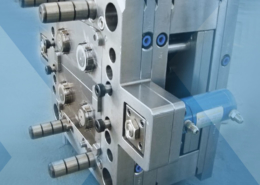
Blend Amorphous PHA with PLA to Improve injection ... - pla injection molding
Author:gly Date: 2024-10-15
Hydraulic presses have historically been the only option available to molders until Nissei Plastic Industrial Co., LTD introduced the first all-electric injection molding machine in 1983.
The projected area of ââthe finished product in the mold opening and closing direction is derived from the overall dimensions of the finished product.
Sumitomo (SHI) Demag Plastics Machinery North America, Inc. is part of a global group of companies dedicated to helping plastics processors compete more effectively in the global marketplace. Sumitomo (SHI) Demag and its Japanese parent company, Sumitomo Heavy Industries (SHI), are one of the specialized manufacturers of high-precision, high-performance plastic injection molding machines with annual sales of more than 5,000 units. The world's largest manufacturer of IM machines. Its global injection molding machine development and production network consists of four factories in Japan, Germany and China, with more than 3,000 employees.
The company's main business verticals are automotive, packaging, medical, electrical, sports and leisure, toys, construction, etc.
The opening and closing stroke should be at least twice the height of the finished product in the opening and closing direction, and should include the length of the vertical runner; the holding stroke should be sufficient to eject the finished product.
There are many different types of injection molding machines, and choosing the right type can bring greater benefits to your business.
There is no doubt that investment in injection molding machines is expensive and needs to be carefully considered. If you are looking for a suitable plastic injection molding machine manufacturer, you can look to us at Log Machine or a Chinese injection molding machine manufacturer, because Chinese plastic injection molding machines provide competitive prices while ensuring high quality. Investing in the right injection molding machine will pay off.
Arburg is a German mechanical engineering company and a world-renowned manufacturer of injection molding machines. Owned by the Hehl and Keinath families, it ranks among the global industry leaders with its electric, hybrid and hydraulic plastic injection molding machines, turnkey systems and its industrial additive manufacturing systems.
When the raw material is injected into the mold cavity under high pressure, the clamping force is generated, so the clamping unit of the plastic injection molding machine must provide enough "clamping force" to prevent the mold from opening. The clamping force requirement is calculated as follows.
Haitian is a leading plastic injection molding machine manufacturer in China. Haitian International Holdings Limited has accumulated more than five years of basic technical experience in the production of "Haitian" brand injection molding machines, and reached a new milestone in the company's history when it was listed on the stock exchange. The advanced corporate structure thus brings a crucial step towards the decisive globalization of the brand. The main focus of the Haitian brand is the development and production of standard injection molding machines for the mass production market. In this area, we create a vital competitive advantage for our customers through commercial efficiency, reliable machine design, extreme reliability and comprehensive support.
Usually, the important factors that affect the selection of injection molding machines include molds, products, plastics, molding requirements, etc. Therefore, before making a selection, it is necessary to collect or master such information: such as mold size (width, height, thickness), weight, special design, etc.; type and quantity of plastic used (single raw material or multiple plastics); appearance size ( length, width, height, thickness), weight of injection molded products, etc.; molding requirements, such as quality requirements, production speed, etc.
Headquartered in Austria and with 9 locations worldwide, ENGEL is the world's leading manufacturer of plastic injection molding machines. Besides machine building, it also offers a wide range of services. The company's main products include system solutions, electric, hydraulic and vertical injection molding machines, used machinery, control units, robots, process stabilization mechanisms, etc. Engel promises clamping forces of between 280 kN and 55,000 kN for its machines.
Milacron is a leading manufacturer of plastic injection molding machines and is a global leader in the manufacture, distribution and service of highly engineered and custom systems in the plastics and processing industries, with a full portfolio of injection molding and extrusion equipment . Milacron maintains a strong market position and maintains leadership in process control systems, maintenance, repair and operational supplies for plastics processing equipment. Milacron provides customers with highly customized equipment, components and services throughout the life cycle of their plastics processing technology systems.
Husky is a well-known manufacturer of plastic injection molding machines and the largest brand supplier of injection molding equipment and services to the plastics industry. The Husky team of more than 4,300 dedicated engineers, designers, innovators, materials and software experts around the world is focused on creating success and profitability for our customers in more than 140 countries.
Fanuc is a well-known CNC solution provider and plastic injection molding machine manufacturer. Teams of automation professionals work in customer service, engineering, finance, human resources, IT, logistics, operations, manufacturing, product development, sales and marketing, and training.
