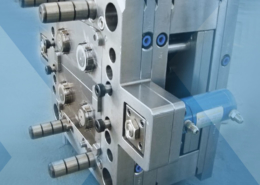
Blend Amorphous PHA with PLA to Improve injection ... - pla injection molding
Author:gly Date: 2024-10-15
The melt flow rate confirms the ability of the molten plastic to flow without complications. As such, it is measured in grams every ten minutes. As there are different plastics utilized in injection molding, so does the melt flow rate vary. But the application of the material contributes to the output of the finished product.
After a few years of working abroad in Paris and Tokyo, Rebecca Dufour Partanen embarked on a journey that would see her pivot for a fashion and beauty startup in New York and return home to Stockholm with a fresh idea for her own slow...
Sulapac Universal Flex 35 is a sustainable, beautiful, and functional injection molding material which contains 87% USDA certified bio-based content. The material is designed for thin-walled structures with good impact strength and is easy to process with minimal, if any adjustments needed for the existing machinery.
1 Suitable for reusable applications as per European Commission regulation (EU) No 10/2011. Dishwashability tested according to EN 12875 standard with 20 washing cycles.
Supplements that meet people’s unique needs In developed countries people have better living standards than ever before. A high standard of living has enabled people to focus on their health by using health apps and smart rings....
Sustainable innovation approach It all began with a desire. In 2018, LES EAUX DE CHANEL introduced a new olfactory world to the fragrances of the House: a singular collection, inspired by Mademoiselle Coco Chanel’s favorite places,...
The material is processable with existing injection molding machinery. Our experts assist with the tests and production settings from mold selection to nozzle size.
Sulapac® materials can be used with existing injection molding machinery, enabling a resource efficient transition towards a cleaner future.
Sulapac Barrier contains 98% USDA certified biobased content2 and biodegrades without leaving persistent microplastics3 or toxic load behind. The material is food contact compliant4 and certified industrially compostable by BPI5.
Biodegradable plastics are plastic wastes that naturally break down over time, making them reusable as plastic pellets for injection molding. Nonetheless, they are suitable for plastic materials whose shelf life is typically limited. An example of such plastic is disposable cutlery. They are eco-friendly and environmentally safe for production purposes and simultaneously reduce waste accumulation.
4 Can be recycled through hydrolysis back to monomers, suitable as feedstock for recycled biopolymers. Mechanical and chemical recyclability tested and proven technically feasible by third parties. Field tests have also verified that Sulapac materials can be collected and sorted out of a mixed waste stream. When collected together, Sulapac materials do not interfere with the current mechanical recycling of conventional fossil- based or bio-based non-biodegradable plastics. The technology for chemical recycling of bio-based and biodegradable materials exists, but the infrastructure is still under development.
At this stage, the plastic pellets are appropriately dried and conditioned to meet the melting requirements and transferred from the hopper into the barrel for melting. There are in-process parameters to be adhered to at each manufacturing stage. During melting, the required temperature to melt the plastic pellets must have been set. In addition, the injection speed and pressure settings are essential to achieve the desired part intended.
Sulapac Universal Heat 30 is a sustainable, beautiful, and functional material for injection molding containing 70% USDA certified biobased content. The material is optimized for high heat resistance without additional or post-treatment, with ideal flexural strain and impact strength, making it a great option for single-use and reusable cutlery1 with outstanding usability.
Sulapac Luxe is the ultimate answer for brands looking for a sustainable yet luxurious replacement for hard plastics like ABS. Sulapac Luxe is ideal for fragrance bottle caps, jars, and lids.
Sulapac® materials are the sustainable, beautiful, and functional alternative to conventional plastic. Start using Sulapac with your existing injection molding equipment and gain competitive advantage through sustainability and innovation.
Sulapac® materials are the sustainable, beautiful, and functional alternative to conventional plastic. Start using Sulapac with your existing injection molding equipment and gain competitive advantage through sustainability and innovation.
This post will be delving deeper into the amazing world of plastic pellets, while we get to understand the options available for plastic parts production. We’re ready when you are.
