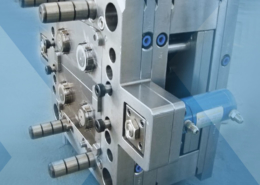
Comparing Plastic Injection Molding And Extrusion Molding - injection extrusion
Author:gly Date: 2024-10-15
This document discusses different molding processes including structural foam molding, sandwich molding, and their advantages and disadvantages. Structural foam molding is a low pressure injection molding process where gas is introduced into molten polymer to reduce density and weight. It requires less pressure than other molding processes. Sandwich molding involves injecting two or more polymers one after another through the same gate to form a layered part with different materials for the core and skin. This allows for weight reduction and various material combinations. Advantages of these processes include lower costs, weight reduction, design flexibility, and strength to weight ratios. Disadvantages include potential for air bubbles or shrinkage.Read less
We can provide advice and quotes on anything - from an idea or simple sketch to complex 3D CAD models. Give us a call today!
We have experience working with a range of different polymers and have in stock a variety of thermoplastics suiting the needs of our clients - from basic, commonly used polymers all the way to specialised engineering grades.
Plastic injection moulding involves heating plastic pellets under a high temperature and pressure to form molten plastic. The molten plastic is then pushed through a nozzle into a die (the injection moulding tool) which contains the pattern for the part being manufactured. The plastic then cools and the part is ejected from the die, before the process repeats again with an empty die cavity.
Plastic injection moulding is a high volume manufacturing method capable of producing multiple complex parts in a single cycle. Injection moulding allows for:
From the wide variety of industries we serve ranging from mining, automotive, construction and aerospace to consumer goods, we have experience using a range of injection moulding polymers including virgin polymers, reprocessed polymers and polymers with material additives such as UV inhibitors, flame retardants and glass fibers.
At Afaridan Plastics, our culture of innovation and continuous improvement means that your product will be delivered successfully - at low cost, high precision and at the fastest turnaround time. We understand how injection methods, flow rates, cooling times, material types and mould design can affect your finished product. Our engineering team will work with you to identify the optimum part design based on the variables at play in the injection moulding process.
Plastic injection moulding requires hardly any work after ejection, as the process produces a good surface finish. The process generates little waste, as scrap plastic can be reground and re-used.
Our system and process can provide full trace-ability when required. At Afaridan Plastics, we have the flexibility to suit the requests of any order size and to tight schedules by coordinating either through our overseas office for large scale orders or in our Perth office for smaller orders.
We've been manufacturing plastic products for over 25 years, ensuring quality control at every step of the injection moulding process. We've streamlined our manufacturing to be as cost-effective as possible, with in-house design, tooling and moulding capabilities. The injection moulding methods we offer include:
GETTING A QUOTE WITH LK-MOULD IS FREE AND SIMPLE.
FIND MORE OF OUR SERVICES:
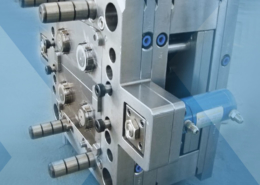
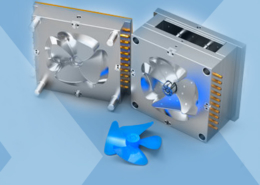
Plastic Molding

Rapid Prototyping
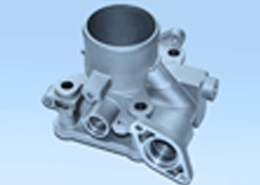
Pressure Die Casting
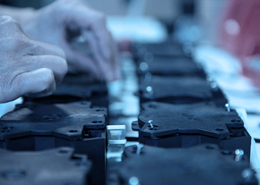
Parts Assembly
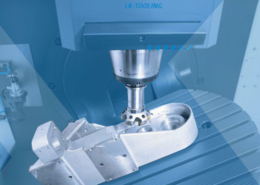