The width and height of the mold should be smaller than or at least one side should be smaller than the large column spacing; the width and height of the mold should preferably be within the range of the mold tray size; the thickness of the mold should be between the mold thickness of the plastic injection molding machine.
The headquarters of LNS Technologies are located in 241 kings village road, scotts valley, california 95066, united states.
Since there are many types of injection molding machines, it is necessary to correctly judge which type of injection molding machine or series should be used to produce the product, such as general thermoplastic or bakelite or PET material, single color, double color, multi-color-color, sandwich or mixed color . In addition, some products require conditions such as high stability (closed circuit), high precision, ultra-high injection speed, high injection pressure or rapid production (multi-circuit), and the appropriate series must also be selected for production.
Plastic injection molding is used to create a large variety of plastic products with different shapes and sizes, from toys and model parts to furniture and building materials. But injection molding is not just for big corporations with large budgets. The PIM-SHOOTER Model 150A manufactured by LNS Technologies brings affordable injection molding to home shops or small businesses. If you are designing prototype parts, this machine will save tons of turn-around time. No more waiting for the parts to be made overseas or by an outside firm. You will be able to manufacture plastic parts for your business in-house. This machine could easily pay for itself on the very first project! Inventors can use this machine to produce sample parts before spending for volume production. Univeristies, community colleges and high schools can use this machine as part of STEM and CNC classroom instruction. Ideal for R&D, Prototyping and Production runs.
Today, I would like to introduce you to the world's top 10 Plastic injection molding machine manufacturers, hoping to help you.
Shibaura Machinery is a well-known manufacturer and solutions provider of plastic injection molding machines, Shibaura designs and manufactures industrial machines and solutions to provide customers with optimum productivity and profitability, and to provide excellent service and support to maximize their return on investment . To pursue this goal, conduct business in a responsible and respectful manner, contribute to the industrial base, and help create a high-quality society through the continuous development of innovative technologies with a focus on mechanics, electronics and systems.
Plastic injection molding is used to create a large variety of plastic products with different shapes and sizes, from toys and model parts to furniture and building materials. But injection molding is not just for big corporations with large budgets. The PIM-SHOOTER Model 150A manufactured by LNS Technologies brings affordable injection molding to home shops or small businesses. If you are designing prototype parts, this machine will save tons of turn-around time. No more waiting for the parts to be made overseas or by an outside firm. You will be able to manufacture plastic parts for your business in-house. This machine could easily pay for itself on the very first project! Inventors can use this machine to produce sample parts before spending for volume production. Univeristies, community colleges and high schools can use this machine as part of STEM and CNC classroom instruction. Ideal for R&D, Prototyping and Production runs.
Finished weight and number of cavities are used to determine the required "shot volume" and to select the appropriate "screw diameter".
The clamping force of the machine should be greater than the clamping force. For the sake of safety, the clamping force of the machine usually needs to be greater than 1.17 times of the clamping force.
Servo injection molding machines claim to take advantage of the best features of both hydraulic and electric systems, but in actuality use almost the same amount of electricity to operate as an electric injection molding machine depending on the manufacturer.
Ningbo Chuangji Machinery Co., Ltd. is located in Yuyao. Is a professional enterprise engaged in plastic injection molding machinery. Since the official launch of LOG Lange presses in 2007, the company's sales network has spread all over the world. It has established more than 50 dealers in mainland China, in North and South America, the CIS, Southeast Asia, Africa, the Middle East, and even Europe. There are dealers and service outlets in more than 20 overseas countries around the world. The company currently has four injection molding machine bases, covering a total area of more than 70,000 square meters, with an annual production capacity of more than 4,000 units. The company always adheres to the management concept of "focus, professionalism and concentration", and pays great attention to talent construction and technology development. Strong independent research and development capabilities and strict quality supervision system make Lange brand injection molding machines have the characteristics of energy saving, high pressure and high speed, precision and stability.
Some engineering plastics require higher injection pressure and suitable screw compression ratio design to have better molding effect, so in order to make the finished product injection better, the selection of the screw also needs to consider the required ratio of injection pressure and compression ratio. .
When calculating the weight of the finished product, the number of cavities (how many cavities are in the mold) should be considered; for stability, the injection volume should be greater than 1.35 times the weight of the finished product, that is, the weight of the finished product should be within 75% of the injection volume.