Considering that the focus of this post is the selection of a suitable plastic pellet, it is paramount to consider certain aspects that assist in this area. Frankly, material property and requirements are essential aspects to be considered. The reason being that before injection molding can proceed, the project requirement must be analyzed. This includes strength, chemical resistance, and flexibility, to mention a few. On top of that, not all materials are capable of the required properties intended for the project.
Considering the roles of plastic pellets and the importance of selecting the right one with accurate properties for injection molding, several types of pellets come up regularly for most projects. The major plastic injection molding materials are highlighted below.
Certain parts require high heat resistance. In such projects, materials such as polyetheretherketone are likely to achieve such feats. In addition, for flexibility-related products, thermoplastic elastomers (TPE) like polyurethane (PU), or thermoplastic vulcanizates (TPV) may be appropriate.
To wrap up, plastic pellets are crucial to the injection molding process. But understanding the various types available for injection molding including polypropylene, ABS, and polyurethane among others is way more important. The selection of the type of plastic pellet is strictly reliant on the material property, compatibility, and quality of the material. Moreover, processing the plastic pellets includes drying and conditioning, melting, and molding, and the effects of recycled or reinforced plastic pellets on injection molding.
1Biodegradation of 48%–59% in 280 days in the marine environment (30ºC/86ºF) (ASTM D6691). Tested also according to ASTM 5511 (accelerated biodegradation in the landfill, 37ºC/99ºF): 68% relative biodegradation in 160 days. Not considered degradable in California.
4 Can be recycled through hydrolysis back to monomers, suitable as feedstock for recycled biopolymers. Mechanical and chemical recyclability tested and proven technically feasible by third parties. Field tests have also verified that Sulapac materials can be collected and sorted out of a mixed waste stream. When collected together, Sulapac materials do not interfere with the current mechanical recycling of conventional fossil-based or bio-based non-biodegradable plastics. The technology for chemical recycling of bio-based and biodegradable materials exists, but the infrastructure is still under development.
Supplements that meet people’s unique needs In developed countries people have better living standards than ever before. A high...
These are determinants of how the final product turns out. Conclusively, industry trends and innovations are deriving sustainable methods of sourcing plastic pellets. Some of these are biodegradable and bio-based materials and the introduction of additives and fillers. As a manufacturer or enthusiast, arming yourself with this knowledge saves you a whole lot of stress and wastage, while providing you with the best manufactured plastic component ever.
5 As the compostability of an end product is also dependent on the geometry of product, it is the responsibility of the manufacturer of the end product to ensure compliance with the regulations.
What’s more, the features of each plastic pellet can influence the melt flow rate of each plastic pellet. This is the reason selecting the appropriate plastic pellet for the desired molded parts is essential for plastic injection molding as well as for high-quality mold manufacturing.
The Sulapac Premium material makes your products look and feel luxurious. The ceramic sound and visible wood chips’ haptic touch make it stand out. It is ideal for sustainable products that aim for an exclusive feel.
Plastic pellets for injection molding have practically been the most important material that has happened to manufacturers of plastic parts and products, including end users from different walks of life. How has this been you may wonder?
Selecting the right plastic pellets directly affects the quality and consistency of the parts manufactured. To achieve product quality and consistency it may be wise to acquire plastic pellets from a tested and trusted supplier who understands the assignment. Additionally, consistent plastic pellets’ shape and size ensure proper and predictable melt flow that translates to the overall quality of parts produced. Any irregularly shaped plastic pellet could result in product defaults such as voids and internal stresses.
3 Raw materials fulfil the requirements for heavy metal tresholds and ecotoxicity according to EN13432 and ASTM D6400.The material complies with the EU and US FDA food contact requirements (restrictions and specifications of use apply, further information in Declaration of Compliance).
1Material is suitable for repeated use as per European Commission regulation (EU) No 10/2011. Dishwashability tested according to EN 12875 standard with 125 washing cycles.
