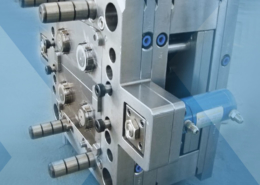
Unraveling the Marvels of Medical Injection Molding
Author:gly Date: 2024-06-08
Introduction
Medical injection molding stands as a beacon of innovation and precision in the realm of healthcare technology, revolutionizing the production of medical devices and components. From intricate surgical instruments to implantable devices, injection molding plays a pivotal role in shaping the landscape of modern medical treatment. This article delves into the intricacies of medical injection molding, uncovering its significance, techniques, applications, advancements, and challenges.
Significance of Medical Injection Molding
Precision and Consistency
Medical injection molding offers unparalleled precision and consistency in the production of intricate medical components, ensuring tight tolerances, minimal variability, and superior part quality. This precision is crucial for medical devices requiring precise geometries, such as catheters, syringes, and surgical instruments, to ensure optimal performance and safety.
Material Biocompatibility
The selection of biocompatible materials is paramount in medical injection molding to ensure compatibility with biological tissues and fluids, minimize the risk of adverse reactions, and comply with regulatory standards. Medical-grade polymers such as polycarbonate, polyethylene, and silicone exhibit excellent biocompatibility, making them ideal candidates for medical device manufacturing.
Cost-Effective Manufacturing
Injection molding offers a cost-effective solution for high-volume production of medical devices, enabling manufacturers to achieve economies of scale, minimize material waste, and optimize production efficiency. This cost-effectiveness is particularly advantageous for disposable medical products, such as syringes, IV components, and surgical trays, where mass production is essential to meet demand.
Techniques in Medical Injection Molding
Cleanroom Molding
Cleanroom injection molding facilities adhere to stringent cleanliness standards to prevent contamination and ensure the production of sterile medical devices. Cleanroom molding techniques, such as overmolding, insert molding, and micro molding, maintain cleanliness and integrity throughout the manufacturing process, meeting the rigorous requirements of medical device regulations.
Multi-Shot Molding
Multi-shot injection molding enables the integration of multiple materials or components into a single, seamless part, enhancing functionality, aesthetics, and performance in medical devices. This technique allows for the encapsulation of inserts, the incorporation of soft-touch grips, and the creation of multi-material structures with varying properties, expanding design possibilities in medical device manufacturing.
Liquid Silicone Rubber Molding
Liquid silicone rubber (LSR) molding offers exceptional precision, flexibility, and biocompatibility in the production of medical devices such as seals, gaskets, and implantable components. LSR molding techniques, including injection molding and compression molding, enable the fabrication of silicone parts with high consistency, durability, and resistance to extreme temperatures and sterilization methods.
Challenges and Future Directions
Regulatory Compliance
Navigating the complex landscape of medical device regulations, standards, and certifications poses challenges for manufacturers in ensuring compliance and product safety. Future research may focus on streamlining regulatory processes, harmonizing international standards, and implementing digital technologies to facilitate compliance management and regulatory reporting.
Advanced Materials and Additive Manufacturing
Advancements in materials science and additive manufacturing technologies offer new opportunities for innovation in medical injection molding. Research efforts may explore the development of bioresorbable polymers, antimicrobial materials, and personalized implants, leveraging additive manufacturing techniques such as 3D printing to produce patient-specific medical devices with enhanced functionality and biocompatibility.
Minimally Invasive Devices and Wearable Technology
The trend towards minimally invasive procedures and wearable medical devices drives demand for smaller, lighter, and more ergonomic components in medical injection molding. Future developments may focus on miniaturization, integration of sensors and electronics, and biocompatible materials to support the advancement of minimally invasive surgery, remote patient monitoring, and personalized healthcare delivery.
Conclusion
In conclusion, medical injection molding stands as a cornerstone of innovation, precision, and reliability in the field of healthcare technology. By leveraging advanced molding techniques, biocompatible materials, and stringent quality controls, manufacturers can produce a diverse range of medical devices that improve patient outcomes, enhance clinical workflows, and advance the practice of modern medicine. As technology continues to evolve and healthcare challenges evolve, the future of medical injection molding holds promise for continued innovation, collaboration, and impact in shaping the future of healthcare delivery and patient care. Embracing challenges, fostering partnerships, and embracing emerging technologies will ensure that medical injection molding remains at the forefront of healthcare innovation for years to come.
GETTING A QUOTE WITH LK-MOULD IS FREE AND SIMPLE.
FIND MORE OF OUR SERVICES:
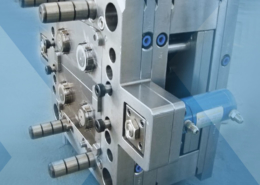
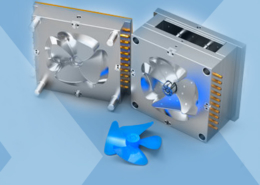
Plastic Molding

Rapid Prototyping
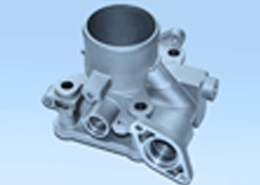
Pressure Die Casting
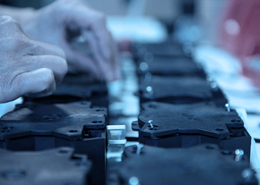
Parts Assembly
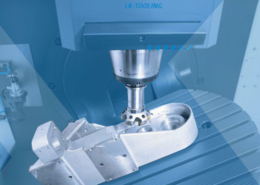