off.
Traditional injection molding techniques are extremely expansive and inclusive to various project requirements however; structural foam molding techniques pose certain advantages w.r.t design and operational requirements. Let’s understand when should you choose structural foam molding over traditional injection molding techniques:
If varying wall thicknesses are needed, then transitions from thick to thin should be tapered with radii and fillets. It is recommended to include a gate in the thinner section and let the material flow into the thicker sections.
GETTING A QUOTE WITH LK-MOULD IS FREE AND SIMPLE.
FIND MORE OF OUR SERVICES:
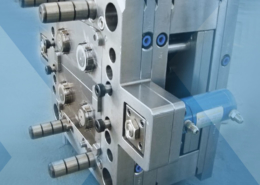
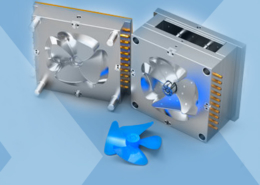
Plastic Molding

Rapid Prototyping
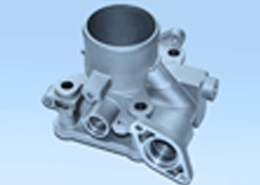
Pressure Die Casting
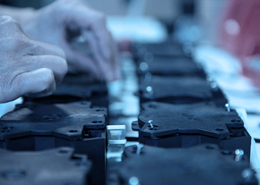
Parts Assembly
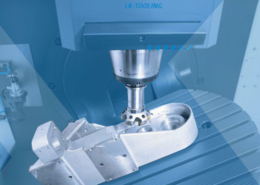