3 Fully biodegradable in simulated marine environment tests according to ISO 22403 and ASTM D6691. Relative biodegradation of 100% (ISO 22403, 27°C / 80°F) and 92% (ASTM D6691, 30°C / 86°F) in 56 days using natural sea water. Not considered biodegradable in California.
Reinforced plastic pellets as well usually contain additives that can increase the functional features of the plastic material. Although, it may impact flow quality, and the ability to efficiently mold. Modifications can be made to accommodate them.
Sulapac Luxe Flex contains 73-86 % USDA certified biobased content1, sustainably sourced biodegradable biopolymers being the main raw material. Sulapac Luxe Flex is safe for people and planet2. It has been certified industrially compostable by TÜV Austria.3 The material is recyclable by design and can also be made with recycled content.4 Available as non-GMO; ask more from your account executive!
2 Sulapac materials within the same family of recipes show biodegradation of 57,6% at 462 days in the marine environment (30ºC / 86ºF) (ASTM D6691), 28% at 153 days when tested according to ASTM 5511 (99 ºF) accelerated biodegradation in the landfill.
1The compostability has been tested up to the thickness of 1,48 mm. As the compostability of an end product is also dependent on the geometry of product, it is the responsibility of the manufacturer of the end product to ensure compliance with the regulations.
These tiny raw materials have been the major medium used for manufacturing electronic parts, toys, automotive parts, and packaging containers. However, the selection of suitable plastic pellets, the different types available, and their applications are what manufacturers have to consider before employing injection molding as the method of production.
Moreso, there’s the option of bio-based plastic pellets which is another alternative means to create raw materials. An innovative advancement that sees plastic pellets derived from renewable, plant-based sources. Plant materials like sugarcane and corn starch are sustainable forms of plastic raw materials in contrast to petroleum-based plastics. Many of the new-age plastic manufacturing companies are environmentally conscious and devoted to reducing toxic waste. Thus, in the high-quality mold manufacturing industry and plastic molding industry more renewable and greener sources of plastic pellets materials are now available.
The unique combination of raw materials: responsibly sourced biodegradable biopolymers and naturally occurring clay minerals, gives Sulapac Solid its beautiful ceramic look and feel, even sound, that makes it stand out. Sulapac Solid meets the EU and FDA requirements for food contact materials5 and it contains zero PFAS6.
4 Restrictions and specifications of use apply, please refer to the relevant Declaration of Compliance for further information.
Sustainable innovation approach It all began with a desire. In 2018, LES EAUX DE CHANEL introduced a new olfactory world to the...
20,57 kg CO2 eq/kg based on cradle-to-gate LCA performed by an independent third-party consultancy (biogenic carbon included).
5Restrictions and specifications of use apply, please refer to the relevant Declaration of Compliance for further information.
The Universal Flex 30 is ideal for single-use and reusable cutlery that ensures easy mass-manufacturing and outstanding usability. Beautiful and sustainable option for injection molding. Ideal flexural strain and impact strength for complicated designs like knives and forks. Suitable for food contact according to EU and FDA.1
3 Restrictions and specifications of use apply, please refer to relevant Declaration of Compliance for further information.
A noteworthy inclusion is the flow characteristics and moldability of plastic materials. This factor may require design adjustment or process modifications to attain proper filling of the mold and excellent product finish.
On the other hand, uncontrolled pressure is capable of damaging the mold and as the product can suffer from internal stress.
Universal material is made of wood from side streams and biodegradable biopolymers. This 100% bio-based material biodegrades without leaving persistent microplastics behind1.
In this environmentally conscious world that we live in, handling recycled or reinforced plastic pellets presents ecologically beneficial advantages. In the same vein, it poses other challenges. Recycled plastics are already formed plastic pellets that are meant for reuse. For this reason, the variation in composition should be factored in. Its material makeup may tend to lead to difficulty in processing, differences in strength, and melt flow. For this to function in injection molding, it must be subjected to a series of tests that will help determine how best to apply them.
One more factor is the cooling time. A shorter cooling time increases productivity by reducing cycle time, meanwhile longer cooling time can ensure proper solidification of parts but takes longer and productivity is negatively impacted.
