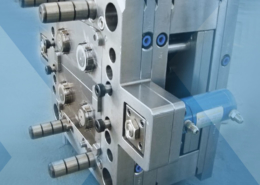
Exploring the Versatility of L-Shaped Plastic Molding
Author:gly Date: 2024-06-08
Introduction
L-shaped plastic molding stands as a hallmark of innovation and functionality in the field of manufacturing. This article delves into the intricacies of L-shaped plastic molding, unraveling its applications, advantages, and transformative potential in various industries. From its inception to modern-day advancements, we embark on a journey to understand the profound impact of L-shaped plastic molding on shaping our world.
Understanding L-Shaped Plastic Molding Technology
L-shaped plastic molding represents a convergence of design and engineering, allowing for the creation of complex geometries with precision and efficiency. At its core, this process involves heating plastic resins to a molten state and injecting them into molds with L-shaped cavities. The cooling and solidification of the plastic result in the formation of L-shaped components with seamless edges and intricate details.
Injection molding is the predominant technique employed in L-shaped plastic molding, offering unparalleled precision and repeatability. The versatility of this method allows for the production of L-shaped components ranging from small electronic parts to large automotive panels, catering to diverse industry needs.
Applications Across Industries
The applications of L-shaped plastic molding span across a multitude of industries, showcasing its adaptability and versatility. In the furniture sector, L-shaped plastic components find use in the construction of modular shelving units, ergonomic chairs, and stylish fixtures, where design aesthetics and functionality converge.
In the automotive industry, L-shaped plastic molding plays a crucial role in fabricating interior trim panels, dashboard components, and structural reinforcements. The lightweight nature of plastic, coupled with the ability to mold complex shapes, contributes to fuel efficiency and vehicle performance.
Moreover, the electronics sector leverages L-shaped plastic molding for the production of enclosures, connectors, and housing assemblies for electronic devices. The precise molding of L-shaped components ensures optimal fit and alignment, enhancing the reliability and longevity of electronic products.
Advantages and Innovations
The adoption of L-shaped plastic molding is driven by its myriad advantages, including cost-effectiveness, design flexibility, and durability. Unlike traditional materials such as metal or wood, plastic offers greater design freedom, allowing for the incorporation of intricate features and geometries without compromising structural integrity.
Furthermore, ongoing innovations in material science and molding technology continue to expand the capabilities of L-shaped plastic molding. The development of reinforced plastics, biodegradable polymers, and advanced surface finishes opens new possibilities for applications in aerospace, medical, and consumer goods sectors.
Sustainability and Future Directions
As the global emphasis on sustainability grows, L-shaped plastic molding is evolving to meet the demands of eco-conscious consumers and regulatory standards. The recyclability of plastics and the adoption of recycled materials in molding processes offer a pathway towards reducing environmental impact and promoting circular economy principles.
Moreover, research efforts are underway to explore alternative materials and manufacturing techniques that further enhance the sustainability of L-shaped plastic molding. Bio-based polymers, additive manufacturing, and closed-loop recycling systems hold promise for shaping the future of plastic molding towards a more sustainable and resilient industry.
Conclusion
In conclusion, L-shaped plastic molding represents a fusion of creativity, precision, and functionality, driving innovation across industries. From furniture to automotive to electronics, its applications are diverse and far-reaching, shaping the way we live, work, and interact with our environment.
As we look towards the future, the continued advancement of L-shaped plastic molding holds immense potential for addressing global challenges and driving sustainable development. By embracing innovation, collaboration, and responsible manufacturing practices, we can harness the full potential of L-shaped plastic molding to create a brighter, more sustainable future for generations to come.
GETTING A QUOTE WITH LK-MOULD IS FREE AND SIMPLE.
FIND MORE OF OUR SERVICES:
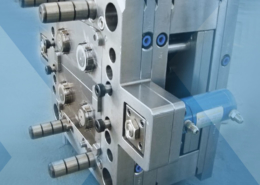
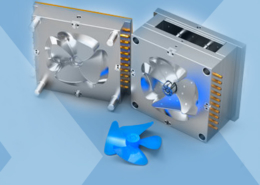
Plastic Molding

Rapid Prototyping
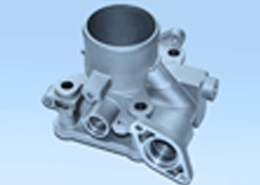
Pressure Die Casting
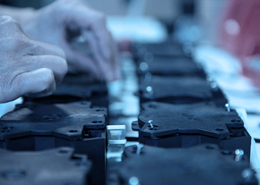
Parts Assembly
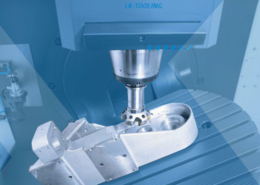