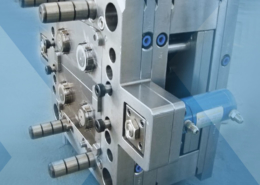
Understanding Injection Mold Tooling Cost
Author:gly Date: 2024-06-08
Injection mold tooling cost is a critical aspect of manufacturing processes across various industries. From automotive to consumer goods, injection molding is a widely used method for mass-producing components. However, the cost associated with tooling can significantly impact the feasibility and profitability of a project. This article delves into the complexities of injection mold tooling cost, exploring various facets to provide a comprehensive understanding for stakeholders in the manufacturing sector.
Importance of Injection Mold Tooling Cost
Injection mold tooling cost encompasses expenses related to the design, creation, and maintenance of molds used in injection molding processes. These molds are essential for shaping raw materials into desired forms with precision and consistency. The significance of understanding tooling cost lies in its direct influence on production expenses, product quality, and time-to-market. High tooling costs can escalate project budgets, leading to reduced competitiveness and profitability.
Factors Influencing Tooling Cost
Design Complexity
The intricacy of part designs significantly impacts tooling cost. Complex geometries require more sophisticated molds, driving up expenses in tooling design, machining, and finishing. Features such as undercuts, thin walls, and intricate details necessitate specialized tooling techniques, adding complexity and cost to the manufacturing process.
Material Selection
The choice of materials for both the part and the mold influences tooling cost. High-performance thermoplastics or engineering resins may require specialized molds capable of withstanding elevated temperatures and pressures. Moreover, certain materials may necessitate additional surface treatments or coatings to enhance mold durability and longevity, further increasing tooling expenses.
Production Volume
Production volume plays a pivotal role in determining tooling cost per unit. While high-volume projects allow for amortizing tooling expenses over a larger number of units, low-volume productions may result in higher per-unit tooling costs. Manufacturers must carefully analyze production forecasts and consider economies of scale to optimize tooling expenditure and maximize cost-effectiveness.
Tooling Complexity
Apart from part design complexity, the intricacy of the tooling itself impacts cost. Multi-cavity molds enable simultaneous production of multiple parts, offering economies of scale but requiring higher initial investment. Additionally, the choice between standard molds and custom-built solutions influences tooling cost, with bespoke options offering tailored functionalities at a premium price.
Mitigating Tooling Costs
Design Optimization
Early involvement of design engineers can facilitate cost-effective part designs optimized for injection molding. Design for Manufacturability (DFM) principles aim to minimize tooling complexity and material waste while enhancing part quality and manufacturability. By reducing the need for intricate features and minimizing tooling modifications, manufacturers can mitigate tooling costs without compromising product performance.
Material Rationalization
Selecting cost-effective materials that meet performance requirements is crucial for controlling tooling expenses. Material rationalization involves evaluating alternative materials with comparable properties at lower costs. Collaboration between design, engineering, and procurement teams can identify suitable material substitutions, reducing tooling expenditure without compromising product integrity.
Strategic Supplier Partnerships
Establishing long-term relationships with reliable tooling suppliers can yield cost savings through volume discounts, preferential pricing, and shared expertise. Collaborative partnerships enable manufacturers to leverage supplier capabilities for tooling design, optimization, and maintenance, fostering continuous improvement and cost reduction initiatives.
Conclusion
Injection mold tooling cost is a multifaceted aspect of manufacturing that demands careful consideration and strategic management. By understanding the factors influencing tooling expenses and implementing cost-saving measures, manufacturers can enhance competitiveness, optimize project budgets, and accelerate time-to-market. Embracing design optimization, material rationalization, and strategic partnerships empowers stakeholders to navigate the complexities of injection mold tooling cost effectively, driving sustainable growth and innovation in the manufacturing industry.
GETTING A QUOTE WITH LK-MOULD IS FREE AND SIMPLE.
FIND MORE OF OUR SERVICES:
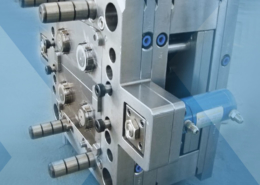
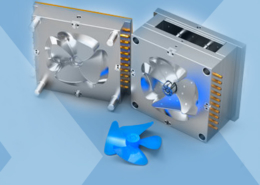
Plastic Molding

Rapid Prototyping
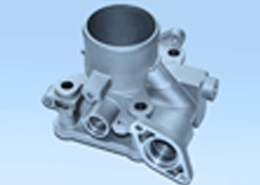
Pressure Die Casting
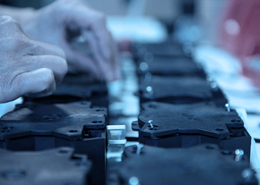
Parts Assembly
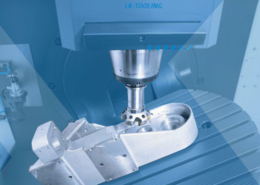