4Relative biodegradation of 77,3% in 420 days in simulated marine environment test (ASTM D6691 86 °F/30 °C) using natural sea water. Not considered biodegradable in California
Fillers such as glass fibers, mineral powders, and carbon fibers are not left out. They improve plastic pellets structurally by reinforcing plastic materials. With such reinforcements, plastic products become triple-strong. Offering durability, strength, and high performance to plastic pellets that lack in such areas.
One such precaution is material drying and conditioning. Why should dry or condition the material you may be thinking about? Material drying helps to eliminate moisture content in the plastic pellets. The inclusion of moisture before sending it to the barrel for melting is liable to cause voids in the pellets. Moist can also be responsible for lower mechanical features of the pellets that can impair the product’s qualities. Drying methods such as desiccant drying, hot air drying, or vacuum drying are applied during the drying process.
Sulapac Luxe contains 73-87% USDA certified biobased content1, sustainably sourced biodegradable biopolymers and non-visible wood flour from industrial side streams being the main components. The material is safe for people and the planet: it leaves no persistent microplastic2 or toxic load3 behind. Sulapac Luxe is recyclable by design4 and can also be made with recycled content.
Sulapac materials for injection molding are sustainable alternatives for PS, ABS, PC and PP. They can be used for various applications including cosmetic packaging, kitchenware, and cutlery.
Sulapac Universal Flex 35 is safe for both people and the planet: the material is certified as industrially compostable by BPI1 and leaves no persistent microplastics2 or toxic load behind. Universal Flex 35 meets the EU and US FDA requirements for food contact materials for dry food3 .
Sulapac Universal Heat 30 is safe for people and the planet: It is made of industrially compostable raw-materials and leaves no permanent microplastic2 or toxic load behind.
Adhering to these in-process parameters delivers quality products with structurally sound parts and excellent surface finish.
7 The heat resistance of the end product is dependent on the geometry and the manufacturing process of the product. It is the responsibility of the manufacturer of the end product to test and validate the maximum usage temperature and optimize the manufacturing process.
Computer-based manufacturing techniques like high-quality CNC Machining can deliver high quality with little human input. Plastic molding on the other hand relies heavily on close monitoring of important parameters chief of which is the type of plastic material used.
2Biodegradation of 79% in 308 days in the marine environment (30 °C / 86 °F) (ASTM D6691). Tested according to ASTM 5511 (accelerated biodegradation in the landfill 37°C / 99 °F): 52% relative biodegradation in 210 d. Not considered biodegradable in California.
Relative biodegradation of 70% in 58 days when tested in simulated solid-state anaerobic condition (ASTM D5511, 37°C / 99 ºF) representing an accelerated biodegradation in a landfill.
To maximise the functionality of your end product, there’s a range of material grades you can choose from with different flexural and tensile properties, heat resistance and density. In terms of look & feel, you can opt for a natural appearance with large wood chips or a smooth polished surface, or something in between!
Sulapac Premium is made of wood chips from industrial side streams combined with biodegradable biopolymers. This 100% bio-based material biodegrades without leaving persistent microplastics behind1.
The Sulapac Premium material makes your products look and feel luxurious. This grade of Premium is more flexible and has a better impact strength. The visible wood chips and haptic touch make it stand out. It is ideal for brands that value sustainability while aiming for that exclusive feel.
In addition to material properties and requirements, understanding the plastic pellets that align with injection molding is paramount. Compatibility with the molding process must be considered to ascertain plastics with precise melt flow rate (MFR), and temperature as it relates to melting and cooling. These are determinants of its ability to mold properly.
Another crucial factor in part formation is the type of pellet being used. There are various types, and their application to part formation depends on what the mechanical features, aesthetical properties, and the designed lifespan of the molded part should be. Considering that, the impact and chemical resistance in each type of plastic pellet is different. Some possess higher impact resistance to chemical resistance and vice versa.
