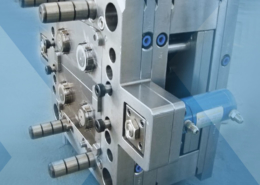
Exploring Medical Device Plastic Molding: A Comprehensive Overview
Author:gly Date: 2024-06-08
Medical device plastic molding is a crucial process in the manufacturing of various medical devices, ranging from simple syringes to complex implantable devices. This article aims to delve into the intricacies of this process, exploring its significance, techniques, challenges, and future prospects.
Importance of Medical Device Plastic Molding
The Vital Role
Medical device plastic molding plays a vital role in the healthcare industry by enabling the mass production of precise, durable, and cost-effective medical devices. It facilitates the production of components with intricate designs and specifications, meeting the stringent regulatory requirements of the healthcare sector.
Enhancing Patient Care
The ability to produce high-quality medical devices through plastic molding enhances patient care by ensuring the reliability and performance of these devices. From diagnostic tools to life-saving implants, molded plastic components contribute to the effectiveness of medical treatments and procedures.
Cost-Effectiveness and Efficiency
Plastic molding offers cost-effectiveness and efficiency in manufacturing medical devices compared to traditional machining methods. It allows for the rapid production of components in large volumes, reducing production costs and lead times while maintaining quality standards.
Techniques in Medical Device Plastic Molding
Injection Molding
Injection molding is the most common technique used in medical device plastic molding. It involves injecting molten plastic material into a mold cavity under high pressure, where it solidifies to form the desired shape. This technique is versatile, precise, and suitable for producing complex geometries.
Blow Molding
Blow molding is another widely used technique, particularly for hollow and container-like medical devices such as bottles, vials, and IV bags. It utilizes air pressure to expand a heated plastic parison (hollow tube) inside a mold cavity, conforming to the mold's shape to create the final product.
Extrusion Molding
Extrusion molding is suitable for producing continuous profiles or long-length components used in medical tubing, catheters, and seals. It involves forcing molten plastic material through a die to form the desired cross-sectional shape, which is then cooled and cut to the desired length.
Challenges and Considerations
Material Selection
Choosing the right plastic material is critical in medical device plastic molding to ensure compatibility with sterilization methods, biocompatibility, chemical resistance, and mechanical properties. Factors such as FDA regulations, material cost, and processing requirements must be considered during selection.
Quality Control
Maintaining strict quality control measures is essential to meet regulatory standards and ensure the safety and efficacy of medical devices. Inspection techniques such as dimensional analysis, visual inspection, and material testing are employed to identify defects and ensure product consistency.
Regulatory Compliance
Navigating the regulatory landscape, including FDA regulations and international standards such as ISO 13485, is a significant challenge in medical device plastic molding. Manufacturers must adhere to stringent requirements throughout the design, manufacturing, and post-market phases to obtain regulatory approval.
Future Directions and Recommendations
In conclusion, medical device plastic molding is a critical process that underpins the production of a wide range of medical devices. By embracing advanced technologies such as additive manufacturing, robotics, and digital twins, manufacturers can further enhance the efficiency, precision, and customization of molded plastic components.
As the healthcare industry continues to evolve, there is a growing need for collaborative efforts between manufacturers, regulatory bodies, and healthcare providers to address emerging challenges and drive innovation in medical device plastic molding. By prioritizing research and development, embracing sustainable practices, and leveraging digitalization, the future of medical device manufacturing holds promise for improved patient outcomes and healthcare delivery.
In summary, medical device plastic molding is not just a manufacturing process; it is a cornerstone of modern healthcare, enabling the innovation and production of life-saving medical devices. By understanding its intricacies, challenges, and future prospects, stakeholders can collaborate to ensure the continued advancement of medical device manufacturing for the betterment of global health.
GETTING A QUOTE WITH LK-MOULD IS FREE AND SIMPLE.
FIND MORE OF OUR SERVICES:
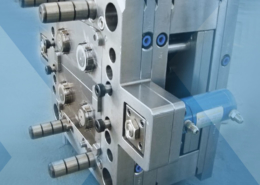
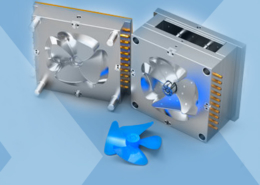
Plastic Molding

Rapid Prototyping
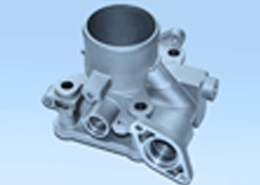
Pressure Die Casting
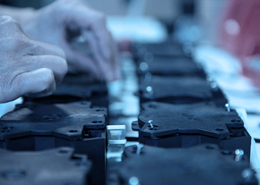
Parts Assembly
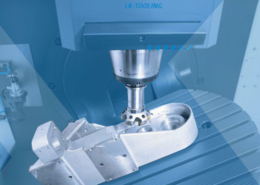