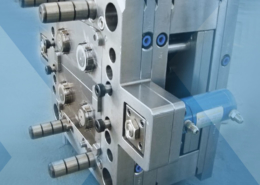
Blend Amorphous PHA with PLA to Improve injection ... - pla injection
Author:gly Date: 2024-10-15
Home // Products // Thermoplastic Elastomers // TPE Knowledge Center // Overmolding Guide // Overmolding: Mold Design
© 2015 – 2024. Avient Corporation. All Rights Reserved. Copyright & Legal Disclaimer. | Privacy Statement | California Privacy Rights | Email Fraud Information | Site Map | Web Design & Development by Upward Brand Interactions | Standard Contractual Clauses
For conventional cold runner tools, full-round runners are best because they provide the lease resistance to flow and minimize cooling in the runner. Cooling is minimized because full round runners have less surface area and therefore keep the material molten longer.
Hot runner tool layout should be naturally or geometrically balanced. Externally heated manifolds are best. Internally heated systems, which use torpedo heaters, are not recommended because they have hot spots, stagnation zones and partially solidified material clinging to the walls.
With the 3K multi-shot molding approach, we are able to achieve tremendous costs savings and production quality repeatability.
Another major potential problem we might face would be the delamination of the individual components after the injection molding process; this is particularly so for the soft thermoplastic bonding to the hard.
The second most efficient runner cross-section is the modified trapezoid. This type of geometry most closely simulates a full round runner but only requires machining in only one plate.
Multi-cavity tool layouts should be balanced. In a balanced runner system, molten material flows into each cavity at equal times and pressure. Examples of balanced spider and cross-runner systems are shown in the figures below:
Since the assembly of the component is confined within a very tight package, the bonding area between the hard and soft thermoplastics is very limited and that runs the risks of the 2 material delaminating during cycle tests or even failure. The Kore team has to review the entire assembly with the internal electronics and add more contact
After reviewing the part geometry and its requirements, the most cost-effective and robust approach to build the part is to develop and produce the part, is a single injection molding cycle with a single triple-shot injection molding process.
All passages should have highly polished circular cross sections with gentle bends to minimize the possibility of stagnation zones, and a diameter of 0.250" to 0.375". Individualized zone controls will allow for some balance adjustment and will improve part quality.
For high volume production, the initial expense of quality tooling is a sound investment. The choice of tool steel will depend on the quantity and quality of parts to be produced and will be primarily determined by the type of rigid substrate being used in the application. If a reinforced substrate material is used a high hardness abrasion resistant steel may be required.
The multi-shot injection molding engineering team at Kore Industries proposed and implemented geometric modifications to the part CAD that makes it feasible to build the part with a single 3K injection molding process.
A cost-effective solution has been found to this technically demanding and potentially labor intensive challenge faced by our customer.
The table below summarizes the advantages and disadvantages of a variety of gate designs. For more in-depth information about a specific gate design, please download the full-length Overmolding Guide.
Runner dimensions rarely exceed 0.300" even for the main runner. Cold slug wells should be used each time the runner makes a turn or divides.
One of the challenges we face for building the part with 3K injection molding process is the risk of the second shot material melting the first shot in the second shot molding cycle. Therefore the processing and material selection is of key importance here.
Most GLS materials overmolding materials are generally non-abrasive / non-corrosive and replicate the mold surface fairly well.
For any technical consultation or to get a quick quote, please contact us by filling up the form below. We’ll get back to you as soon as we can.
All conventional gating types are suitable for processing GLS elastomers. The type of gate and the location, relative to the part, can affect the following:
Customer faces challenges with development and manufacture of a multi-component part that requires incorporation of 3 different thermoplastic polymers.
The type of gating is dependent on both part and tool design. For automatically degating tools, the highly elastic nature of softer TPEs makes gate design such as submarine gates or three plate tools with self-degating drops more difficult. Higher hardness and filled grades usually have lower ultimate elongation and therefore are more easily degated. To assure that a gate will break at a specific location, the land length should be short to create a high stress concentration.
The objective of selecting this approach is to simplify the build process and reduce the production costs as well as the enhancement to the functionality of the end part with this innovative triple-shot injection molding process.
This is an application for employment with Kore Industries. This application will be considered current for a period of sixty (60) days following the date of application. If, at the end of this period, you still wish to be considered for employment by Kore Industries. It will be necessary for you to complete another application. Kindly complete the attached Consent Form before the application is considered valid.
GETTING A QUOTE WITH LK-MOULD IS FREE AND SIMPLE.
FIND MORE OF OUR SERVICES:
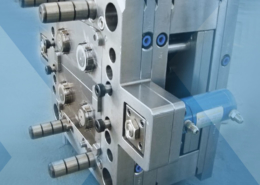
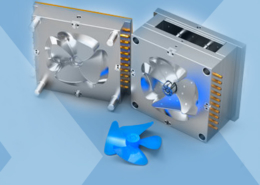
Plastic Molding

Rapid Prototyping
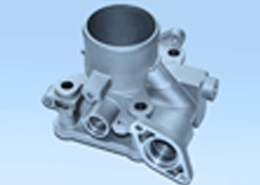
Pressure Die Casting
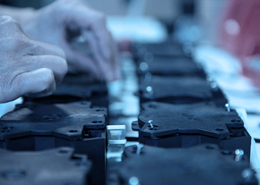
Parts Assembly
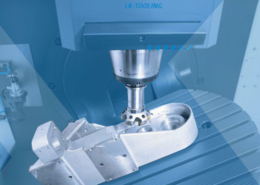