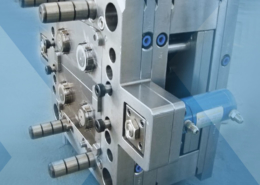
The Versatility of Injection Moldable Plastics: A Comprehensive Overview
Author:gly Date: 2024-06-08
Injection moldable plastics have revolutionized manufacturing processes across industries, offering a versatile solution for producing intricate and customized components with efficiency and precision. This article delves into the multifaceted world of injection moldable plastics, exploring their properties, applications, advancements, and future prospects.
The Basics
Injection moldable plastics, also known as injection-molded polymers, are thermoplastics that are heated to a molten state and injected into a mold cavity under high pressure. Once cooled and solidified, they take the shape of the mold, resulting in complex geometries with tight tolerances. This process offers advantages such as rapid production, scalability, and design flexibility, making it indispensable in various industries ranging from automotive and electronics to healthcare and consumer goods.
Properties and Characteristics
The properties of injection moldable plastics vary depending on the type of polymer used, such as polyethylene (PE), polypropylene (PP), polystyrene (PS), and acrylonitrile butadiene styrene (ABS). These materials exhibit a wide range of characteristics, including high strength-to-weight ratios, chemical resistance, thermal stability, and electrical insulation. Additionally, additives such as fillers, reinforcements, and flame retardants can further enhance their performance and tailor them to specific applications.
Applications Across Industries
The versatility of injection moldable plastics enables their utilization in diverse applications. In the automotive sector, they are used for interior components, exterior trims, and under-the-hood parts, offering lightweight alternatives to metal counterparts while meeting stringent safety and durability requirements. In the electronics industry, they find applications in housing for electronic devices, connectors, and insulating components, providing excellent dielectric properties and design freedom. Moreover, injection moldable plastics play a crucial role in medical devices, packaging, toys, and household appliances, illustrating their ubiquitous presence in everyday life.
Advancements and Innovations
Recent advancements in materials science and manufacturing technologies have expanded the capabilities of injection moldable plastics. The development of bio-based polymers derived from renewable sources addresses concerns about environmental sustainability, offering biodegradable alternatives to traditional plastics. Furthermore, the integration of additive manufacturing techniques such as 3D printing with injection molding processes enables the production of complex hybrid structures with customized properties, opening new avenues for product design and prototyping.
Challenges and Future Directions
Despite their numerous advantages, injection moldable plastics face challenges related to material selection, process optimization, and environmental impact. Addressing these challenges requires interdisciplinary research efforts focusing on sustainable materials, recycling technologies, and waste reduction strategies. Additionally, advancements in digital design tools, predictive modeling, and in-situ monitoring techniques can enhance the efficiency and reliability of injection molding processes, paving the way for the widespread adoption of these materials in emerging industries such as aerospace, renewable energy, and advanced manufacturing.
In conclusion, injection moldable plastics represent a cornerstone of modern manufacturing, offering unparalleled versatility, efficiency, and customization capabilities. As industries continue to evolve and demand for innovative solutions grows, the role of injection moldable plastics will only become more pronounced. By leveraging advancements in materials science, process engineering, and sustainability initiatives, we can harness the full potential of these materials to shape a more sustainable and technologically advanced future.
GETTING A QUOTE WITH LK-MOULD IS FREE AND SIMPLE.
FIND MORE OF OUR SERVICES:
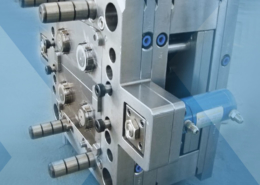
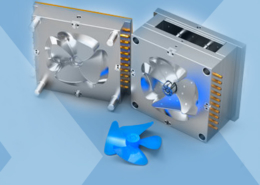
Plastic Molding

Rapid Prototyping
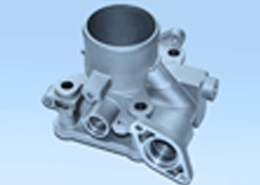
Pressure Die Casting
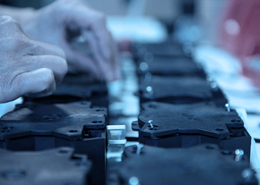
Parts Assembly
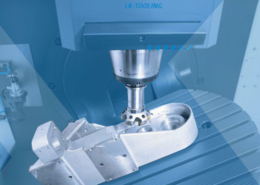