Sulapac’s patent pending innovation is a perfect fit for cosmetic brands seeking for a sustainable packaging for water-based formulas. Used as the inner layer of a jar, it provides an excellent barrier against water evaporation and enables you to pack your emulsions in beautiful, bio-based and biodegradable Sulapac packaging. The weight loss of Sulapac Barrier in one year (demonstrated shelf life) is well below 3%1, which is the typically accepted maximum weight loss for cosmetic packaging.
Consequently, conditioning the plastic pellets for injection molding represents keeping the pellets at a conducive temperature before proceeding to melt the plastic pellets. It’s a form of preparatory step conditioning the plastic pellets in readiness for melting. Conditioning assists the plastic pellets to melt accordingly, thereby fostering the proper melting of the pellets.
1 Sulapac materials within the same family of recipes show biodegradation of 26-60% at 140 days in the marine environment (30ºC / 86ºF) (ASTM D6691).
Deep concerns have sprouted over the usage and disposal of plastic waste which may have an increased environmental impact on our world today. It is for this reason that manufacturers of plastic parts and components seek to find sustainable alternatives to sourcing plastic pellets as raw materials. One such way is via biodegradable plastic pellets or bio-based materials.
1 Sulapac Universal Flex 30 meets the EU and US FDA requirements for food contact materials. Restrictions and specifications of use apply, please ask for Declaration of Compliance for further information.
Replace conventional plastic with the beautiful, functional and sustainable Sulapac material. We will help you to make the switch smoothly.
Additives no doubt double the confidence you have in your plastic pellets to produce industry standard, excellent performance plastic parts and components.
This bio-based (87%) material is safe for people and the planet: it is industrially compostable and biodegrades without leaving persistent microplastics behind1.
After a few years of working abroad in Paris and Tokyo, Rebecca Dufour Partanen embarked on a journey that would see her pivot for a...
The accurate melting temperature must be set. Once this is in order, the plastic is melted to the required temperature. The injection speed ensures regular mold filling as too much speed can result in defects in the mold. While a slow-speed injection can result in short shots or part deficiency. Injection pressure ascertains how much flow of the melted plastic pellets enters the mold. The injection pressure must be adequate to fill the mold as insufficient pressure can negatively impact the part produced.
2 Relative biodegradation of 49,7 % in 308 days in simulated marine environment test (ASTM D6691 86 °F / 30 °C) using natural sea water. Not considered biodegradable in California.
When it comes to chemical-resistant plastic pellets, not all polymer resins are chemical resistant. While some boast of higher chemical resistance to other plastic pellets. Plastic pellets that are chemical resistant include fluoropolymers like polytetrafluoroethylene (PTFE) or polyvinylidene fluoride (PVDF). These material properties reflect on the product, and because of that proper consideration must be assigned.
Without plastic pellets for injection molding the process is considered inefficient. These polymer resin-made pellets are the primary input to the plastic parts and tools formed with injection molding. However, the formation of parts relies greatly on the properties of the plastic pellets. They are of different resins and can transform into any desired shape just like other advanced manufacturing techniques like 3D printing technology. The transformation process duly begins when the plastic pellets are fed into the barrel where heating and melting take place. The molten plastic is then injected into the mold cavity to take shape. These steps are crucial to part formation.
Please note that if the end product needs to be resistant to high temperatures (HDT-B 130 °C)6, the minimum mold temperature is 100°C7.
The material is processable with existing injection molding machinery. Our experts assist with the tests and production settings from mold selection to nozzle size.
Sulapac Solid is a sustainable injection molding material ideal for kitchenware used on a daily basis, such as plates, mugs, bowls and containers. It has high impact strength and it is dishwasher1 and microwave safe. The material is available in natural, white and black color.
The material has high density, good resistance to temperature fluctuations and a unique, ceramic look and feel, even sound. With Luxe both shiny or a matt surface can be achieved depending on your mold selection.
3The compostability has been tested up to the thickness of 150μm according to BPI (ASTM D6400). As the compostability of an end product is also dependent on the geometry of product, it is the responsibility of the manufacturer of the end product to ensure compliance with the regulations.
