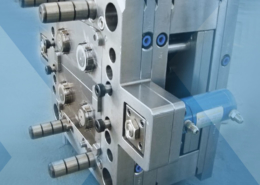
Exploring Large Plastic Molds: Precision in Production
Author:gly Date: 2024-06-08
Large plastic molds play a pivotal role in modern manufacturing, facilitating the mass production of a wide range of plastic components used in various industries. From automotive parts and household appliances to consumer electronics and medical devices, large plastic molds enable the efficient and cost-effective production of complex geometries with tight tolerances. This article delves into the realm of large plastic molds, shedding light on their significance, applications, design considerations, and future prospects.
Significance of Large Plastic Molds
Driving Innovation and Efficiency
Large plastic molds are instrumental in driving innovation and efficiency across diverse industries. By enabling the mass production of intricate plastic components, these molds facilitate the realization of innovative designs and technological advancements. Moreover, large-scale production using plastic molds enhances efficiency by reducing lead times, minimizing material waste, and optimizing production processes. As a result, manufacturers can meet market demands more effectively while maintaining a competitive edge in the global marketplace.
Versatility and Adaptability
Large plastic molds exhibit remarkable versatility and adaptability, allowing manufacturers to produce a wide range of components in varying shapes, sizes, and materials. Whether it's automotive body panels, electronic enclosures, or medical device housings, large plastic molds can accommodate diverse requirements with precision and consistency. This versatility enables manufacturers to cater to evolving consumer preferences, adapt to changing market trends, and explore new business opportunities in emerging sectors.
Cost-Effectiveness and Scalability
Large plastic molds offer significant cost savings and scalability advantages compared to alternative manufacturing methods. Once the initial mold is fabricated, the cost per part decreases substantially with each additional unit produced, making large-scale production economically viable. Furthermore, the scalability of plastic molding processes allows manufacturers to ramp up production quickly in response to increased demand, without compromising quality or consistency. This cost-effectiveness and scalability make large plastic molds an attractive choice for businesses seeking efficient and sustainable manufacturing solutions.
Design Considerations for Large Plastic Molds
Complexity of Mold Geometry
The design of large plastic molds must account for the complexity of the part geometry, including intricate features, undercuts, and draft angles. Complex geometries present unique challenges in mold design, such as ensuring uniform cooling, preventing warpage, and minimizing cycle times. Utilizing advanced CAD software and simulation tools, mold designers can analyze and optimize mold geometry to achieve optimal part quality and production efficiency. Moreover, innovative mold design techniques, such as conformal cooling and multi-cavity molds, can further enhance performance and productivity.
Material Selection and Compatibility
Selecting the appropriate material for large plastic molds is crucial to ensuring durability, longevity, and compatibility with the intended production environment. Factors such as temperature resistance, wear resistance, and chemical compatibility must be carefully considered when choosing mold materials. Additionally, advancements in composite materials and surface coatings offer opportunities to enhance mold performance and extend service life. By selecting high-quality materials and employing robust manufacturing processes, manufacturers can mitigate the risk of mold failure and maximize return on investment.
Tooling and Equipment Requirements
Large plastic molds require specialized tooling and equipment to withstand the forces and pressures involved in the molding process. From injection molding machines and mold bases to hot runners and cooling systems, every component of the molding system must be designed and engineered for reliability and efficiency. Collaborating with experienced mold manufacturers and equipment suppliers can help ensure that the tooling and equipment meet the specific requirements of large-scale production. Moreover, investing in preventive maintenance and regular servicing can prolong the lifespan of molds and minimize downtime, thereby optimizing production uptime and throughput.
Future Prospects and Emerging Trends
Advancements in Additive Manufacturing
The integration of additive manufacturing technologies, such as 3D printing, into the realm of large plastic molds holds immense potential for innovation and efficiency. Additive manufacturing allows for the rapid prototyping of mold components, complex geometries, and customized tooling with reduced lead times and costs. Furthermore, the ability to iterate designs on-the-fly enables manufacturers to optimize mold performance and adapt to changing production requirements more effectively. As additive manufacturing continues to mature, its role in large plastic mold fabrication is expected to expand, ushering in a new era of flexibility and customization in manufacturing.
Sustainable Manufacturing Practices
With growing emphasis on environmental sustainability, manufacturers are increasingly adopting eco-friendly materials, processes, and practices in large plastic mold fabrication. From biodegradable resins and recycled plastics to energy-efficient molding processes and closed-loop recycling systems, sustainable manufacturing initiatives are reshaping the landscape of plastic molding. By minimizing waste, reducing energy consumption, and optimizing resource utilization, manufacturers can not only reduce their environmental footprint but also enhance operational efficiency and corporate social responsibility. As sustainability becomes a driving force in manufacturing, integrating sustainable practices into large plastic mold fabrication will be critical for long-term success and competitiveness.
Conclusion
In conclusion, large plastic molds represent a cornerstone of modern manufacturing, enabling the efficient and cost-effective production of complex plastic components on a large scale. From driving innovation and efficiency to offering versatility and scalability, these molds play a vital role in shaping various industries and driving economic growth. By considering key design considerations, embracing emerging trends, and adopting sustainable practices, manufacturers can harness the full potential of large plastic molds to meet the evolving demands of the market and propel their businesses forward into the future. As we continue to push the boundaries of possibility in manufacturing, large plastic molds will remain at the forefront of innovation, driving progress and shaping the world around us.
GETTING A QUOTE WITH LK-MOULD IS FREE AND SIMPLE.
FIND MORE OF OUR SERVICES:
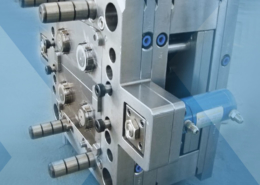
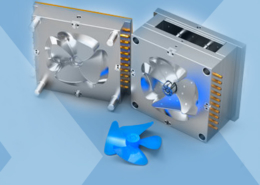
Plastic Molding

Rapid Prototyping
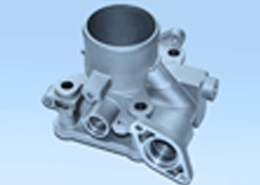
Pressure Die Casting
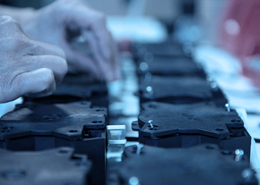
Parts Assembly
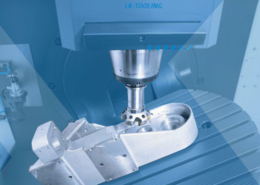