In addition, in many cases, they will be classified by the function or application of the injection molding machine, such as our common PET preform injection molding machine, PVC Pipe injection molding machine, etc. Plastic Injection molding machine manufacturers usually prepare or customize corresponding injection molding solutions for you. You can ask your intended manufacturer in detail.
In this case, it may be necessary to check whether the injection volume and injection speed of the machine are sufficient, whether it needs to be equipped with an accumulator, closed-loop control, etc. Screws that can provide higher injection pressures generally have lower injection speeds, and conversely, screws that can provide lower injection pressures generally have higher injection speeds. Therefore, when selecting the screw diameter, the injection volume, injection pressure and injection speed (injection speed) should be comprehensively considered and weighed.
Headquarters and main manufacturing facilities are located in Canada, with additional manufacturing facilities in the United States, Luxembourg, Switzerland, China and the Czech Republic. In addition, three technical centers in Japan, Luxembourg and Shanghai, as well as a worldwide network of locations.
Clamping force = the projected area of ââthe finished product in the opening and closing direction (cm2) × the number of cavities × the pressure in the mold (kg/cm2).
Injection-molded parts are an indispensable part of modern production and life, occupying a very large share in the plastics processing industry. A high-end injection molding machine is very important due to its complexity, accuracy, manufacturing speed, etc.
With world-class "high cycle performance" as the core, through years of experience training, stronger and more evolved "long-life design" and "precise and stable molding" have been realized. In addition, it combines "advanced intelligence" with a new controller that is extremely easy to use. We respond to the diverse needs of various molding sites and contribute to improving productivity.
After getting the above information, you can follow the steps below to choose a suitable plastic injection molding machine
The width and height of the mold must conform to the minimum mold size recommended by the injection molding machine. Too small is not acceptable.
Hydraulic machines, although not nearly as precise, are the predominant type in most of the world, with the exception of Japan.
The electric press, also known as Electric Machine Technology (EMT), reduces operation costs by cutting energy consumption and also addresses some of the environmental concerns surrounding the hydraulic press. Electric presses have been shown to be quieter, faster, and have a higher accuracy, however the machines are more expensive.
Today, with the internationalization of the market and the diversification of customer needs, our company has always adhered to the attitude of taking the forming site as the starting point, relying on the professional technical strength accumulated since the establishment of the company, and adopting the one-to-one implementation strategy to solve various problems with customers. .
Since its establishment in 1947, NISSEI is a leading manufacturer of injection molding machines, and has continuously improved its professional and technical characteristics. With the concept of "professional, profound and extensive", it has gradually expanded the industry scope of related technology applications. While paying attention to improving the performance of injection molding machines, it also researches Developed molds, forming support systems, forming processing and other related technologies.
From the mold size, determine whether the machine's "large column spacing", "mold thickness", "mold minimum size" and "mold tray size" are appropriate to confirm whether the mold can be placed.
So far, the specifications of the clamping unit have been preliminarily determined, and the tonnage of the machine has been roughly determined. Next, the following steps must be performed again to confirm which injection unit has a better screw diameter.
JSW is a leading plastic injection molding machine manufacturer with many years of R&D manufacturing experience and extensive experience in manufacturing large electric injection molding machines ranging from 550 to 3000 metric tons.
The mold and finished product should determine whether the "opening stroke" and "clamping stroke" are sufficient to remove the finished product.
GETTING A QUOTE WITH LK-MOULD IS FREE AND SIMPLE.
FIND MORE OF OUR SERVICES:
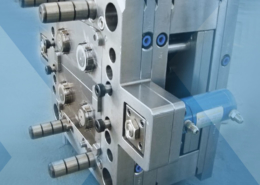
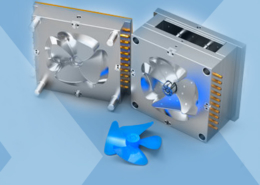
Plastic Molding

Rapid Prototyping
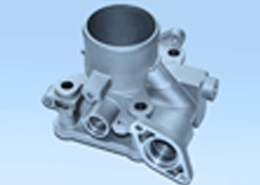
Pressure Die Casting
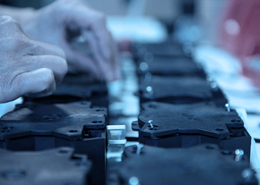
Parts Assembly
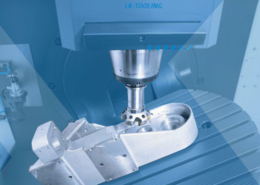