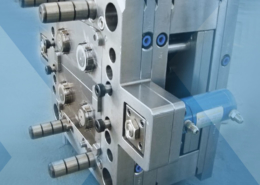
Bobbin 20mm Yellow Beaded BASICS Polcore Moulding - bobbin molding
Author:gly Date: 2024-10-15
With the help of clean room injection molding, medical manufacturers can safely provide quality-assured products to hospitals, clinics, and patients. This process ensures that medical devices are safe, ultimately improving patient care.
Among these standards, ISO 8 is commonly used in medical device manufacturing. Learn more about these classifications in this article: What is an ISO 8 Cleanroom? Principles & Requirements
The pharmaceutical industry takes cleanliness and hygiene to a microscopic level. Clean rooms help manufacturers create products that adhere to strict quality control standards and regulatory compliance.
Clean rooms are highly controlled environments that minimize the risk of airborne particles getting into products or equipment. They prevent dust, dirt, and microbes from contaminating sensitive materials.
Products are packaged in specialized containers or packaging materials to protect against contamination during storage and transportation.
Products typically go through sterilization processes to remove remaining microorganisms so they are safe for medical or pharmaceutical use. Manufacturers commonly use ethylene oxide (EtO) sterilization and gamma irradiation.
Inject molding in clean rooms has a strict operating procedure to ensure the product manufactured is safe and effective:
Choosing the right clean room injection molding manufacturer makes all the difference in ensuring product safety and quality. Here are some key questions to help you choose:
In the structural foam molding process, a physical or chemical blowing agent is mixed in with the resin. The resin is shot into the cavity, but not completely filled or packed out. The blowing agent expands to push the resin to the extremities of the cavities. As the part cools, the internal pressure of the foaming action takes up the internal shrinkage, and reduces sinks over ribs or heavy cross-sections.
Quality control tests, such as visual inspection, dimensional measurements, and functional testing, are performed to make sure the product works as intended.
Clean rooms sometimes use Ultra Low Penetration Air (ULPA) filters, which provide even higher filtration that can catch particles invisible to the naked eye.
In injection molding, a clean room provides a sterile space to melt plastic resins, inject them into molds, and cool them off. They aim to ensure that the final products are safe and effective. Below is the common industries that require cleanroom environments:
Medical device manufacturing adheres to ISO 13485, a global quality management system standard. While it doesn’t classify clean rooms, It’s in place to safeguard the quality and safety of medical devices produced in clean room environments.
There are many advantages of the structural foam injection molding which combine to provide an economical advantage over other processes, and allow production of parts which can’t be matched by any other process. Following is a list of many of the advantages of the structural foam molding process:
In industries like healthcare, pharmaceuticals, and biotechnology, cleanliness is an absolute necessity. A single spec of dust can contaminate a life-saving drug or compromise a medical implant. That’s why clean room injection molding has become an indispensable part of manufacturing in these industries.
Structural foam is a low-pressure form of injection molding, which utilizes most thermoplastics, (including post-consumer regrind), to mold rigid products, which can have thicker walls and higher stiffness-to-weight ratios than standard injection molded products.
Raw plastic resins are selected and prepared according to strict quality control standards. This often includes drying or pre-heating the resin so that they are easier to process.
ISO 14664-1 is the current international standard clean room classification system. It classifies clean rooms into ranges from ISO 1 (the cleanest) to ISO 9, each with a specific limit for particles in the environment.
With over 40 years of experience and state-of-the-art facilities, including ISO Class 7 and 8 cleanrooms, we’re able to handle even the most demanding projects. Our commitment to quality and safety is also reflected in our ISO 13485:2016 and ISO 9001:2015 certifications.
My mission at Polymer Resources has not changed since I founded this company more than four decades ago. It includes continuing our tradition of financial stability, sustainable growth and visionary leadership that compounds success for customers, suppliers and employees. It also means proudly manufacturing our products in America, and making them available to the global marketplace.
Structural foam molding minimizes molded-in stress that can lead to warpage and part deformation. Other advantages include less energy usage due to the low-pressure process and cost savings and sustainability from using less resin and less-expensive aluminum tooling. Also, versatility in part geometry, from thin walls to very thick and large shapes, is an additional benefit of using structural foam. Aesthetically, the foaming bubbles in the matrix pack out the resin and reduce the incidence of sink on the exterior show side of the plastic part.
Clean rooms have specialized airflow systems to control the movement of air and keep the environment clean. There are two types of airflow:
The resins are melted and injected into precision molds inside the clean room. Temperature, pressure, and injection speed, are controlled to achieve the desired product quality and consistency. Click here to know more details about how injection molding works.
Biotechnology workers know how important it is to stay clean. They often work with sensitive biological materials like cells, tissues, and microorganisms. Clean rooms help maintain a sterile environment and avoid contamination.
Clean rooms are classified based on their level of cleanliness, which is determined by the number and size of particles allowed per cubic meter of air.
Fs 209E is an older US federal standard that ISO standards have mostly replaced. Although some industries, like semiconductor manufacturing, still use this as a benchmark. Classifications range from Class 1 (the strictest) to Class 100,000 — each class also has a specific particle count.
High-Efficiency Particulate Air (HEPA) filters are essential in injection molding. They catch and remove 99.9% of microparticles from the environment.
THY Precision understands the importance of clean room injection molding in delivering safe, sterile, and quality products for the medical, pharmaceutical, and biotechnology industries.
It’s so effective that clean rooms are essentially classified based on the number of particles allowed per cubic meter of air.
GETTING A QUOTE WITH LK-MOULD IS FREE AND SIMPLE.
FIND MORE OF OUR SERVICES:
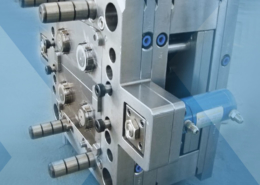
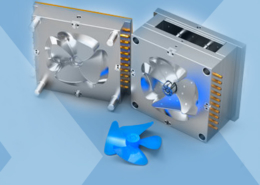
Plastic Molding

Rapid Prototyping
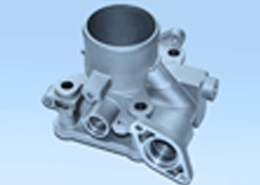
Pressure Die Casting
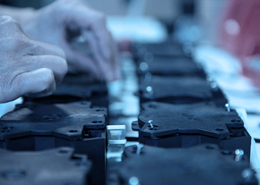
Parts Assembly
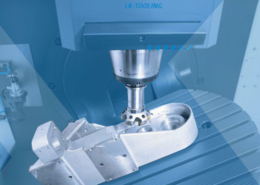