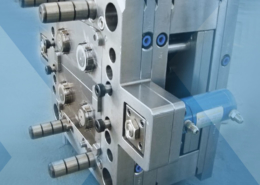
Exploring the World of Medical Device Plastic Injection Molding
Author:gly Date: 2024-06-08
Medical device plastic injection molding stands at the intersection of precision engineering and healthcare innovation, playing a crucial role in the production of intricate components for medical devices. In this comprehensive exploration, we delve into the intricacies of medical device plastic injection molding, uncovering its significance, applications, and future prospects.
Unraveling the Complexity of Injection Molding
Injection molding is a versatile manufacturing process that involves injecting molten material into a mold cavity, where it solidifies to form the desired shape. In the realm of medical devices, plastic injection molding offers unparalleled precision and scalability, enabling the production of complex geometries with tight tolerances. From implantable devices to diagnostic equipment, injection molding serves as the cornerstone of modern medical device manufacturing.
Precision Engineering
Precision is paramount in medical device manufacturing, where even the slightest deviation can have profound implications for patient safety and device performance. Injection molding allows for the production of components with micron-level accuracy, ensuring that each part meets the exacting specifications required for medical applications.
Material Selection
The choice of materials is critical in medical device manufacturing, where biocompatibility, durability, and sterilizability are paramount considerations. Injection molding supports a wide range of materials, including medical-grade polymers, elastomers, and bioresorbable materials, offering manufacturers the flexibility to select the most suitable materials for their specific application.
Advancing Healthcare Through Innovation
Medical device plastic injection molding drives innovation in healthcare by enabling the development of novel devices and technologies that improve patient outcomes and enhance the delivery of care. From miniaturized implants to wearable devices, injection molding facilitates the realization of groundbreaking innovations that push the boundaries of what is possible in healthcare.
Miniaturization and Integration
Miniaturization is a prevailing trend in medical device design, driven by the demand for devices that are less invasive, more portable, and more comfortable for patients. Injection molding enables the production of tiny, complex components that can be seamlessly integrated into compact medical devices, opening up new possibilities for diagnosis, monitoring, and treatment.
Customization and Personalization
Personalized medicine is revolutionizing healthcare by tailoring treatments to the unique characteristics of individual patients. Injection molding plays a key role in this paradigm shift, allowing for the mass customization of medical devices to meet the specific needs of each patient. Whether producing custom orthopedic implants or patient-specific surgical instruments, injection molding empowers manufacturers to deliver personalized solutions that optimize patient outcomes.
Ensuring Quality and Regulatory Compliance
Quality and regulatory compliance are paramount in the medical device industry, where patient safety is non-negotiable. Medical device plastic injection molding companies adhere to stringent quality management systems and regulatory requirements to ensure that their products meet the highest standards of safety, efficacy, and reliability.
Quality Management Systems
Quality management systems, such as ISO 13485, provide a framework for ensuring the consistent quality of medical devices throughout the manufacturing process. Injection molding companies implement robust quality management systems that encompass design controls, process validation, and risk management to mitigate the risk of defects and ensure the reliability of their products.
Regulatory Compliance
Regulatory compliance is a complex and evolving landscape, with regulations such as the FDA's Quality System Regulation (QSR) and the European Medical Device Regulation (MDR) setting forth stringent requirements for medical device manufacturers. Injection molding companies navigate this regulatory landscape with precision, ensuring that their processes and products comply with all applicable regulations and standards.
Conclusion
In conclusion, medical device plastic injection molding plays a pivotal role in the advancement of healthcare, driving innovation, precision, and quality in the production of medical devices. With its ability to realize complex geometries, support a diverse range of materials, and enable the mass customization of devices, injection molding is poised to continue shaping the future of healthcare. As we look ahead, continued investment in research and development, adherence to rigorous quality standards, and collaboration across the healthcare ecosystem will be essential to unlock new opportunities and address the evolving needs of patients worldwide.
GETTING A QUOTE WITH LK-MOULD IS FREE AND SIMPLE.
FIND MORE OF OUR SERVICES:
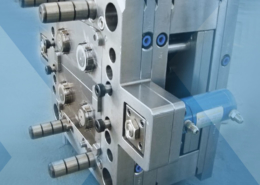
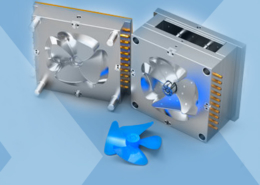
Plastic Molding

Rapid Prototyping
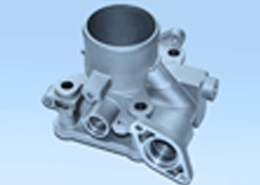
Pressure Die Casting
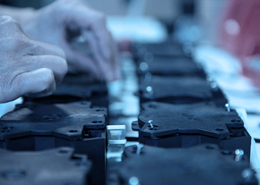
Parts Assembly
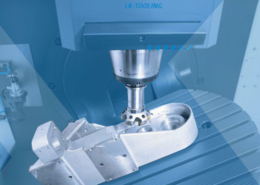