2 Ecotoxicity and threshold values for heavy metals tested according to EN 13432. The material complies with the EU and US FDA food contact requirements (restrictions and specifications of use apply, further information in Declaration of Compliance).
Replace your traditional plastic material and start mass-producing truly sustainable products with minimal investment. Universal material is designed to fit to existing production lines and molds. It is suitable for rigid products such as jars and hangers. Technical specification and easy processing instructions are available in the technical datasheet.
Sulapac Luxe Flex is a sustainable material for injection molding ideal for replacing hard plastics like ABS. Luxe Flex can be used to manufacture fragrance caps, cosmetic jars, lids, compact powder boxes, and pencils, for example. The material is resistant to temperature fluctuations, has a high density and a premium look and feel, even sound. With Sulapac Luxe both shiny and matt surface can be achieved depending on your mold selection. The material has excellent processability and it is easy to color with Sulapac masterbatches. Luxe Flex is now also available as black granules!
Industry trends and innovations are skyrocketing, especially in plastic manufacturing. The stakes for innovative mediums of sourcing for sustainable, improved materials to fashion out sound injection-molded plastic components just got raised. Another such introduction is additives and fillers.
6Sulapac Solid has been tested for per-and polyfluoroalkyl substances (PFAS) by an independent laboratory (ISO/IEC 17025 certified) based on CEN/TS 15968 test method; No PFAS compounds were detected.
2 Biodegradation of 56,7% in 280 days in the marine environment ASTM D6691(86°F / 30°C). Not considered biodegradable in California.
The material contains 100% USDA certified biobased content. Sulapac Solid has low carbon footprint2, and it is certified as industrially compostable by BPI3. It doesn’t leave persistent microplastics or toxic load behind4. Furthermore, the material is certified chemically recyclable by LOOPLA technology.
1 Material version with USDA Certified Biobased Product label (certification mark of the U.S. Department of Agriculture) available.
Our experts are happy to support you in choosing the right material. Contact our sales to discuss more or ask for a quote.
Many things can go wrong if the process of injection molding does not fulfill some qualifications. These prerequisites are likely to disrupt the balance of the injection process which can in turn lead to defects, reduced structural integrity, and reduced melt flow. However, all of these can be averted if precautions are duly executed.
Melting temperature is the next parameter to consider. The regulated or industry-stipulated melting temperature should be set. An exceedingly high temperature can result in material deterioration and degradation, while too low a temperature may result in an incomplete melting of the plastic. For that reason, it could be eliminated by setting the appropriate melting temperature according to material properties.
3Restrictions and specifications of use apply, please refer to relevant Declaration of Compliance for further information.
A few other plastic materials such as polycarbonate, polyethylene terephthalate (PET), and nylon are some other plastics utilized in injection molding and in the high-quality mold manufacturing industry.
GETTING A QUOTE WITH LK-MOULD IS FREE AND SIMPLE.
FIND MORE OF OUR SERVICES:
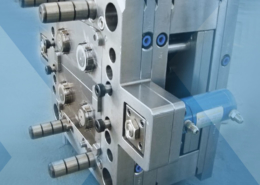
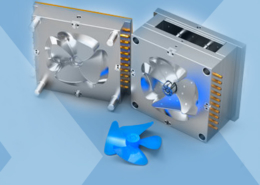
Plastic Molding

Rapid Prototyping
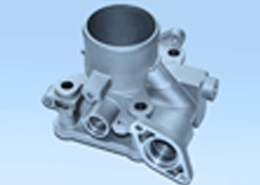
Pressure Die Casting
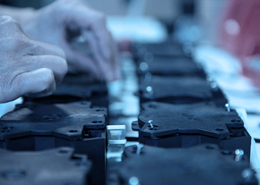
Parts Assembly
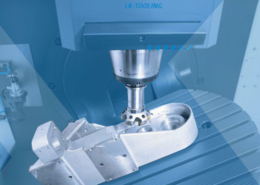