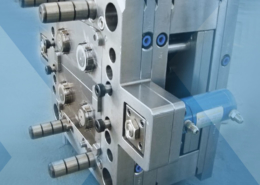
Exploring Kilang Plastic Injection Moulding: Innovating the Future of Manufactur
Author:gly Date: 2024-06-08
In the realm of modern manufacturing, Kilang Plastic Injection Moulding stands as a beacon of innovation and efficiency. This article delves into the intricacies of this technology, offering insights into its processes, applications, and significance in shaping industries worldwide.
1. Origins and Evolution
Kilang Plastic Injection Moulding traces its origins back to the mid-20th century, paralleling the rise of plastic as a versatile material in various industries. Developed initially as a means to streamline production processes, it has since evolved into a sophisticated method with diverse applications across sectors.
The evolution of Kilang Plastic Injection Moulding is marked by advancements in materials science, machinery, and computer-aided design (CAD) technologies. These innovations have propelled the technique from simple moulding processes to highly precise and customizable manufacturing solutions.
2. Precision and Efficiency
At the heart of Kilang Plastic Injection Moulding lies its unparalleled precision and efficiency. By injecting molten plastic into meticulously crafted moulds at high pressures, this technique enables the production of intricate and complex components with minimal material wastage.
The precision offered by Kilang Plastic Injection Moulding is paramount in industries such as automotive, electronics, and medical devices, where even minor deviations can compromise performance and safety. Moreover, its efficiency in mass production ensures cost-effectiveness and timely delivery of goods to meet market demands.
3. Versatility and Customization
One of the defining characteristics of Kilang Plastic Injection Moulding is its versatility and customization capabilities. With the ability to accommodate a wide range of thermoplastics and additives, manufacturers can tailor the properties of the final product to meet specific requirements.
From color variations to material compositions, Kilang Plastic Injection Moulding offers unparalleled flexibility in product design. This versatility is invaluable in industries where aesthetics, functionality, and performance are paramount, enabling manufacturers to stay ahead in competitive markets.
4. Sustainability and Environmental Impact
Despite its numerous advantages, Kilang Plastic Injection Moulding is not without environmental considerations. The widespread use of plastics raises concerns about waste management and pollution, prompting the industry to explore sustainable alternatives and recycling initiatives.
Efforts to mitigate the environmental impact of Kilang Plastic Injection Moulding include the adoption of bio-based plastics, optimization of production processes to minimize energy consumption, and the implementation of closed-loop recycling systems. These initiatives aim to promote eco-friendly practices while maintaining the efficiency and functionality of the manufacturing process.
Conclusion: Shaping the Future of Manufacturing
In conclusion, Kilang Plastic Injection Moulding stands as a cornerstone of modern manufacturing, offering precision, efficiency, versatility, and customization unparalleled by traditional methods. However, its continued evolution must be guided by a commitment to sustainability and environmental responsibility.
As industries embrace digitalization and automation, Kilang Plastic Injection Moulding is poised to play an even greater role in shaping the future of manufacturing. By leveraging emerging technologies such as artificial intelligence and additive manufacturing, the industry can further enhance efficiency, reduce waste, and unlock new possibilities in product design and production.
In the quest for innovation and progress, it is imperative that stakeholders across industries collaborate to harness the full potential of Kilang Plastic Injection Moulding while safeguarding the planet for future generations. Only through concerted efforts can we ensure that this transformative technology continues to drive economic growth and societal advancement in a sustainable manner.
GETTING A QUOTE WITH LK-MOULD IS FREE AND SIMPLE.
FIND MORE OF OUR SERVICES:
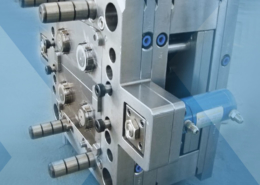
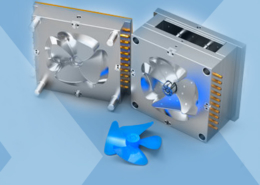
Plastic Molding

Rapid Prototyping
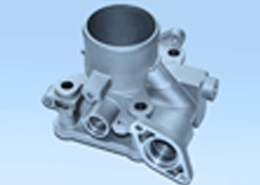
Pressure Die Casting
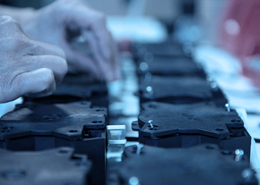
Parts Assembly
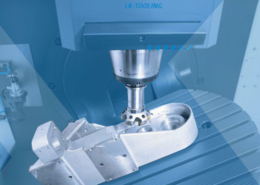