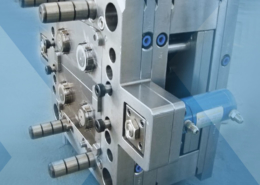
Exploring the Versatility of Injection Molding Acetal
Author:gly Date: 2024-06-08
Injection molding acetal stands as a cornerstone in modern manufacturing, offering unparalleled versatility, durability, and dimensional stability. This article aims to pique readers' interest by introducing the concept of injection molding acetal and providing background information on its significance in various industries.
Introduction to Injection Molding Acetal
Injection molding acetal, also known as polyoxymethylene (POM), is a thermoplastic polymer renowned for its exceptional mechanical properties and ease of processing. Widely used in industries such as automotive, electronics, and consumer goods, acetal exhibits high strength, stiffness, and chemical resistance, making it an ideal choice for a wide range of applications.
Advantages of Injection Molding Acetal
Injection molding acetal offers several advantages over other materials and manufacturing processes.
High Mechanical Strength
Acetal boasts impressive mechanical properties, including high tensile strength, stiffness, and impact resistance. These properties make it suitable for applications where structural integrity and durability are paramount, such as gears, bearings, and automotive components.
Dimensional Stability
One of the key advantages of acetal is its excellent dimensional stability, even in harsh environments or fluctuating temperatures. This property ensures tight tolerances and consistent part dimensions, making it ideal for precision components in electronics, medical devices, and aerospace applications.
Chemical Resistance
Acetal exhibits excellent resistance to a wide range of chemicals, including solvents, fuels, and lubricants. This chemical resistance makes it suitable for applications where exposure to harsh substances is common, such as fuel system components, pump parts, and chemical processing equipment.
Process Overview
The process of injection molding acetal involves several key steps, from material selection to part production.
Material Selection
The first step in injection molding acetal is selecting the appropriate acetal grade based on the specific requirements of the application. Factors such as mechanical properties, chemical resistance, and thermal stability are considered when choosing the optimal material for the intended use.
Mold Design
Once the material is selected, the mold design process begins, taking into account part geometry, gate location, cooling channels, and ejection mechanisms. Advanced mold design software allows for the creation of complex molds that optimize part quality, cycle time, and production efficiency.
Injection Molding
The injection molding process begins with the melting of acetal resin pellets in the barrel of an injection molding machine. The molten material is then injected into a mold cavity under high pressure, where it cools and solidifies to form the desired part. After cooling, the mold opens, and the molded part is ejected, trimmed, and finished as needed.
Applications
Injection molding acetal finds applications across a wide range of industries, thanks to its versatility and performance characteristics.
Automotive
In the automotive industry, acetal is used for various components such as gears, bushings, connectors, and interior trim pieces. Its high strength, low friction, and wear resistance make it ideal for demanding automotive applications where durability and performance are critical.
Electronics
In the electronics industry, acetal is utilized for components such as connectors, switches, housings, and insulators. Its dimensional stability, electrical properties, and resistance to moisture and chemicals make it well-suited for applications requiring reliability and performance in challenging environments.
Consumer Goods
Acetal is also widely used in the production of consumer goods such as sporting equipment, tools, and household appliances. Its combination of strength, stiffness, and ease of processing makes it an attractive choice for manufacturers seeking high-performance materials for consumer products.
Future Directions
Looking ahead, the future of injection molding acetal holds promise for further innovation and advancement. Continued research into material formulations, process optimization, and sustainability initiatives will likely expand the applications and capabilities of acetal, opening up new opportunities for manufacturers across industries.
Conclusion
In conclusion, injection molding acetal represents a cornerstone in modern manufacturing, offering unparalleled versatility, durability, and performance for a wide range of applications. From automotive to electronics to consumer goods, acetal continues to play a vital role in driving innovation, efficiency, and reliability in various industries. By understanding the intricacies of injection molding acetal and embracing its potential, manufacturers can unlock new opportunities for product development, cost savings, and market competitiveness.
GETTING A QUOTE WITH LK-MOULD IS FREE AND SIMPLE.
FIND MORE OF OUR SERVICES:
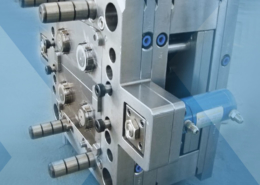
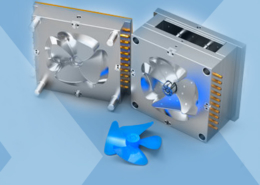
Plastic Molding

Rapid Prototyping
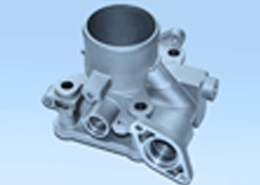
Pressure Die Casting
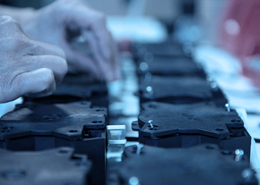
Parts Assembly
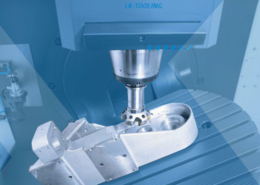