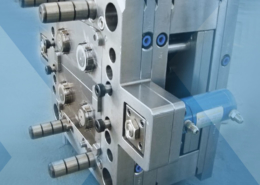
Exploring Large Part Injection Molding
Author:gly Date: 2024-06-08
In the realm of manufacturing, large part injection molding stands out as a technique of paramount importance, offering unparalleled advantages in the production of oversized plastic components. From automotive panels to industrial equipment, large part injection molding plays a crucial role in various industries. This article aims to delve into the intricacies of large part injection molding, unraveling its significance, capabilities, challenges, and future prospects.
Introduction to Large Part Injection Molding
Large part injection molding involves the fabrication of plastic components exceeding traditional size limits. This process utilizes specialized equipment and techniques to produce oversized parts with precision and efficiency. With advancements in machinery, materials, and mold design, large part injection molding has emerged as a cost-effective solution for manufacturing complex, large-scale components.
Key Considerations in Large Part Injection Molding
Equipment and Machinery
Large part injection molding necessitates robust machinery capable of accommodating oversized molds and handling high-tonnage clamping forces. Injection molding machines with extended platens, wide tie-bar spacing, and enhanced hydraulic systems are essential for ensuring mold stability, part quality, and production efficiency.
Mold Design and Fabrication
The design and fabrication of molds for large parts present unique challenges due to increased size, weight, and complexity. Meticulous attention to detail is required to optimize mold cooling, gate placement, and material flow, minimizing defects such as warpage, sink marks, and voids. Collaborative efforts between mold designers, engineers, and manufacturers are critical for achieving optimal part performance and quality.
Material Selection and Processing
Choosing the right materials is crucial in large part injection molding to meet performance requirements while minimizing costs. Engineering resins, such as ABS, PC, and nylon, offer excellent strength, durability, and dimensional stability for large components. Additionally, processing parameters must be carefully controlled to ensure uniform material distribution, proper fill, and optimal cycle times.
Advantages of Large Part Injection Molding
Cost Efficiency
Large part injection molding enables the production of oversized components in a single operation, eliminating the need for secondary assembly processes. This reduces labor costs, material waste, and lead times associated with multi-part assemblies, enhancing overall cost efficiency and competitiveness.
Design Freedom
The versatility of large part injection molding allows for intricate designs and complex geometries that would be impractical or impossible to achieve through other manufacturing methods. Design freedom enables engineers to optimize part functionality, aesthetics, and performance, opening up new possibilities for product innovation and differentiation.
Scalability
Large part injection molding is inherently scalable, accommodating varying production volumes and batch sizes with minimal adjustments. From low-volume prototypes to high-volume productions, injection molding offers flexibility and scalability to meet evolving market demands and customer requirements.
Challenges and Future Directions
Tooling Complexity
The fabrication of molds for large parts involves significant upfront costs and lead times, posing challenges for manufacturers, particularly in niche or custom applications. Innovations in mold design, additive manufacturing, and rapid prototyping offer potential solutions to reduce tooling complexity and accelerate time-to-market.
Sustainability
As sustainability becomes increasingly important in manufacturing, large part injection molding faces pressure to minimize environmental impact and promote circular economy principles. Integration of recycled materials, biodegradable resins, and energy-efficient processes can enhance sustainability while maintaining performance and cost-effectiveness.
Digitalization and Automation
The adoption of digitalization and automation technologies holds promise for optimizing large part injection molding processes, improving efficiency, and reducing operational costs. Predictive maintenance, real-time monitoring, and data analytics enable proactive decision-making and continuous improvement, driving competitiveness and profitability in the long term.
Conclusion
Large part injection molding represents a cornerstone of modern manufacturing, offering unparalleled capabilities in the production of oversized plastic components. By leveraging advanced equipment, materials, and processes, manufacturers can achieve cost-effective solutions, design freedom, and scalability to meet diverse market demands. Despite challenges such as tooling complexity and sustainability concerns, ongoing innovations in technology and process optimization pave the way for a brighter future for large part injection molding. As industries continue to evolve and demand larger, more complex components, the role of large part injection molding will remain indispensable in shaping the landscape of manufacturing.
GETTING A QUOTE WITH LK-MOULD IS FREE AND SIMPLE.
FIND MORE OF OUR SERVICES:
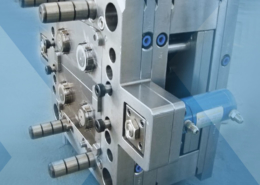
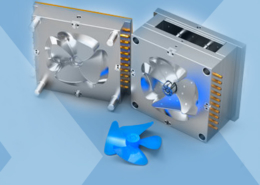
Plastic Molding

Rapid Prototyping
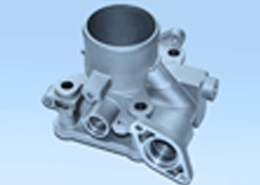
Pressure Die Casting
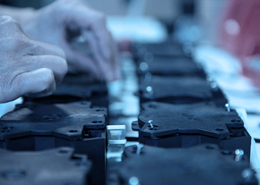
Parts Assembly
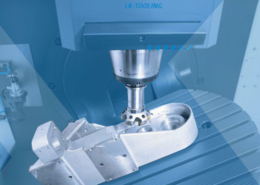